Considerations Using Additive Manufacture of Emulsion Inks to Produce Respiratory Protective Filters Against Viral Respiratory Tract Infections Such as the COVID-19 Virus
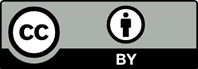
This review paper explores the potential of combining emulsion-based inks with additive manufacturing (AM) to produce filters for respiratory protective equipment (RPE) in the fight against viral and bacterial infections of the respiratory tract. The value of these filters has been highlighted by the current severe acute respiratory syndrome coronavirus-2 crisis where the importance of protective equipment for health care workers cannot be overstated. Three-dimensional (3D) printing of emulsions is an emerging technology built on a well-established field of emulsion templating to produce porous materials such as polymerized high internal phase emulsions (polyHIPEs). PolyHIPE-based porous polymers have tailorable porosity from the submicron to 100 s of µm. Advances in 3D printing technology enables the control of the bulk shape while a micron porosity is controlled independently by the emulsion-based ink. Herein, we present an overview of the current polyHIPE-based filter applications. Then, we discuss the current use of emulsion templating combined with stereolithography and extrusionbased AM technologies. The benefits and limitation of various AM techniques are discussed, as well as considerations for a scalable manufacture of a polyHIPE-based RPE.
1. Joshi SC, Sheikh AA, 2015, 3D printing in aerospace and its long-term sustainability. Virtual Phys Prototyping, 10:175–85. https://doi.org/10.1080/17452759.2015.1111519
2. Conner BP, Manogharan GP, Martof AN, et al., 2014, Making Sense of 3-D Printing: Creating a Map of Additive Manufacturing Products and Services. Addit Manuf, 1:64–76. https://doi.org/10.1016/j.addma.2014.08.005
3. Ng WL, Chua CK, Shen YF, 2019, Print me an organ? Why we are not there yet. Progress Polymer Sci, 97:101145. https://doi.org/10.1016/j.progpolymsci.2019.101145
4. Tino R, Moore R, Antoline S, et al., 2020, COVID-19 and the Role of 3D Printing in Medicine. Springer, Berlin, Germany.
5. Celik HK, Kose O, Ulmeanu ME, et al., 2020, Design and Additive Manufacturing of a Medical Face Shield for Healthcare Workers Battling Coronavirus (COVID-19). Int J Bioprint, 6:286. https://doi.org/10.18063/ijb.v6i4.286
6. Cook TM, 2020, Personal protective equipment during the coronavirus disease (COVID) 2019 pandemic-a narrative review. Anaesthesia, 75:920–7. https://doi.org/10.1111/anae.15071
7. Public Health England, 2020, COVID-19: Infection Prevention and Control Guidance. Public Health England, United Kingdom, England.
8. Chen N, Zhou M, Dong X, et al., 2020, Epidemiological and Clinical Characteristics of 99 Cases of 2019 Novel Coronavirus Pneumonia in Wuhan, China: A Descriptive Study. Lancet, 395:507–13. https://doi.org/10.1016/s0140-6736(20)30211-7
9. World Health Organization, 2020, Rational Use of Personal Protective Equipment (PPE) for Coronavirus Disease (COVID-19): Interim Guidance. World Health Organization, Geneva, Switzerland.
