Abstract
Multistable mechanical metamaterials are a type of mechanical metamaterials with special features, such as reusability, energy storage and absorption capabilities, rapid deformation, and amplified output forces. These metamaterials are usually realized by series and/or parallel of bistable units. They can exhibit multiple stable configurations under external loads and can be switched reversely among each other, thereby realizing the reusability of mechanical metamaterials and offering broad engineering applications. This paper reviews the latest research progress in the design strategy, manufacture and application of multistable mechanical metamaterials. We divide bistable structures into three categories based on their basic element types and provide the criterion of their bistability. Various manufacturing techniques to fabricate these multistable mechanical metamaterials are introduced, including mold casting, cutting, folding and three-dimensional/4D printing. Furthermore, the prospects of multistable mechanical metamaterials for applications in soft driving, mechanical computing, energy absorption and wave controlling are discussed. Finally, this paper highlights possible challenges and opportunities for future investigations. The review aims to provide insights into the research and development of multistable mechanical metamaterials.
Highlights
The design principle and advantages of multistable mechanical metamaterials were introduced.
The most advanced manufacture techniques of multistable mechanical metamaterials were reviewed.
Multistable mechanical metamaterials have attractive applications, such as wave control, soft actuator and energy absorption.
Perspectives and challenges on multistable mechanical metamaterials were provided.
Export citation and abstract BibTeX RIS

Original content from this work may be used under the terms of the Creative Commons Attribution 4.0 license. Any further distribution of this work must maintain attribution to the author(s) and the title of the work, journal citation and DOI.
1. Introduction
Metamaterials are artificial microstructural materials with extraordinary mechanical [1–3], thermal [4–6], acoustic [7–9] and optical [10, 11] properties over conventional materials [12]. These properties are dependent on the special designed microstructures rather than the base materials [10, 13]. Among them, mechanical metamaterials are a class of artificial materials that exhibit exotic mechanical properties, such as negative thermal expansion [2, 14], negative Poisson's ratio auxetic behavior [15, 16], multistability [17, 18], tunable stiffness [19], etc.
Multistable mechanical metamaterials are a type of mechanical metamaterials which can exhibit multiple steady-state configurations under external loads and can be switched reversely [20, 21]. They are usually obtained by series and/or parallel connections of bistable structures with two stable configurations. The bistable structure crosses the energy barrier and quickly switches from the initial steady state to the second steady state when the external load exceeds the critical load of the steady-state transition, and the deformation state can be maintained without continuous energy input. The energy barrier is determined by the geometric size, structural form and material properties of the bistable structure. Therefore, the power output and the snap-through threshold can be tuned by adjusting the parameter values [18, 21, 22]. Bistable structures are common in nature and in daily life, such as Venus flytrap leaves ('Open and Closed'), hummingbird beak (rapidly closing in a few milliseconds to eat insects), switches, bottle caps, pen caps, plastic buckles, nylon cable ties, bouncing toy balls, tape measures, hair clips, and so on [23]. Based on the basic element types, natural and engineered bistable structures can be broadly classified into three categories, as shown in figure 1: (1) beams, trusses, and compliant mechanisms; (2) curved surfaces and thin-shell structures; and (3) other structures such as kirigami and snap-fit structures.
Figure 1. Classification of bistable unit structures and preparation and potential applications of multistable mechanical metamaterials. The three innermost leaves contain three basic bistable units. The intermediate ring describes the basic preparation methods of multistable metamaterials: 3D printing (DIW, FDM, SLA, PolyJet, PBF, PμSL, and TPP), cutting (mechanical cutting and laser cutting) and mold casting. The outermost ring describes the potential applications of multistable mechanical metamaterials: energy absorption. [18] John Wiley & Sons. © 2015 WILEY‐VCH Verlag GmbH & Co. KGaA, Weinheim. [21] John Wiley & Sons. © 2021 Wiley‐VCH GmbH. Reproduced from [25]. CC BY 4.0. From [44]. Reprinted with permission from AAAS. From [20]. Reprinted with permission from AAAS. Reproduced from [34], with permission from Springer Nature. Reproduced from [40]. CC BY 4.0. Reproduced with permission from [41].
Download figure:
Standard image High-resolution imageIn the past decade, bistable/multistable structures have garnered significant attention due to their excellent properties:
- (a)Bistable structures can maintain their deformed shape and can be restored to their initial state with the application of an opposite force, improving device utilization [24].
- (b)
- (c)
- (d)
- (e)
To realize these advantages, various methods are used to fabricate the multistable mechanical metamaterials, including laser cutting, mold casting, three-dimensional (3D)/4D printing, etc. The advancement of additive manufacturing (AM) (i.e. 3D printing) technology has allowed the fabrication of complex multistable mechanical metamaterials [28, 29], which is beyond the capability of traditional subtractive manufacturing methods. These 3D printing methods include macroscopic manufacturing technology and mesoscopic/microscopic manufacturing technology. With the support of these advanced manufacturing technologies, different types of multistable mechanical metamaterials have been prepared and have shown great application prospects in soft actuator/robot [30–33], mechanical storage/logical operation [26, 34–37], energy absorption [18, 21, 24, 38, 39], and wave control [40, 41].
The development of multistable mechanical metamaterials involves lots of interdisciplinary, from mechanical design to manufacturing and materials science. At present, most of current reviews on bistable/multistable structures and multistable mechanical metamaterials are limited to their design strategies or applications, such as multistable actuators for soft robots or bistable structures for advanced functional systems [23, 42, 43]. A systematic and integrated review of multistable mechanical metamaterials, which involves classification of bistable units, mechanical properties, manufacturing and application prospects of multistable mechanical metamaterials is absent. With this motivation, the current paper reviews the recent progress in the design, manufacture and application of multistable mechanical metamaterials in the past decade. Firstly, we introduce the characteristics and design principles of bistable units. Subsequently, we summarize the most advanced manufacturing technology of multistable mechanical metamaterials, including 3D/4D printing, cutting and mold casting. Then, we discuss the application prospects of multistable mechanical metamaterials, such as soft actuators/robots, mechanical logic/storage, energy absorption, wave control, etc. Finally, we conclude the article and provide predictions and outlooks for future challenges and opportunities. Ultimately, we hope that this review can provide insights into the research and development of multistable mechanical metamaterials.
