The design and processing of a 3D-printed high-performance biological fixation plate
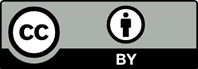
In order to generate a high-performance personalized biological fixation plate with matching mechanical properties and biocompatibility, reverse reconstruction and fracture reduction of a femur were performed by combining reverse and forward approaches, and the surface was extracted according to the installation position of the plate to complete plate modeling by shifting, thickening, and performing other operations. Subsequently, topology optimization and three-dimensional (3D) printing were performed, and the properties of the manufactured plate were probed. The results showed that the maximum displacement of the plate was 4.13 mm near the femoral head, the maximum stress was 5.15e2 MPa on both sides of the plate across its entire length, and the stress concentration decreased following topology optimization. The plate with optimized topology and filled with porous structure has a good filling effect. The final mass of the H-shaped plate was 12.05 g, while that of the B-shaped plate was 11.05 g, which dropped by 20.93% and 27.49%, respectively, compared with the original plate. The surface of the 3D-printed plate was bright and new, with a clear pore structure and good lap joint. The B-shaped and H-shaped plates were closely dovetailed with the host bone, which met the assembly requirements. This lays a foundation for the direct application of a high-performance personalized biological fixation plate.
1. Wu C, Zheng Z, Chen X, et al., 2016, Digital internal fixation of bone plate based on 3D printing of standard parts library of distal femoral fracture. China Tissue Eng Res, 20(13):1895–1903.
2. Zhang C, Jia D, Li F, et al., 2021, Design and simulation of titanium alloy lattice bone plate for 3D printing. J Shanghai Jiaotong Univ, 55(02):170–178.
3. Xu Y, Liu B, Zhang Y, et al., 2019, Analysis of the application effect of S2 alar screw in 23 cases of complex lower lumbar surgery. Fujian Med J, 41(02):37–40.
4. Zhang G, Li J, Li J, et al., 2021. Selective laser melting molding of individualized femur implant: Design, process, optimization. J Bionic Eng, 18(1):128–137.
5. García-León RA, Gómez-Camperos JA, Jaramillo HY, 2021, Scientometric review of trends on the mechanical properties of additive manufacturing and 3D printing. J Mater Eng Perform, 30(7), 4724–4734.
6. Caminero MN, Gutiérrez AR, Chacón Muoz JM, et al., 2021. Additive manufacturing of 316L stainless-steel structures using fused filament fabrication technology: Mechanical and geometric properties. Rapid Prototyp J, 27(3), 583–591.
7. Wu H, Li J, Wei Z, et al., 2020, Effect of processing parameters on forming defects during selective laser melting of AlSi10Mg powder. Rapid Prototyp J, 26 (5) , 871–879.
8. Hu X, He M, Min L, et al., 2020, Early efficacy evaluation of 3D printed porous metal support prosthesis in the treatment of Campanacci grade I and II giant cell tumor of bone in the proximal tibia. Chin J Bone Joint Surg, 13(12):1023–1029.
9. Li Z, Xue J, 2019, Research progress on the effect of 3D printed porous titanium alloy pore structure on bone induction. Chin J Orthop Clin Basic Res, 11(06):358–363.
10. Jia D, Li F, Zhang C, et al., 2019, Design and simulation analysis of lattice bone plate based on finite element method. Mech Adv Mater Struct, 28(13), 1311–1321.
11. Pobloth AM, Checa S, Razi H, et al., 2018, Mechanobiologically optimized 3D titanium-mesh scaffolds enhance bone regeneration in critical segmental defects in sheep. Sci Transl Med, 10(423):eaam8828.
12. Wang L, Kang J, Sun C, et al., 2017, Mapping porous microstructures to yield desired mechanical properties for application in 3D printed bone scaffolds and orthopaedic implants. Mater Design, 133:62–68.
13. Kanu NJ, Patwardhan D, Gupta E, et al., 2020, Finite element analysis of mechanical response of fracture fixation functionally graded bone plate at paediatric femur bone fracture site under compressive and torsional loadings. Mater Today Proc, 38:2817–2823.
14. Smith KE, Dupont KM, Safranski DL, et al., 2016, Use of 3D printed bone plate in novel technique to surgically correct hallux valgus deformities. Tech Orthop, 31(3):181.
15. Adam GAO, Zimmer D, 2014, Design for additive manufacturing—Element transitions and aggregated structures. CIRP J Manuf Sci Technol, 7(1):20–28.
16. Kranz J, Herzog D, Emmelmann C, 2015, Design guidelines for laser additive manufacturing of lightweight structures in Ti Al6V4. J Laser Appl, 27(S1):S14001.