10. Cheng VC, Wong SC, Chuang VW, et al., 2020, The Role of Community-wide Wearing of Face Mask for Control of Coronavirus Disease 2019 (COVID-19) Epidemic Due to SARS-CoV-2. J Infect, 81:107–14. https://doi.org/10.1016/j.jinf.2020.04.024
11. Vuorinen V, Aarnio M, Alava M, et al., 2020, Modelling Aerosol Transport and Virus Exposure with Numerical Simulations in Relation to SARS-CoV-2 Transmission by Inhalation Indoors. Saf Sci, 130:104866.https://doi.org/10.1016/j.ssci.2020.104866
12. Gralton J, Tovey E, McLaws ML, et al., 2011, The Role of Particle Size in Aerosolised Pathogen Transmission: A Review. J Infect, 62:1–13. https://doi.org/10.1016/j.jinf.2010.11.010
13. Wang CS, Otani Y, 2013, Removal of Nanoparticles from Gas Streams by Fibrous Filters: A Review. Ind Eng Chem Res, 52:5–17. https://doi.org/10.1021/ie300574m
14. Grinshpun SA, Yermakov M, Khodoun M, 2020, Autoclave Sterilization and Ethanol Treatment of Re-used Surgical Masks and N95 Respirators During COVID-19: Impact on Their Performance and Integrity. J Hosp Infect, 105:608–14. https://doi.org/10.1016/j.jhin.2020.06.030
15. Rengasamy S, Eimer BC, Shaffer RE, 2009, Comparison of Nanoparticle Filtration Performance of NIOSH-approved and CE-marked Particulate Filtering Facepiece Respirators. Ann Occup Hyg, 53:117–28. https://doi.org/10.1093/annhyg/men086
16. Grinshpun SA, Haruta H, Eninger RM, et al., 2009, Performance of an N95 Filtering Facepiece Particulate Respirator and a Surgical Mask During Human Breathing: Two Pathways for Particle Penetration. J Occup Environ Hyg, 6:593–603. https://doi.org/10.1080/15459620903120086
17. Cai M, Li H, Shen S, et al., 2018, Customized Design and 3D Printing of Face Seal for an N95 Filtering Facepiece Respirator. J Occup Environ Hyg, 15:226–34. https://doi.org/10.1080/15459624.2017.1411598
18. Swennen GR, Pottel L, Haers PE, 2020, Custom-made 3D-printed Face Masks in Case of Pandemic Crisis Situations with a Lack of Commercially Available FFP2/3 Masks. Int J Oral Maxillofac Surg, 49:673-7. https://doi.org/10.1016/j.ijom.2020.03.015
19. British Standards Institution, 2011, 149: 2001+ A1: 2009 Respiratory Protective Devices. Filtering Half Masks to Protect against Particles. Requirements, Testing, Marking. British Standards Institution, London, UK.
https://doi.org/10.3403/02279488
20. Gawn J, Clayton M, Makison C, et al., 2008, Evaluating the Protection Afforded by Surgical Masks Against Influenza Bioaerosols: Gross Protection of Surgical Masks Compared to Filtering Facepiece Respirators. Health Safety Exec,2020. Available from: https://www.hse.gov.uk/research/rrpdf/rr619. pdf. [Last accessed on 2020 Jan 01].
21. Lee SA, Hwang DC, Li HY, et al., 2016, Particle Size-selective Assessment of Protection of European Standard FFP Respirators and Surgical Masks Against Particles-tested with Human Subjects. J Healthc Eng, 2016:8572493. https://doi.org/10.1155/2016/8572493
22. Langford CR, Johnson DW, Cameron NR, 2015, Preparation of Hybrid Thiol-Acrylate Emulsion templated Porous Polymers by Interfacial Copolymerization of High Internal Phase Emulsions. Macromol Rapid Commun, 36:834–9. https://doi.org/10.1002/marc.201400733
23. Carnachan RJ, Bokhari M, Przyborski SA, et al., 2006, Tailoring the Morphology of Emulsion-templated Porous Polymers. Soft Matter, 2:608–16. https://doi.org/10.1039/b603211g
24. Althubeiti KM, Horozov TS, 2019, Efficient Preparation of Macroporous Poly (Methyl Methacrylate) Materials from High Internal Phase Emulsion Templates. React Function Polymers, 142:207–12. https://doi.org/10.1016/j.reactfunctpolym.2019.06.015
25. Moglia RS, Holm JL, Sears NA, et al., 2011, Injectable polyHIPEs as High-porosity Bone Grafts. Biomacromolecules, 12:3621–8. https://doi.org/10.1021/bm2008839
26. Paterson TE, Gigliobianco G, Sherborne C, et al., 2018, Porous Microspheres Support Mesenchymal Progenitor Cell Ingrowth and Stimulate Angiogenesis. APL Bioeng, 2:026103. https://doi.org/10.1063/1.5008556
27. Huš S, Krajnc P, 2014, PolyHIPEs from Methyl Methacrylate: Hierarchically Structured Microcellular Polymers with Exceptional Mechanical Properties. Polymer, 55:4420–24. https://doi.org/10.1016/j.polymer.2014.07.007
28. Bokhari M, Carnachan RJ, Przyborski SA, et al., 2007, Emulsion-templated Porous Polymers as Scaffolds for Three Dimensional Cell Culture: Effect of Synthesis Parameters on Scaffold Formation and Homogeneity. J Mater Chem, 17:4088–94. https://doi.org/10.1039/b707499a