2. Design principles of bistable units
2.1. Mechanical properties of bistable structures
Bistability is the most basic structural form in the multistable structure. A snap-through effect, wherein the first steady state of bistability quickly transitions to the second steady state upon the application of a load F exceeding the threshold Fcr, is commonly observed in bistable structures [23]. Most bistable units exhibit three different nonlinear mechanical responses by adjusting the geometric parameters, i.e. bistability, monostability and simple stability [23]. Additionally, bistable structures can maintain their state after unloading without requiring a continuous supply of energy. The second steady state can transform back to the first steady state when the reverse force is applied. The structure exhibits a nonlinear force–displacement curve during the steady state conversion, as shown in the blue solid line in figure 2(a). Notably, the bistable structure exhibits negative force during snap-through, which signifies a transition from initial positive stiffness to negative stiffness during deformation, and an eventual return to positive stiffness upon completion of steady-state conversion [45, 46].
Figure 2. Bistable and monostable (a) force–displacement and (b) energy landscapes. The analogy of 'ball on the hill' illustrates stable and unstable equilibrium: (c) bistable and (d) stable under external force constraints.
Download figure:
Standard image High-resolution imageMonostability indicates that a structure has a single stable configuration when it undergoes deformation [23, 47]. The structure yields and deforms via a snap-through phenomenon when the applied load exceeds a particular threshold. However, once the load is removed, the structure can no longer sustain its deformed shape and require external support to maintain it; this is demonstrated in figure 2(a) by the yellow dotted line. Conversely, a simple steady state exhibits nonlinear elastic deformation under an applied load without any signs of snap-through instability [23]. The stable structure returns to the initial steady state after unloading, and the force–displacement curve shows no negative stiffness.
The energy landscape of the bistable structure during the steady-state conversion process is shown in figure 2(b). It can be seen that the structure will experience one local maximum Umax (unstable point) and two local minimums U1 and U2 (stable point) during this conversion process. Therefore, the structure absorbs energy and then releases energy during the steady state transition. In contrast, the monostable structure represented by the yellow dotted line in figure 2(b) has only one local minimum [22, 23]. The energy barrier ΔU, which determines the transition between the two steady states, is measured by controlling the displacement and equals the difference between the maximum and minimum energy values [23]. ΔU1 = Umax − U1 represents the transition from stable state 1 to stable state 2, while ΔU2 = Umax − U2 represents the transition from stable state 2 to state 1 (figure 2(b)). The load applied on the bistable structure has to overcome the energy barrier for the snap-through.
The energy landscape can be visualized as a 'ball on the hill' [48, 49], as shown in figure 2(c). Points A and C represent stable points corresponding to the local minimums in the energy landscape. The ball will return to its original position at either A or C under small perturbations, signifying a stable equilibrium state. Point B is an unstable point, where the potential energy is high, corresponding to the local maximum point in the energy landscape. Once disturbed from point B, the system will move toward the lower energy states at point A or C without returning to point B, indicating an unstable equilibrium state. Point D represents an infinite number of possible equilibrium states, known as the random equilibrium state with a high degree of uncertainty. Point E is also stable, but only under external constraints, as shown in figure 2(d).
In comparison to stable and monostable structures, bistable structures have the following excellent characteristics. Firstly, bistable structures possess a reusable property that allows them to switch between two steady states reversibly [21, 24, 50]. Secondly, they experience rapid deformation during snap-through, allowing for amplified output force even with low driving energy [22]. Thirdly, bistable structures exhibit energy storage and absorption properties, which can prevent secondary impact caused by rebound [18, 21, 51]. Fourthly, bistable structures are characterized as having low energy consumption since they maintain their deformed shape without requiring additional energy [23, 52]. Finally, multiple bistable units can be connected in series and/or in parallel to construct multistable structures with different stable configurations that exhibit rich deformation capability and reconfigurability under external drive [23, 42].
2.2. Classification of bistable units design principles
There are many bistable structures in nature [23], such as Venus's flytrap leaves ('Open and Closed'), hummingbird beak (rapidly closing in a few milliseconds to eat insects). Similarly, bistable structures are ubiquitous in daily life, including switches, bottle caps, pen caps, plastic buckles, nylon cable ties, bouncing toy balls, tape measures, hair clips, and so on. We classify these natural and engineering bistable structures into three categories according to the element type. The first category is bistable structures with rods with 1D characteristics as the basic element type, such as beams, trusses, compliant mechanisms. The second category is bistable structures with shell structures with 2D characteristics as the basic element type, such as curved surfaces and thin shell structures. In addition, there are some other bistable units, which are divided into the third category, such as snap-fit structure, biholar sheet structure, rotating hinge deployable kirigami structure, and square-twist origami structure, etc.
2.2.1. Beams, trusses and compliant mechanisms.
Bars are the fundamental elements studied in mechanical engineering. Among these, beams, trusses, and flexible mechanisms are the simplest units in bistable structures, featuring four common forms, as shown in figure 3(a). The beam and truss structures are easy to design, and the structures are simpler and easier to prepare.
Figure 3. Common bistable units. (a) Bistable beams, truss units and compliant mechanisms: (i) Von Mises truss; (ii) constrained curved beams; (iii) inclined straight beam; (iv) rigid connection compliant mechanism with spring. (b) Bistable thin shell unit: (i) dome shell; (ii) single curved surface and double curved surface; (iii) '<'-shaped straw shell; (iv) Miura-ori and waterbomb origami; (v) Kresling origami. (c) Other bistable units: (i) snap-fit structure; (ii) biholar sheet structure; (iii) rotary hinge deployable kirigami structure; (iv) square-twist origami structure.
Download figure:
Standard image High-resolution image
(1) The Von Mises truss [53] consists of two connecting trusses or two ends fixed on a support rod with a hinged connection in the center (figure 3(a-i)). Its bistability relies primarily on hinge deformation, which may produce snap-through instability with small displacements [23]. Von Mises trusses are inherently bistable structures with α values ranging from 0° to 90°. Snap-through instability will occur when the deformation inclination angle θ exceeds the threshold angle . Based on these characteristics, Von Mises truss structures are often used in soft robotics, wave control and mechanical logic operations.
(2) The constrained curved beam [51, 54], namely the pre-buckling double-clamped curved beam under horizontal force (figure 3(a-ii)). The constrained curved beam structure can achieve monostability and bistability by adjusting the geometric structure parameters. The mechanical response of the beam can be altered by the ratio Q= H/h, where H and h represent the height and thickness of the beam, respectively [54–57]. If Q > Qcr = 2.31, it exhibits bistability. Due to the simplicity and ease of preparation of the structure, constrained curved beams are used in a wide range of applications, such as energy absorption, microelectromechanical systems, actuators/soft robotics, mechanical computing, etc.
(3) The inclined straight beam [18, 58], which is fixed at one end and can be moved vertically at the other end (figure 3(a-iii)). The bistable characteristics of inclined straight beams are similar to those of constrained curved beams. As tilt angle α increases from 0° to 90° under a constant beam slenderness ratio h/L, the beam undergoes continuous transitions from the simple steady state to monostable and eventually to bistable [18].
The bistability of inclined straight beams satisfies the condition that:

where, h is the thickness of the beam, L is the length of the beam, and α is the inclination angle of the straight beam.
(4) The rigid connection compliant mechanism with spring, as shown in figure 3(a-iv). The mechanism consists of two rotatable rigid links that are connected via a freely rotating joint and a pre-tensioned elastic linear spring that stores and releases energy [59]. Rigid constraints and pre-stretched springs cause the bistability of the mechanism, which necessitates that the length of the two rigid links (L2) be greater than the initial length of the spring (L1), i.e. L2 > L1. This structure undergoes a snap through earlier at small displacements, enabling a large range of motion with small drive inputs. Due to its absorption, storage and release of large amounts of energy, it has a wide range of applications in fast-driving robots, special sensors for switching response and wave control.
2.2.2. Thin shell structure.
The shell structure is also a common component in mechanics, which is generally expressed as a layered structure. The bistable thin-shell structures encompass a variety of forms such as the spherical dome shell structure, curved surfaces (single and double curved), '<' shaped straw thin-shell structure, Miura-ori, waterbomb origami, and Kresling origami structure, as shown in figure 3(b). Compared with beams and trusses, thin shell structures have excellent flexibility and larger contact area, and adopt the closed structure. This kind of structure can not only interact with the surrounding environment friendly, but also interact with the fluid effectively. Therefore, they can easily realize grasping, bouncing and other actions, and are more suitable for unique applications such as fluid-driven soft robotics and mechanical computing.
(1) The spherical dome shell structure is a typical 3D bistable structure [40, 60–62] (figure 3(b-i)). The initially stable convex dome structure is transformed into another stable transition state (concave configuration) when a load exceeding a certain threshold is applied to its top. Bistability with snap-through is achievable for both thin and finite-thickness dome shells. For the eversion dome shell with a large enough depth, only a small driving force is needed to quickly return to its natural state through the stored large strain energy. The spherical dome shell structure is commonly used in soft robotics, mechanical computing, energy absorption and wave control. The dimensionless parameter λd, which signifies the ratio of tensile energy Us to bending energy Ub, regulates the monostability and bistability in the dome shell. The monostable dome shell is transformed into bistable when λd exceeds the threshold value (equation (1)). The criteria for determining the 3D dome's monostability and bistability are as follows:
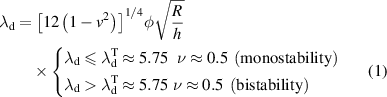
where, ν is Poisson's ratio, h is thickness, R is radius, and φ is opening angle.
(2) The bistable surface structure includes two types: the tape measure-like monocurvature cylindrical surface and the Venus flytrap-like double-curvature surface [63] (figure 3(b-ii)). In general, the bistable surface has a large length/thickness ratio, that is, l/h≫1 (l and h are length and thickness, respectively). When subjected to a bending load above a certain threshold, the monocurvature cylindrical surface undergoes a change in curvature direction and morphs into another stable structure. For double-curvature surfaces, the curvature of both axes will change during the steady-state conversion [64, 65]. The cylindrical surface undergoes a bending-based deformation, which causes its principal curvature to switch from the y-axis to the x-axis, that is, from stable state 1 to stable state 2. Long cylindrical surfaces can be compressed into compact curved shapes [66]. Bistable surface structures are often used in fast-response, low-energy grippers because of their flexibility, large effective area, and no energy required to maintain their stable shape after conversion between open and closed states. The bistability in curved surfaces is governed by the dimensionless geometric parameter η [66–68]. One can determine the bistability of the curved surface using the following formula:

where, w is the width, h is the thickness and κ0 is the curvature of the surface.
(3) The '<' shaped straw thin-shell structure is also a common bistable shell structure in which two conical shells are connected by creases [24, 52], as shown in figure 3(b-iii). The element switches between 'unfolded' and 'folded' states under tensile or compressive loading. Its deformation mode shares similarities with the Von Mises truss and rigidly connects compliant mechanisms with springs. This flexible straw structure is stretchable and foldable, and can be applied to energy absorption and shape reconfiguration. However, the strength and stability of the structure are poor, and it is challenging to accurately control the deformation of each unit. The independent flexible deformation of each '<'-shaped bistable unit under the compressive loading can easily trigger the local instability. The bistability and monostability of the '<' shaped straw thin-shell structure depend on θ1 and θ2. The structure will change from monostability to bistability with the increase of one angle (e.g. θ1) when another angle (e.g. θ2) is fixed.
(4) Miura-ori [69–71] and waterbomb origami [72] are two common bistable folding structures. The origami structure can be designed through the strategy of crease and folding deformation, which can transform the 2D structure into 3D structure. They can rapidly transition between steady states when subjected to the axial load, as shown in figure 3(b-iv), resembling the Von Mises truss structure in terms of deformation modes (figure 3(a-i)). Their origami surfaces act as rigid surfaces, while their creases function as compliant hinges. Miura-ori and waterbomb origami have negative Poisson's ratio properties, and their mechanical properties are scale-independent. They are folded from 2D materials, so the structure is lightweight and can also achieve a huge unfolding area. Therefore, they have broad application prospects in deployable devices, soft robotics, shape reconfiguration and so on. Geometric factors, including sector angle (α), remaining folding angles (γm0 and γv0), and material dimensions such as length and width, can all be modified to fine-tune their bistable behavior.
(5) The Kresling origami is a pattern formed by the buckling of a thin-walled cylinder under the axial compression and torsion [36, 73], as shown in figure 3(b-v). Its defining features are folding peaks and valleys that alternate at a specific angle along the torsion direction, and it has two regular polygons at the top and bottom. The Kresling origami structure moves through the torsional buckling deformation and the axial contraction motion, which is also known as the tension–torsional coupling. Therefore, its main applications are in the fields of soft robotics and mechanical computing. The bistability of Kresling origami depends solely on its geometric parameters and not on material properties.
2.2.3. Other bistable structures.
In addition, there are some other bistable units, such as snap-fit structure, biholar sheet structure, rotating hinge deployable kirigami structure, and square-twist origami structure, etc, as shown in figure 3(c).
(1) Snap-fit structure is a common connecting part in engineering, such as bottle cap, pen cap, equipment shell and so on. The snap-fit structure is usually composed of two parts (figure 3(c-i)): the protruding snap-fit part and the concave groove part [17, 74]. The snap-fit fits into the groove under axial compression, causing deformation and ultimately leading to rapid assembly, known as the snap-through phenomenon. Due to the snap-fit structure has less material limitation and high structural stability, high strength and strong tunability, it is often used in energy absorption, packaging structure and compressible devices. However, the snap-fit structure requires contact between the groove and the snap-fit for assembly, and the regular friction causes it to be prone to wear. The bistable attributes of snap-fit structures are dependent on the insertion surface angle α and the opening ratio d/D. A snap-fit structure will manifest bistability if the insertion surface angle α ranges from 0° to 90° and the opening ratio d/D varies from 0 to 1.