29. Richez A, Deleuze H, Vedrenne P, et al., 2005, Preparation of Ultra-low-density Microcellular Materials. J Appl Polymer Sci, 96:2053–63. https://doi.org/10.1002/app.21668
30. Xu H, Zheng X, Huang Y, et al., 2016, Interconnected Porous Polymers with Tunable Pore Throat Size Prepared via Pickering High Internal Phase Emulsions. Langmuir, 32:38–45. https://doi.org/10.1021/acs.langmuir.5b03037
31. Williams JM, Gray AJ, Wilkerson MH, 1990, Emulsion Stability and Rigid Foams from Styrene or Divinylbenzene Water-in-oil Emulsions. Langmuir, 6:437–44. https://doi.org/10.1021/la00092a026
32. Cameron NR, Barbetta A, 2000, The Influence of Porogen Type on the Porosity, Surface Area and Morphology of Poly (Divinylbenzene) PolyHIPE Foams. J Mater Chem, 10:2466–71. https://doi.org/10.1039/b003596n
33. Barbetta A, Cameron NR, 2004, Morphology and Surface Area of Emulsion-Derived (PolyHIPE) Solid Foams Prepared with Oil-phase Soluble Porogenic Solvents: Span 80 as Surfactant. Macromolecules, 37:3188–201. https://doi.org/10.1021/ma0359436
34. Williams JM, Wrobleski DA, 1988, Spatial Distribution of the Phases in Water-in-oil Emulsions. Open and Closed Microcellular Foams from Cross-linked Polystyrene. Langmuir, 4:656–62. https://doi.org/10.1021/la00081a027
35. Gurevitch I, Silverstein MS, 2010, Polymerized Pickering HIPEs: Effects of Synthesis Parameters on Porous Structure. J Polymer Sci Part A, 48:1516–25. https://doi.org/10.1002/pola.23911
36. Robinson JL, Moglia RS, Stuebben MC, et al., 2014, Achieving Interconnected Pore Architecture in Injectable polyHIPEs for Bone Tissue Engineering. Tissue Eng Part A, 20:1103–12. https://doi.org/10.1089/ten.tea.2013.0319
37. Cameron NR, Sherrington DC, Albiston L, et al., 1996, Study of the Formation of the Open-cellular Morphology of Poly (Styrene/Divinylbenzene) polyHIPE Materials by Cryo- SEM. Coll Polymer Sci, 274:592–5. https://doi.org/10.1007/bf00655236
38. Lissant KJ, 1966, The Geometry of High-internal-phase-ratio Emulsions. J Coll Int Sci, 22:462–8. https://doi.org/10.1016/0021-9797(66)90091-9
39. Owen R, Sherborne C, Paterson T, et al., 2016, Emulsion Templated Scaffolds with Tunable Mechanical Properties for Bone Tissue Engineering. J Mech Behav Biomed Mater, 54:159–72. https://doi.org/10.1016/j.jmbbm.2015.09.019
40. San Manley S, Graeber N, Grof Z, et al., 2009, New Insights into the Relationship Between Internal Phase Level of Emulsion Templates and Gas-liquid Permeability of Interconnected Macroporous Polymers. Soft Matter, 5:4780–7. https://doi.org/10.1039/b900426b
41. Tadros TF, 2013, Emulsion Formation, Stability, and Rheology. Emulsion Formation Stabil, 1:1–75.
https://doi.org/10.1002/9783527647941.ch1
42. Brun N, Ungureanu S, Deleuze H, et al., 2011, Hybrid Foams, Colloids and Beyond: From Design to Applications. Chem Soc Rev, 40:771–88. https://doi.org/10.1039/b920518g
43. Cameron NR, 2005, High Internal Phase Emulsion Templating as a Route to Well-defined Porous Polymers. Polymer, 46:1439–49. https://doi.org/10.1016/j.polymer.2004.11.097
44. Cameron NR, Sherrington DC, 1996, High Internal Phase Emulsions (HIPEs)-structure, Properties and Use in Polymer Preparation. Biopolymers Liquid Crystalline Polymers Phase Emulsion, 126:163–214. https://doi.org/10.1007/3-540-60484-7_4
45. Kimmins SD, Cameron NR, 2011, Functional Porous Polymers by Emulsion Templating: Recent Advances. Adv Function Mater, 21:211–25. https://doi.org/10.1002/adfm.201001330
46. Pulko I, Krajnc P, 2012, High Internal Phase Emulsion Templating-a Path to Hierarchically Porous Functional Polymers. Macromol Rapid Commun, 33:1731–46. https://doi.org/10.1002/marc.201200393
47. Tebboth M, Menner A, Kogelbauer A, et al., 2014, Polymerised high internal phase emulsions for fluid separation applications. Curr Opin Chem Eng, 4:114–20. https://doi.org/10.1016/j.coche.2014.03.001
48. Silverstein MS, 2014, PolyHIPEs: Recent Advances in Emulsion-templated Porous Polymers. Prog Polym Sci, 39:199–234. https://doi.org/10.1016/j.progpolymsci.2013.07.003
49. Zhang T, Sanguramath RA, Israel S, et al., 2019, Emulsion Templating: Porous Polymers and Beyond. Macromolecules, 52:5445–79. https://doi.org/10.1021/acs.macromol.8b02576
50. Silverstein MS, 2014, Emulsion-templated Porous Polymers: A Retrospective Perspective. Polymer, 55:304–20. https://doi.org/10.1016/j.polymer.2013.08.068