(2) The biholar sheet structure is a quasi-2D structure, which is composed of two circular holes with different aperture sizes [75–77], as shown in figure 3(c-ii). The structure is bistable when the geometric dimensions meet specific conditions [78, 79]. The round hole shrinks inward, that is, from the extended state to the bending state when compressed. In metamaterials with periodic holes, the size of the hole can adjust the stiffness, Poisson's ratio and the critical condition of steady-state conversion, which can be applied to soft robotics, shape deformation and other fields. The biholar sheet structure exhibits bistable characteristics as x
increases continuously, i.e.
x
≳0.17 [77].
(3) For the rotating hinge deployable kirigami structure [80, 81] (figure 3(c-iii)), the hinge point of the structure will bear great deformation under tensile load. The structure snaps to the second stable configuration when the load increases to a certain threshold. The kirigami structure has the same lightweight properties as the origami structure. In addition, the tensile expansion behavior generated by the structure can be isotropically adjusted to target scalability, highly flexible and stretchable devices. It is found that the thickness of the bending hinge plays a key role in the stability of the structure [80, 81], especially the thickness ratio t/l of the hinge and the width ratio a/l of the rotating. The ratio of the local minimum strain energy Emin to the strain energy barrier Emax in the stable state of structural deformation is η= Emin/Emax. The structure is bistable when η < 1.
(4) The square-twist origami structure undergoes torsional deformation and exhibits bistable properties when subjected to axial stretching/compression [82] (figure 3(c-iv)). The square-twist origami can fold by allowing the facet to bend, and it provides bistability when the bending and crease energy ratio is large enough (i.e. >1000). In addition, the square-twisted origami structure also has a negative Poisson's ratio characteristic. It allows self-unfolding by releasing pre-stored energy in the elastic fold region during steady-state transitions, leading to applications such as reconfigurable devices and soft robotics.
More steady-state units can also be realized by ingenious structural design. Zhang et al [20] designed X-shaped kirigami microstructures with tristability, which is mainly caused by the elastic tension/compression asymmetry of the kirigami microstructure. Liu et al [83] designed an origami unit with four tilted panels and four corresponding creases, and the nonlinearity of the folding motion makes the unit show three stable states (tristability). The three steady states shown in the above examples of tristable structures are sequentially arranged, that is, the transition from the first steady state to the third steady state must undergo the second steady state. This leads to the problems of low steady-state switching efficiency and short structural fatigue life. Li et al [84] proposed a new concept of compliant tristability—'non-transit' tristability structure. The structure not only has three stable states, but also can realize the direct switching between any two steady states without going through another steady state. In addition, there is no fixed number of steady-state gear structures, which can achieve stable and continuous parameter control [85]. These multistable units break the shackles of traditional bistable unit structure design and provide a new design paradigm for the design of multistable mechanical metamaterials with more novel properties.
Combining these bistable units in series, parallel, or series–parallel can form multistable structures with multiple stable configurations, known as multistable mechanical metamaterials. These metamaterials can take the form of 1D chain structures, 2D mesh structures, and 3D spatial structures [21, 58, 86, 87], for example, constrained multi-layer pre-buckling beam, multi-layer inclined beam and multi-layer Von Mises truss. The spring-based multistable linkage mechanism is a chain linkage mechanism formed by concatenating bistable units, adding additional linkages and springs to create a parallel mechanism that forms a multi-layer rigidly connected compliant mechanism with springs. Each layer of the structure will suddenly bounce under a uniaxial compression load, demonstrating bistable performance, and the multi-layer structure has multiple stable configurations.
3. Manufacture of multistable mechanical metamaterials
Traditional manufacturing processes such as mold casting, cutting and folding are commonly used to fabricate multistable mechanical metamaterials. However, with the continuous development of multistable mechanical metamaterials, the traditional manufacturing process has been difficult to meet the multi-functional and miniaturization needs of these metamaterials. Therefore, many new manufacturing technologies such as 3D printing (AM), 4D printing, and micro-nano processing have emerged. This section summarizes the main methods for the preparation of multistable mechanical metamaterials. Cutting (mechanical cutting and laser cutting) and mold casting are conventional preparation methods. AM is the most widely used method. These include macroscopic manufacturing technologies (such as direct ink writing (DIW), fused deposition modeling (FDM), stereolithography (SLA), polymer jetting (PolyJet), powder bed melting (PBF), etc), and mesoscopic/microscopic manufacturing technologies (such as projection micro SLA (PμSL), two-photon photopolymerization (TPP) technology, etc).
3.1. Molding and cutting
A simple and common method for preparing multistable mechanical metamaterials is mold casting, as shown in figure 4(a-i). Molds are often manufactured by 3D printing methods, and then cast into molds using some elastic and deformable 'soft materials' (e.g. silica gel, polyurethane, hydrogel, etc) to obtain the final structure. These soft materials themselves are often difficult to use directly for 3D printing, because they require specific curing conditions and their hardness cannot directly form a 3D structure.
Figure 4. Molding and cutting. (a) Multistable mechanical metamaterials fabricated by mold casting. (i) Schematic diagram of mold casting process. (ii) Fabrication of multistable mechanical metamaterials for large-size (centimeter-scale or larger) inclined-arm beams by molding (mold casting). [18] John Wiley & Sons. © 2015 WILEY‐VCH Verlag GmbH & Co. KGaA, Weinheim. (iii) Fabrication of digitally synthesized multi-material structures with monostable or bistable characteristics by mold casting. Reproduced with permission from [88]. (b) Multistable mechanical metamaterials processed by tool cutting. (i) Schematic diagram of tool cutting processing. (ii) Multistable, reprogrammable origami metamaterials, connected by rigid panels and hinges (including free hinges and elastic hinges). [83] John Wiley & Sons. © 2022 Wiley‐VCH GmbH. The unit panel and free hinge are milled by computer numerical control (CNC) three-axis engraving machine (precision 10 μm). The elastic hinge is cut by a four-axis CNC engraving machine (precision 20 μm). (c) Multistable mechanical metamaterials processed by laser cutting. (i) Schematic diagram of laser cutting. (ii) Multistable shape reconfigurable structural material based on kirigami by laser cutting of thick PTFE sheets. [89] John Wiley & Sons. © 2016 WILEY‐VCH Verlag GmbH & Co. KGaA, Weinheim. (iii) Laser cutting super-stretch wear-resistant natural rubber to make non-periodic compact kirigami patterns. Reproduced from [90], with permission from Springer Nature.