51. Silverstein MS, 2020, The Chemistry of Porous Polymers: The Holey Grail. Israel J Chem, 60:140–50.
52. Andrieux S, Quell A, Stubenrauch C, et al., 2018, Liquid Foam Templating-a Route to Tailor-made Polymer Foams. Adv Coll Int Sci, 256:276–90. https://doi.org/10.1016/j.cis.2018.03.010
53. Moon S, Kim JQ, Kim BQ, et al., 2020, Processable Composites with Extreme Material Capacities: Toward Designer High Internal Phase Emulsions and Foams. Chem Mater, 32:4838–54. https://doi.org/10.1021/acs.chemmater.9b04952
54. Dikici BA, Claeyssens F, 2020, Basic Principles of Emulsion Templating and Its Use as an Emerging Manufacturing Method of Tissue Engineering Scaffolds. Front Bioeng Biotechnol, 8:875.
https://doi.org/10.3389/fbioe.2020.00875
55. Taylor-Pashow KM, Pribyl JG, 2019, PolyHIPEs for Separations and Chemical Transformations: A Review. Solvent Extract Ion Exchan, 37:1–26. https://doi.org/10.1080/07366299.2019.1592924
56. Choudhury S, Connolly D, White B, 2015, Supermacroporous polyHIPE and Cryogel Monolithic Materials as Stationary Phases in Separation Science: A Review. Anal Methods, 7:6967–82. https://doi.org/10.1039/c5ay01193k
57. Gu H, Liu Y, Yin D, et al., 2018, Heparin-immobilized Polymeric Monolithic Column with Submicron Skeletons and Well-defined Macropores for Highly Efficient Purification of Enterovirus 71. Macromol Mater Eng, 303:1800411. https://doi.org/10.1002/mame.201800411
58. Muralikrishnan R, Swarnalakshmi M, Nakkeeran E, 2014, Nanoparticle-membrane Filtration of Vehicular Exhaust to Reduce air Pollution-a Review. Int Res J Environ Sci, 3:82–6.
59. Xing YF, Xu YH, Shi MH, et al., 2016, The Impact of PM2. 5 on the Human Respiratory System. J Thorac Dis, 8:E69.
60. ISO, 2015, ISO/TS 80004-2: 2015. Nanotechnologies- Vocabulary-Part 2: Nano-objects. ISO, United Kingdom.
61. Ramachandran S, Rajiv S, 2020, Emulsion Templated Amino Functionalised Polymeric Monolith Filter for Innovative Air Purification Technology. J Porous Mater, 27:939–46. https://doi.org/10.1007/s10934-019-00856-1
62. Walsh DC, Stenhouse JI, Kingsbury LP, et al., 1996, PolyHIPE Foams: Production, Characterisation, and Performance as Aerosol Filtration Materials. J Aerosol Sci, 27:S629–30. https://doi.org/10.1016/0021-8502(96)00387-4
63. Hung CH, Leung WW, 2011, Filtration of Nano-aerosol Using Nanofiber Filter Under Low Peclet Number and Transitional Flow Regime. Separat Purificat Technol, 79:34–42. https://doi.org/10.1016/j.seppur.2011.03.008
64. Krajnc P, Leber N, Štefanec D, et al., 2005, Preparation and Characterisation of Poly (High Internal Phase Emulsion) Methacrylate Monoliths and Their Application as Separation Media. J Chromatogr A, 1065:69–73.
https://doi.org/10.1016/j.chroma.2004.10.051
65. Pulko I, Smrekar V, Podgornik A, et al., 2011, Emulsion Templated Open Porous Membranes for Protein Purification. J Chromatogr A, 1218:2396–401. https://doi.org/10.1016/j.chroma.2010.11.069
66. Yao C, Qi L, Yang G, et al., 2010, Preparation of Sub-micron Skeletal Monoliths with High Capacity for Liquid Chromatography. J Separat Sci, 33:475–83. https://doi.org/10.1002/jssc.200900655
67. Dinh NP, Cam QM, Nguyen AM, et al., 2009, Functionalization of Epoxy-based Monoliths for Ion Exchange Chromatography of Proteins. J Separat Sci, 32:2556–64.