Download figure:
Standard image High-resolution imageShan et al [18] used the molding (mold casting) method to manufacture multistable mechanical metamaterials of inclined beams with larger sizes (centimeter scale or larger) structures (figure 4(a-ii)). A negative mold was made using a 3D printer and VeroBlue material, and the structure was cast with silicone rubber. The as-cast mixture is first degassed in vacuum and then cured at room temperature. Finally, a centimeter-scale (10.6 cm × 10.8 cm × 3.0 cm) structure was obtained.
Li et al [88] fabricated a digitally synthesized multi-material structure that can achieve any programmable mechanical response. These structures can exhibit monostable or bistable characteristics. They used a mold casting method and used two polydimethylsiloxane (PDMS) elastomers with different characteristics (PDMS 1 and PDMS 2) for digital synthesis and fabrication of multi-material structures (figure 4(a-iii)). A 3D printer based on FDM was used to make the mold. The mold was printed with terephthalate glycol polyethylene (PETG) filament, and its glass transition temperature is about 90 °C, which was higher than the curing temperature of PDMS. In order to use these two PDMS elastomers to prepare multi-material composite structures, they poured PDMS 1 into the first mold and semi-cured it to a semi-solid state. The semi-cured PDMS 1 area is then removed from the mold and inserted into the second mold, leaving only an empty groove for the PDMS 2 area in the second mold, after which the PDMS 2 is poured into the groove. Here, the semi-cured solid PDMS 1 region and the first mold together act as the 'mold' for the liquid PDMS 2. Finally, the entire structure in the second mold is cured to an all-solid-state, which completes the manufacturing.
Origami and kirigami techniques (i.e. the ancient art of folding and cutting) are often used to design multistable mechanical metamaterials. However, due to the limitation of structure and material, origami and kirigami multistable structures are often prepared by traditional processing methods. Usually, some creases or cracks are produced on thin sheet materials (such as paper, polypropylene (PP) sheet, polytetrafluoroethylene (PTFE) sheet, Mylar polyester sheet, etc) by means of cutting and carving, and then the sheet is folded, spliced or bonded. The methods used to produce these creases or cracks are mostly mechanical cutting (engraving machine engraving) and laser cutting on thin sheet materials. As shown in figure 4(b-i), the engraving machine controller controls the engraving path according to the computer aided design (CAD) diagram. The high-speed rotary engraving head can engrave various planar or 3D relief graphics and texts in the design by cutting the processing materials fixed on the main engine working table with the tool configured according to the processing materials.
Liu et al [83] proposed multistable, reprogrammable origami metamaterials, as shown in figure 4(b-ii). These origami metamaterials are connected by rigid panels and hinges (including free hinges and elastic hinges). Finely designed panels and hinges are required to allow the perfect assembly of elements and 2D tessellations. Each element panel is made of 2 mm thick polycarbonate (PC) (Makrolon® polycarbonate, E= 2300 MPa) sheet milled by a CNC three-axis engraving machine (with accuracy of 10 μm). The free hinge is cut off from a 1 mm thick white PP sheet using the same engraving machine as the PC panel. PP is selected because of its excellent folding performance and fatigue resistance. This allows the creation of very thin (0.2 mm) folded lines, resulting in zero energy hinges, i.e. almost perfect free hinges. The folding line is obtained by a ball end mill (with radius of 1 mm) mounted on the milling machine. The elastic hinge is realized by cutting the silicone rubber entity (600 mm × 30 mm × 40 mm) with a four-axis CNC engraving machine (with precision of 20 μm). This rubber hinge leads to the multistability of the unit cell because it can store energy when folded. Finally, the panel and hinge are bonded together to form a unit cell.
Another advanced and widely used cutting process is laser cutting. It is a processing method for the thermal cutting of materials using a high-energy-density laser beam as a 'cutting tool' (figure 4(c-i)). Laser cutting technology can be used to cut various metals, non-metallic plates, composite materials, etc, and has been widely used in various fields. Laser cutting is the use of focused laser beam irradiation of the workpiece, so that the irradiated material is rapidly melted, vaporized, ablated or reached the ignition point, while the use of high-speed airflow coaxial with the beam to remove the molten material, so as to achieve cutting the workpiece. The cutting quality of the laser is excellent. Not only is the cutting speed fast and the dimensional accuracy high (up to ±0.05 mm), but the workpiece is almost distortion-free because the laser beam is applied to a very small area with a small heat-affected zone.
Haghpanah et al [89] proposed a multistable shape reconfigurable structural material based on kirigami (figure 4(c-ii)). This structural material is manufactured by laser cutting thick PTFE sheets. The laser wavelength is 630–680 nm, and the maximum laser power is 1 mW. The manufacture of the 3D structure includes the production of 2D laser cutting parts of Teflon, and then assembly and bonding using screws and nuts.
Choi et al [90] proposed a reverse design method to construct an approximately conforming target shape (figure 4(c-iii)). This reverse design method allows the creation of non-periodic compact kirigami patterns that can approximate any given shape in two or three dimensions when expanded. To experimentally verify the design of some 2D and 3D deployable shapes, they made physical models by laser cutting a piece of super-stretched, abrasion-resistant natural rubber.
3.2. AM techniques for multistable mechanical metamaterials
The development of AM technology makes it possible to fabricate complex multistable mechanical metamaterials, which is beyond the capability of traditional subtractive manufacturing methods. The AM techniques for the preparation of multistable mechanical metamaterials are summarized below.
3.2.1. Material extrusion.
Extrusion-based 3D printing methods, such as DIW [93, 94] and FDM [95, 96], are widely used due to their affordability and ease of operation. DIW involves the extrusion of viscous liquid ink through a nozzle onto specific 2D slices, forming filaments that build up layer by layer to create a complete 3D part (figure 5(a-i)). Similarly, FDM melts the material at a high temperature before extruding it through the printing nozzle to form continuous filaments that are deposited on a construction platform (figure 5(b-i)). The nozzle draws a 2D slice of the desired shape and repeats this process until a 3D part is formed.
Figure 5. Extrusion-based 3D printing method. (a) Multistable mechanical metamaterials fabricated by direct ink writing (DIW) 3D printing. (i) Schematic diagram of the working principle of direct ink writing (DIW) using viscoelastic ink. (ii) Multistable mechanical metamaterials based on inclined beam was constructed by DIW. [18] John Wiley & Sons. © 2015 WILEY‐VCH Verlag GmbH & Co. KGaA, Weinheim. (iii) Multistable mechanical metamaterials based on Von Mises truss was constructed by DIW. Reproduced with permission from [37]. (b) Multistable mechanical metamaterials fabricated by fused deposition modeling (FDM) 3D printing. (i) Schematic diagram of the basic working principle and device of fused deposition modeling (FDM). (ii) The macro size NAND logic gate is constructed by FDM. Reproduced from [27]. CC BY 4.0. (iii) The multi-step metamaterials are constructed by FDM. Reprinted from [91], © 2020 Elsevier Ltd. All rights reserved. (iv) Double-U-type multi-stable mechanical metamaterials are constructed by FDM. Reprinted from [92], © 2018 Elsevier Ltd. All rights reserved. (c) Multistable mechanical metamaterials fabricated by multi-material FDM 3D printing. (i) The basic working principle of multi-material FDM. (ii) The multi-stable deformation structure is constructed based on the origami module prepared by the multi-material FDM AM process. [28] John Wiley & Sons. © 2022 Wiley‐VCH GmbH.
Download figure:
Standard image High-resolution imageDIW technology supports a wide range of inks, such as conductive gels, elastomers, and hydrogels. These inks have rheological properties (such as viscoelasticity, shear thinning, yield stress, etc) that contribute to the implementation of the 3D printing process. Shan et al used DIW technology to extrude viscoelastic PDMS ink from the nozzle to construct 3D multistable mechanical metamaterials based on inclined beams [18] (figure 5(a-ii)) and Von Mises trusses [37] (figure 5(a-iii)). The conical inner diameter of the nozzle can be adjusted according to the required structural size, and the extrusion of ink is controlled by a pressure box. A custom 3D positioning table is used to control the precise position of the nozzle. The PDMS-based ink is rheological to ensure that the uncured ink is fluid and retains its shape during the printing process. The printed model is then cured to produce permanent cross-linking to maintain a stable shape. Although DIW technology has many advantages, the diameter of extruded filaments is usually limited by the nozzle diameter, and the pattern deposited is limited by the nozzle movement path, which limits the application of DIW technology on multistable mechanical metamaterials.
Similar to DIW technology, FDM technology has a fast-forming speed and a wide variety of supporting materials, such as polylactic acid (PLA), thermoplastic polyurethane (TPU), acrylonitrile–butadiene–styrene copolymer (ABS), and nylon (PA, including PA6, PA12, etc). These thermoplastic polymer materials have excellent mechanical properties and are, therefore, very popular in the preparation of multistable mechanical metamaterials. Song et al [27] used ABS-M30™ material to print macro-sized NAND logic gates with a commercial FDM 3D printer (figure 5(b-ii)). Due to the excellent ductility of TPU, the designability of the structure with TPU can be improved. Meng et al [91] proposed multi-step metamaterials made of TPU, which was fabricated using AM method—FDM technique (figure 5(b-iii)). Yang and Ma [92] designed double-U-type multistable mechanical metamaterials based on a curved beam. This metamaterial is prepared by the thermoplastic elastomer material based on FDM technology.
Multi-material AM technology is an important means to realize integrated molding of multi-material metamaterials. Figure 5(c-i) shows the multi-material AM technology based on FDM technology. This technology is implemented with multiple nozzles that allow the deposition of different materials in the same or different areas. Melancon et al [28] constructed a multistable deformation structure by connecting 3D printed origami modules. Each origami module is 3D printed using a multi-material printer, as shown in figure 5(c-ii). Considering the geometric incompatibility of the origami module during expansion deformation, the material (TPU) prints a small triangular surface of 1 mm thickness. At the joint of the triangular face (hinge), the thickness is reduced to 0.4 mm, allowing more flexibility. In addition, in order to achieve rigid connection and bistability of different units, rigid PLA was used to print four triangular faces of the end cap and bistable unit. Coupling between units is achieved through screws and holes.
FDM technology is appropriate for applications that involve relatively simple geometries and do not require high levels of accuracy. Nevertheless, its use in preparing high-precision multistable mechanical metamaterials often poses challenges.
3.2.2. Vat photopolymerization, inkjet printing and powder bed fusion.
Vat photopolymerization is another commonly utilized AM technique for creating multistable mechanical metamaterials. Here, we mainly discuss the preparation of macroscopic multistable mechanical metamaterials by vat photopolymerization. Specifically, SLA was the first commercially available 3D printing method that aimed to achieve high precision, large scale, and fast printing speed. Mesoscopic and microscopic multistable mechanical metamaterials prepared by vat photopolymerization will be discussed in section 3.2.3.
The SLA system uses ultraviolet (UV) light to irradiate into a liquid vat containing liquid photosensitive (IP-S) resin, as shown in figure 6(a-i). The UV laser under the control of the computer scans the liquid resin connection points according to the contour of each layer section of the predetermined part. The thin resin layer in the scanned area generates a photopolymerization reaction, thus forming a thin layer section of the part. The uncured resin continues to exist in the liquid vat and provides raw material support for the part being manufactured. After printing, the cured resin layer moves downward with the working platform in the liquid, and the next polymer layer continues to repeat the above process at the top of the layer. This process continues until the parts are removed from the liquid medium according to the process of CAD, and finally, a 3D solid model is obtained. Xu et al [74] proposed snap-fit mechanical metamaterials with multistable, reprogrammable and reusable properties, as shown in figure 6(a-ii). Inspired by the 3D needle carving array mode, the pixel mechanical metamaterials were developed. The multistable mechanical metamaterials consist of two parts, the snap-fit tube structure and the groove structure. The metamaterials are designed to be modular in order to adapt to complex environments and applications on different occasions. The modular snap-fit tube and groove structure are prepared by SLA 3D printing. The perfectly matched snap-fit tubes and grooves were finally printed and then assembled into multistable mechanical metamaterials through rational structural design (figure 6(a-ii)).