https://doi.org/10.1002/jssc.200900243
68. Zhang T, Guo Q, 2017, Continuous Preparation of polyHIPE Monoliths from Ionomer-stabilized High Internal Phase Emulsions (HIPEs) for Efficient Recovery of Spilled Oils. Chem Eng J, 307:812–9.
https://doi.org/10.1016/j.cej.2016.09.024
69. Zhang N, Zhong S, Zhou X, et al., 2016, Superhydrophobic P (St-DVB) Foam Prepared by the High Internal Phase Emulsion Technique for Oil Spill Recovery. Chem Eng J, 298:117–24. https://doi.org/10.1016/j.cej.2016.03.151
70. Balow RB, Giles SL, McGann CL, et al., 2018, Rapid Decontamination of Chemical Warfare Agent Simulant with Thermally Activated Porous Polymer Foams. Ind Eng Chem Res, 57:8630–4.
https://doi.org/10.1021/acs.iecr.8b01546
71.McGann CL, Daniels GC, Giles SL, et al., 2018, Air Activated Self-Decontaminating Polydicyclopentadiene PolyHIPE Foams for Rapid Decontamination of Chemical Warfare Agents. Macromol Rapid Commun, 39:1800194. https://doi.org/10.1002/marc.201800194
72. Hughes JM, Budd PM, Tiede K, et al., 2015, Polymerized High Internal Phase Emulsion Monoliths for the Chromatographic Separation of Engineered Nanoparticles. J Appl Polymer Sci, 132:41229. https://doi.org/10.1002/app.41229
73. Bhumgara Z, 1995, Polyhipe Foam Materials as Filtration Media. Filtrat Separat, 32:245–51. https://doi.org/10.1016/s0015-1882(97)84048-7
74. Malakian A, Zhou M, Zowada RT, et al., 2019, Synthesis and in Situ Functionalization of Microfiltration Membranes Via High Internal Phase Emulsion Templating. Polymer Int, 68:1378–86. https://doi.org/10.1002/pi.5828
75. Katsoyiannis IA, Zouboulis AI, 2002, Removal of Arsenic from Contaminated Water Sources by Sorption Onto Iron-oxide-coated Polymeric Materials. Water Res, 36:5141–55. https://doi.org/10.1016/s0043-1354(02)00236-1
76. Zhu Y, Wang W, Yu H, et al., 2020. Preparation of Porous Adsorbent Via Pickering Emulsion Template for Water Treatment: A Review. J Environ Sci, 88:217–36. https://doi.org/10.1016/j.jes.2019.09.001
77. Zhao C, Danish E, Cameron NR, et al., 2007, Emulsion-templated Porous Materials (PolyHIPEs) for Selective Ion and Molecular Recognition and Transport: Applications in Electrochemical Sensing. J Mater Chem, 17:2446–53. https://doi.org/10.1039/b700929a
78. Pulko I, Krajnc P, 2008, Open Cellular Reactive Porous Membranes from High Internal Phase Emulsions. Chem Commun, 37:4481–3. https://doi.org/10.1039/b807095d
79. Sevšek U, Seifried S, Stropnik Č, et al., 2011, Poly (styrene-co-divinylbenzene-co-2-ethylhexyl) Acrilate Membranes with Interconnected Macroporous Structure. Mater Tehnol, 45:247–51.
80. Kovačič S, Preishuber-Pflügl F, Slugovc C, 2014, Macroporous Polyolefin Membranes from Dicyclopentadiene High Internal Phase Emulsions: Preparation and Morphology Tuning. Macromol Mater Eng, 299:843–50. https://doi.org/10.1002/mame.201300400
81. Owen R, Sherborne C, Evans R, et al., 2020, Combined Porogen Leaching and Emulsion Templating to Produce Bone Tissue Engineering Scaffolds. Int J Bioprint, 6:99–113. https://doi.org/10.18063/ijb.v6i2.265
82. Huang X, Yang Y, Shi J, et al., 2015, High-internal-phase Emulsion Tailoring Polymer Amphiphilicity towards an Efficient NIR-sensitive Bacteria Filter. Small, 11:4876–83. https://doi.org/10.1002/smll.201501396
83. Yang Q, Li H, Shen S, et al., 2018, Study of the Micro-climate and Bacterial Distribution in the Deadspace of N95 Filtering Face Respirators. Sci Rep, 8:1–13. https://doi.org/10.1038/s41598-018-35693-w
84. Wang X, Chen X, Peng Y, et al., 2019, Silver-modified Porous Polystyrene Sulfonate Derived from Pickering High Internal Phase Emulsions for Capturing Lithium-ion. RSC Adv, 9:7228–37. https://doi.org/10.1039/c8ra09740b
85. Sadeghi S, Moghbeli MR, 2012, Synthesis and Dispersion of Colloidal Silver Nanoparticles on Microcellular Polyhipe Support. Coll Surf A, 409:42–51. https://doi.org/10.1016/j.colsurfa.2012.05.037
86. Lundin JG, McGann CL, Weise NK, et al., 2019, Iodine Binding and Release from Antimicrobial Hemostatic Polymer Foams. React Function Polymers, 135:44–51. https://doi.org/10.1016/j.reactfunctpolym.2018.12.009
87. Streifel BC, Lundin JG, Sanders AM, et al., 2018, Hemostatic and Absorbent PolyHIPE-Kaolin Composites for 3D Printable Wound Dressing Materials. Macromol Biosci, 18:1700414. https://doi.org/10.1002/mabi.201700414
88. McDonnell G, Russell AD, 1999, Antiseptics and Disinfectants: Activity, Action, and Resistance. Clin Microbiol Rev, 12:147–79. https://doi.org/10.1128/cmr.12.1.147
89. McGann CL, Streifel BC, Lundin JG, et al., 2017, Multifunctional polyHIPE Wound Dressings for the Treatment of Severe Limb Trauma. Polymer, 126:408–18. https://doi.org/10.1016/j.polymer.2017.05.067
90. Dikici BA, Dikici S, Reilly GC, et al., 2019, A Novel Bilayer Polycaprolactone Membrane for Guided Bone Regeneration: Combining Electrospinning and Emulsion Templating. Materials, 12:2643. https://doi.org/10.3390/ma12162643
91. Gui H, Zhang T, Ji S, et al., 2020, Nanofibrous, Porous Monoliths Formed from Gelating High Internal Phase Emulsions Using Syndiotactic Polystyrene. Polymer, 2020:122708. https://doi.org/10.1016/j.polymer.2020.122708
92. Johnson DW, Sherborne C, Didsbury MP, et al., 2013, Macrostructuring of Emulsion-templated Porous Polymers by 3D Laser Patterning. Adv Mater, 25:3178–81. https://doi.org/10.1002/adma.201300552
93. Sears NA, Dhavalikar PS, Cosgriff-Hernandez EM, 2016, Emulsion Inks for 3D Printing of High Porosity Materials. Macromol Rapid Commun, 37:1369–74. https://doi.org/10.1002/marc.201600236
94. Sears N, Dhavalikar P, Whitely M, et al., 2017, Fabrication of Biomimetic Bone Grafts with Multi-material 3D Printing. Biofabrication, 9:025020. https://doi.org/10.1088/1758-5090/aa7077
95. Welch CF, Rose GD, Malotky D, et al., 2006, Rheology of High Internal Phase Emulsions. Langmuir, 22:1544–50. https://doi.org/10.1021/la052207h
96. Stansbury JW, Idacavage MJ, 2016, 3D Printing with Polymers: Challenges Among Expanding Options and Opportunities. Dent Mater, 32:54–64. https://doi.org/10.1016/j.dental.2015.09.018
97. Malayeri A, Sherborne C, Paterson T, et al., 2016, Osteosarcoma Growth on Trabecular Bone Mimicking Structures Manufactured Via Laser Direct Write. Int J Bioprint, 2:67–77. https://doi.org/10.18063/ijb.2016.02.005
98. Wang AJ, Paterson T, Owen R, et al., 2016, Photocurable High Internal Phase Emulsions (HIPEs) Containing Hydroxyapatite for Additive Manufacture of Tissue Engineering Scaffolds with Multi-scale Porosity. Mater Sci Eng C, 67:51–8. https://doi.org/10.1016/j.msec.2016.04.087
99. Sherborne C, Owen R, Reilly GC, et al., 2018, Light-based Additive Manufacturing of PolyHIPEs: Controlling the Surface Porosity for 3D Cell Culture Applications. Mater Design, 156:494–503.
https://doi.org/10.1016/j.matdes.2018.06.061
100. Huan S, Mattos BD, Ajdary R, et al., 2019, Two-phase Emulgels for Direct Ink Writing of Skin-Bearing Architectures. Adv Function Mater, 29:1902990.
https://doi.org/10.1002/adfm.201902990
101. Sušec M, Ligon SC, Stampfl J, et al., 2013, Hierarchically Porous Materials from Layer-by-layer Photopolymerization of High Internal Phase Emulsions. Macromol Rapid Commun, 34:938–43.
https://doi.org/10.1002/marc.201300016
102. Rezanavaz R, 2018, 3D Printing of Porous Polymeric Materials for Stationary Phases of Chromatography Columns. UC Library, California.