Figure 6. Vat photopolymerization, material jetting and powder bed fusion. (a) Multistable mechanical metamaterials fabricated by stereolithography (SLA) 3D printing. (i) The working principle of stereolithography (SLA) of photocuring resin. (ii) The snap-fit mechanical metamaterials were fabricated by stereolithography (SLA). Reprinted from [74], © 2022 Elsevier Ltd. All rights reserved. (b) Multistable mechanical metamaterials fabricated by material jetting (MJT) 3D printing. (i) Schematic diagram of the working principle of PolyJet (polymer injection) technology (material jetting (MJT) technology). (ii) Frictional metamaterials based on snap-fit structure were prepared using PolyJet technology. Reprinted from [97], © 2020 Published by Elsevier Ltd. (iii) Scalable tri-stable hierarchical mechanical metamaterials were prepared by multi-material PolyJet 3D printing. From [20]. Reprinted with permission from AAAS. (iv) Multi-material PolyJet technology is used to prepare multi-plane mechanical metamaterials based on bistable Von Mises truss. Reprinted from [98], Crown Copyright © 2020 Published by Elsevier Ltd. All rights reserved. (c) Multistable mechanical metamaterials fabricated by powder bed fusion (PBF) 3D printing. (i) The working principle of selective laser sintering (SLS) and selective laser melting (SLM). (ii) 3D printing based on SLS technology to realize the concept of multistable design on the surface of Schwarz's Primitive shell. [21] John Wiley & Sons. © 2021 Wiley‐VCH GmbH. (iii) Fabrication of mechanical metamaterials based on bistable curved beams by SLS. [51] John Wiley & Sons. © 2015 WILEY‐VCH Verlag GmbH & Co. KGaA, Weinheim. (iv) Fabrication of friction metamaterials by AM based on SLM technology. Reprinted from [97], © 2020 Published by Elsevier Ltd. (v) Fabrication of modular multistable metamaterials with reprogrammable mechanical properties: the double-beam frame is prepared by FDM technology, and the connecting rod and M-shaped rod are prepared by SLS technology. Reprinted from [99], © 2022 Elsevier Ltd. All rights reserved.
Download figure:
Standard image High-resolution imageAlthough vat photopolymerization is widely used, the material used in printing is photosensitive resin, which has insufficient mechanical properties (brittleness and toughness) [100, 101]. There are many resins that need to be stored in the liquid vat when printing large-size structures, resulting in more resin volatilization and waste of raw materials [74]. If you need to replace different materials or multi-material printing, the operation is difficult. These shortcomings limit its application in multistable mechanical metamaterials.
At present, some improved vat photopolymerization AM or post-processing technologies are expected to improve the mechanical properties of multistable mechanical metamaterials. The 'pyrolysis' method of vat photopolymerization can enhance the strength of materials without sacrificing ductility. Surjadi et al [102] adopted a low-cost, facile pyrolysis process, which can greatly improve the stiffness, strength and ductility of photocurable 3D printed polymer microlattices. Saccone et al [103] developed a new hydrogel infusion AM technology via vat photopolymerization for the production of metals and alloys with microscale resolution structures. The obtained metal has a highly twinned microstructure and extremely high hardness, which provides a new way to fabricate advanced metal micromaterials. Wang et al [104] controlled the exposure time of photopolymerization, so that 3D printing can distribute rigid segments and flexible segments at a specific position to form an elastic dual-network structure (toughness can be increased by 100%). In addition, there are many commercial high-performance resins (e.g. high-strength resin, elastic resin and flexible resin etc) are also emerging. These high-performance resins, advanced vat photopolymerization AM and post-processing technologies provide a feasible solution for the manufacture of high-strength, and high-toughness multistable mechanical metamaterials.
Material jetting (MJT) technology is similar to the 2D inkjet printer method in that it is sprayed onto the build platform by continuous or drop-on-demand. MJT technology is known for its ability to print multiple materials (such as polymers, metals, ceramics, etc). PolyJet (polymer jetting), a technique proposed by Objet Geometries (Stratasys Ltd), is widely used. The basic principle is as shown in figure 6(b-i), where IP-S polymer droplets are ejected from the nozzle and cured under UV light (similar to SLA technology) by building layer by layer until the part is complete. This 3D printing technology allows two or more photosensitive polymers to be deposited side by side in a predetermined ratio. In this way, PolyJet allows the creation of a so-called digital material, a group of materials whose properties can be digitized within a certain range. Garland et al [97] proposed friction metamaterials using MJT technology to demonstrate this strategy. A PolyJet 3D printer was used to spray the photocuring polymer to prepare 'macropolymer' elements (figure 6(b-ii)). The effects of elastic modulus, minimum printable feature size, nonlinear deformation process, surface roughness and subsequent friction coefficient on energy dissipation of friction metamaterials are investigated. The results show that the damping coefficient η of this polymer structure is as high as 0.226, which has good energy dissipation ability. Zhang et al [20] designed scalable tristable hierarchical mechanical metamaterials for ternary logic operations and amplitude modulation. The mechanical metamaterials are fabricated using multi-material PolyJet 3D printing (figure 6(b-iii)). Two different materials (Vero White Plus and Tango Black Plus) were obtained by a multi-material 3D printer and cured with UV light at room temperature. Tango Black Plus (black) is a soft elastomer (∼0.5 MPa) used to fabricate X-shaped kirigami microstructures. The tristability of the element can be achieved by elastic tension/compression asymmetry of the X-shaped kirigami microstructure. Vero White Plus (white) is a hard polymer (∼680 MPa) as a rigid framework for the structure. Waheed et al [98] used PolyJet technology to prepare multi-plane mechanical metamaterials to realize Boolean AND/OR mechanical logic (figure 6(b-iv)). The PolyJet technology is suitable for printing complex geometries due to its multi-material printing capability. In addition, the use of digital materials provides better material property control for different parts of mechanical metamaterials. The metamaterials are based on a bistable Von Mises truss structure, and the joints will undergo bending deformation during the steady-state transition. Therefore, three different materials (Vero White, FLX9950 and FLX9960) were used for printing. Vero White is a rigid polymer used to manufacture unit cell corners, center shuttle and thin truss members. The rigid corners are connected to the thick flexible member, using a digital material FLX9950 (Shore hardness of 35–40 A, elongation at break of 110%–130%) to prevent the Von Mises truss from tearing during the steady-state transition. The flexible hinges of the bistable system are made of digital material FLX9960 (Shore hardness of 57–63 A, elongation at break of 75%–85%). Although the material is stronger and less elastic than the FLX9950, it adds a larger deviation to the system to ensure that a bouncy response can be achieved. When printing, a soluble support structure is used. After the printing is completed, the parts are dissolved in a corrosive solution of sodium hydroxide and sodium metasilicate to dissolve the supports.