103. Cooperstein I, Layani M, Magdassi S, 2015, 3D Printing of Porous Structures by UV-Curable O/W Emulsion for Fabrication of Conductive Objects. J Mater Chem C, 3:2040–4. https://doi.org/10.1039/c4tc02215g
104. Wenger L, Radtke CP, Göpper J, et al., 2020, 3D-printable and Enzymatically Active Composite Materials Based on Hydrogel-filled High Internal Phase Emulsions. Front Bioeng Biotechnol, 8:713.
https://doi.org/10.3389/fbioe.2020.00713
105. Sears NA, Wilems TS, Gold KA, et al., 2019, Hydrocolloid Inks for 3D Printing of Porous Hydrogels. Adv Mater Technol, 4:1800343. https://doi.org/10.1002/admt.201800343
106. Minas C, Carnelli D, Tervoort E, et al., 2016, 3D Printing of Emulsions and Foams into Hierarchical Porous Ceramics. Adv Mater, 28:9993–9. https://doi.org/10.1002/adma.201603390
107. Alison L, Menasce S, Bouville F, et al., 2019, 3D Printing of Sacrificial Templates into Hierarchical Porous Materials. Sci Rep, 9:1–9. https://doi.org/10.1038/s41598-018-36789-z
108. Jiang H, Sheng Y, Ngai T, 2020, Pickering Emulsions: Versatility of Colloidal Particles and Recent Applications. Curr Opin Coll Int Sci, 49:1–15. https://doi.org/10.1016/j.cocis.2020.04.010
109. Liu J, Wang P, He Y, et al., 2019, Polymerizable Nonconventional Gel Emulsions and Their Utilization in the Template Preparation of Low-density, High-strength Polymeric Monoliths and 3D Printing. Macromolecules, 52:2456–63. https://doi.org/10.1021/acs.macromol.8b02610
110. Sihler S, Schrade A, Cao Z, et al., 2015, Inverse Pickering Emulsions with Droplet Sizes Below 500 nm. Langmuir, 31:10392–401. https://doi.org/10.1021/acs.langmuir.5b02735
111. Zhu W, Zhu Y, Zhou C, et al., 2019, Pickering Emulsion-templated Polymers: Insights into the Relationship Between Surfactant and Interconnecting Pores. RSC Adv, 9:18909–16. https://doi.org/10.1039/c9ra03186c
112. Sommer MR, Alison L, Minas C, et al., 2017, 3D Printing of Concentrated Emulsions into Multiphase Biocompatible Soft Materials. Soft Matter, 13:1794–803. https://doi.org/10.1039/c6sm02682f
113. Tu R, Sprague E, Sodano HA, 2020, Precipitation Printing Towards Diverse Materials, Mechanical Tailoring and Functional Devices. Addit Manuf, 2020:101358. https://doi.org/10.1016/j.addma.2020.101358
114. Karyappa R, Ohno A, Hashimoto M, 2019, Immersion Precipitation 3D Printing (ip 3DP). Mater Horiz, 6:1834–44. https://doi.org/10.1039/c9mh00730j
115. Yang T, Hu Y, Wang C, et al., 2017, Fabrication of Hierarchical Macroporous Biocompatible Scaffolds by Combining Pickering High Internal Phase Emulsion Templates with Three-dimensional Printing. ACS Appl Mater Int, 9:22950–8. https://doi.org/10.1021/acsami.7b05012.s001
116. Hu Y, Wang J, Li X, et al., 2019, Facile Preparation of Bioactive Nanoparticle/Poly (ε-caprolactone) Hierarchical Porous Scaffolds Via 3D Printing of High Internal Phase Pickering Emulsions. J Coll Int Sci, 545:104–15. https://doi.org/10.1016/j.jcis.2019.03.024
117. Visser CW, Amato DN, Mueller J, et al., 2019, Architected Polymer Foams via Direct Bubble Writing. Adv. Mater, 31:1904668. https://doi.org/10.1002/adma.201904668
118. Voisin HP, Gordeyeva K, Siqueira G, et al., 2018, 3D Printing of Strong Lightweight Cellular Structures Using Polysaccharide-based Composite Foams. ACS Sustain Chem Eng, 6:17160–7. https://doi.org/10.1021/acssuschemeng.8b04549
119. Wirth DM, Jaquez A, Gandarilla S, et al., 2020, Highly Expandable Foam for Lithographic 3D Printing. ACS Appl Mater Int, 12:19033–43. https://doi.org/10.1021/acsami.0c02683
120. Mu X, Bertron T, Dunn C, et al., 2017, Porous Polymeric Materials by 3D Printing of Photocurable Resin. Mater Horiz, 4:442–9. https://doi.org/10.1039/c7mh00084g
121. Sommer MR, Schaffner M, Carnelli D, et al., 2016, 3D Printing of Hierarchical Silk Fibroin Structures. ACS Appl Mater Int, 8:34677–85. https://doi.org/10.1021/acsami.6b11440
122. Giglia S, Bohonak D, Greenhalgh P, et al., 2015. Measurement of Pore Size Distribution and Prediction of Membrane Filter Virus Retention Using Liquid-liquid Porometry. J Memb Sci, 476:399–409. https://doi.org/10.1016/j.memsci.2014.11.053
123. Schultz S, Wagner G, Urban K, et al., 2004, High-pressure Homogenization as a Process for Emulsion Formation. Chem Eng Technol, 27:361–8. https://doi.org/10.1002/ceat.200406111
124. Vladisavljević GT, 2016, Recent Advances in the Production of Controllable Multiple Emulsions Using Microfabricated Devices. Particuology, 24:1–17. https://doi.org/10.1016/j.partic.2015.10.001
125. Costantini M, Colosi C, Guzowski J, et al., 2014, Highly Ordered and Tunable Polyhipes by Using Microfluidics. J Mater Chem B, 2:2290–300. https://doi.org/10.1039/c3tb21227k
126. Quell A, Elsing J, Drenckhan W, et al., 2015, Monodisperse Polystyrene Foams Via Microfluidics-a Novel Templating Route. Adv Eng Mater, 17:604–9. https://doi.org/10.1002/adem.201500040
127. Quell A, de Bergolis B, Drenckhan W, et al., 2016, How the Locus of Initiation Influences the Morphology and the Pore Connectivity of a Monodisperse Polymer Foam. Macromolecules, 49:5059–67.
https://doi.org/10.1021/acs.macromol.6b00494
128. Elsing J, Stefanov T, Gilchrist MD, et al., 2017, Monodisperse Polystyrene Foams Via Polymerization of Foamed Emulsions: Structure and Mechanical Properties. Phys Chem Chem Phys, 19:5477–5485.
https://doi.org/10.1039/c6cp06612g
129. Costantini M, Jaroszewicz J, Kozoń Ł, et al., 2019, 3D-printing of Functionally Graded Porous Materials Using On-demand Reconfigurable Microfluidics. Ange Chem Int Ed, 58:7620–7625.
https://doi.org/10.1002/anie.201900530
130. Abate AR, Romanowsky MB, Agresti JJ, et al., 2009, Valve-based Flow Focusing for Drop Formation. Appl Phys Lett, 94:023503. https://doi.org/10.1063/1.3067862
131. Stubenrauch C, Menner A, Bismarck A, et al., 2018, Emulsion and Foam Templating-promising Routes to Tailor-made Porous Polymers. Ange Chem Int Ed, 57:10024-10032. https://doi.org/10.1002/anie.201801466
132. Nisisako T, Torii T, 2008, Microfluidic Large-scale Integration on a Chip for Mass Production of Monodisperse Droplets and Particles. Lab Chip, 8:287–293. https://doi.org/10.1039/b713141k
133. Nisisako T, Ando T, Hatsuzawa T, 2012, High-volume Production of Single and Compound Emulsions in a Microfluidic Parallelization Arrangement Coupled with Coaxial Annular World-to-chip Interfaces. Lab Chip, 12:3426–3435. https://doi.org/10.1039/c2lc40245a
134. Carballido L, Dabrowski ML, Dehli F, et al., 2020, Monodisperse Liquid Foams Via Membrane Foaming. J Coll Int Sci, 568:46–53. https://doi.org/10.1016/j.jcis.2020.02.036
135. Vladisavljević GT, 2019, Preparation of Microemulsions and Nanoemulsions by Membrane Emulsification. Coll Surf A, 2019:123709. https://doi.org/10.1016/j.colsurfa.2019.123709
136. Wang B, Prinsen P, Wang H, et al., 2017, Macroporous Materials: Microfluidic Fabrication, Functionalization and Applications. Chem Soc Rev, 46:855–914. https://doi.org/10.1039/c5cs00065c