PBF utilizes thermal energy to bond powder materials together to form 3D polymer or metal parts. It can be divided into four categories, which are selective laser sintering (SLS) technology, selective laser melting (SLM) technology, electron beam melting (EBM) technology and multi-jet fusion (MJF) technology. The main differences between these types are their heat sources and temperature ranges. EBM and SLM are usually used to print metal parts, while SLS and MJF are usually used to print polymer parts. SLS and SLM are common methods for preparing multistable mechanical metamaterials. Their principles are similar, as shown in figure 6(c-i). During the printing process, the powdered material is spread on the substrate plate, and the laser beam selectively sinters the powder material in the specified area. And then, another layer of powder is spread on the previously sintered layer, and the above sintering process is repeated. Finally, the powder is sintered together to form a 3D powder sintered part. Shi et al [21] implemented the multistable design concept on Schwarz's Primitive shellular using two perforation strategies. This strategy is implemented by 3D printing based on SLS technology (figure 6(c-ii)). A thin layer of TPU powder was laid on the build platform, and then a CO2 laser (Sinterstation 2500 and 50 W CO2 laser) selectively sintered TPU powders according to the slice structure pattern. After printing is completed, the build platform moves down and the blade places the new powder in the build area. This process will be repeated until the entire perforated shellular is 3D printed. An outstanding advantage of SLS over other printing methods, such as FDM, SLA, and DIW is that the un-sintered underlying powder provides support for the next layer, which applies to those perforated shellular metamaterials with overhangs. The un-sintered powder in the structure is removed with a brush when the 3D printing process is complete and then polished in an abrasive blast cabinet with spray beads. Rafsanjani et al [51] proposed snapping mechanical metamaterials based on a bistable double-curved beam structure (figure 6(c-iii)). Those mechanical metamaterials (5 × 5 cells, with thickness of 3 mm) were prepared by SLS technique, and the materials used are nylon-based rubber materials (Young's modulus E≈ 78 MPa, Poisson's ratio ν≈ 0.4). The friction metamaterials proposed by Garland et al [97] also used AM methods based on SLM technology. The friction metamaterials of 316l stainless steel were obtained, as shown in figure 6(c-iv). The damping coefficient η of structural element is 0.507, which is obviously higher than that of natural material. Mao et al [99] proposed a strategy for modular multistable metamaterials with reprogrammable mechanical properties, which are assembled from unit cells with tunable snap-through behavior. The unit cell is composed of detachable rods and a fixed frame, which contains two bistable curved beams. The shape of the curved beam can be changed by inserting rods of different lengths into the frame, thereby regulating the snap-through behavior of the unit cell. All components, including double-beam frames, M-bar and horizontal and vertical connecting rods, are manufactured through AM. The double-beam frame was prepared with TPU (Young's modulus E = 180 MPa) and using FDM technology. Nylon 7100 (E = 1.0 GPa) was used to print connecting rods and M-bars by SLS technology. The heights of the two curved beams change synchronously when the M-bars with different lengths are inserted, and the geometry and mechanical response of the unit cells can be adjusted. Therefore, these tunable unit cells can be assembled with horizontal and vertical links to form multistable mechanical metamaterials with programmable mechanical properties (figure 6(c-v)).
3.2.3. Micro-nano 3D printing.
The main difference between micro-nano 3D printing and 'traditional' 3D printing is that micro-nano 3D printing can achieve high precision that 'traditional' 3D printing cannot. The precision of micro-nano 3D printing can reach meso-, micro- and nano-scale. This characteristic enables micro-nano 3D printing to mass-produce multistable mechanical metamaterials of microstructures. At present, the commercial micro-nano scale 3D printing methods mainly include PμSL technology and TPP technology.
PμSL is a micro-scale and ultra-high-precision light-curing AM technology (figure 7(a-i)), which belongs to the vat photopolymerization family. Its basic principle is similar to that of digital light processing (DLP) [106]. The 3D model that needs to be printed is projected layer by layer onto the IP-S resin and accumulated layer by layer. Finally, the 3D sample is directly processed from the digital model through the above rapid light curing molding process. The difference is that PμSL technology designs and optimizes the optical projection system to reduce the projection size of a single pixel to a micron or even submicron. Song et al [27] used three different 3D printing techniques to fabricate novel micromechanical logic gates. The basic element of a mechanical logic gate is a bistable Von Mises truss structure. A mesoscale (∼25 mm × 25 mm) NAND logic gate was printed using PμSL (custom machine, material: PR57 resin), as shown in figure 7(a-ii). Mei et al [35] proposed mechanical metamaterials with reprogrammable logic functions. The basic element of mechanical metamaterials is a bistable curved beam structure. In order to verify the mechanical response and mechanical logic operation of the structure on the mesoscale, mesoscopic scale signal elements were prepared, as shown in figure 7(a-iii). The signal element is composed of two connectors and a supporting curved beam. These components are made of ultra-tough low-viscosity resin and printed by a 3D printer (microArch P150).
Figure 7. Micro-nano 3D printing. (a) Multistable mechanical metamaterials fabricated by projection micro stereolithography (PμSL) 3D printing. (i) Schematic diagram of the working principle of the projection micro stereolithography (PμSL) technique. (ii) Projection microstereolithography prints mesoscale (about 25 mm × 25 mm) Von Mises truss-based NAND logic gates. Reproduced from [27]. CC BY 4.0. (iii) The PμSL technique prints mesoscopic-scale curved beam-based signal elements. Reproduced from [35]. CC BY 4.0. (b) Multistable mechanical metamaterials fabricated by two-photon photopolymerization (TPP) 3D printing. (i) The working principle of two-photon photopolymerization (TPP) 3D printing technology. (ii) The micro-scale bistable bending mechanism fabricated by two-photon photocuring (2PS) can be driven between two stable positions. Reproduced from [27]. CC BY 4.0. (iii) TPP system prints snap-through metastructures for manipulating micro-objects. From [105]. Reprinted with permission from AAAS. (iv) Multistable micro-lattices based on a bistable curved beam were printed by TPP 3D printing technology. [39] John Wiley & Sons. © 2016 WILEY‐VCH Verlag GmbH & Co. KGaA, Weinheim.
Download figure:
Standard image High-resolution imageAnother common micro-nano 3D printing technology is TPP, which utilizes the nonlinear characteristics of two-photon or multiphoton absorption to achieve photopolymerization (figure 7(b-i)). Different from the single-photon absorption polymerization of SLA/DLP/PμSL, TPP technology uses a near-infrared laser with a longer wavelength and lower energy as the curing light source, and the photosensitive resin at the focus absorbs two or more photons to cause a photocuring reaction. The probability of being absorbed and Rayleigh scattering is small due to the low photon energy, making it easy to penetrate the medium. The photoinitiator will produce two-photon absorption (TPA) at the focus of the beam with high photon energy, which triggers the polymerization and curing of the photosensitive resin and can produce 3D entities of various shapes. The intensity of the incident light outside the beam focus position is not strong enough to produce TPA by adjusting the intensity of the incident light, and only the beam focus position produces TPA, resulting in a polymerization reaction. The incident light can pass through the liquid resin, limiting the polymerization reaction to a very small area of the beam focus position, curing volume pixels in a tiny region of space. Therefore, TPP can achieve nanoscale AM. Song et al [27] used three different 3D printing techniques to fabricate new micromechanical logic gates. In order to fabricate and test the proposed mechanical logic gates on a microscale, a novel approach is to combine two-photon photocuring (2PS) and holographic optical tweezers (HOT) into a single device. As shown in figure 7(b-ii), the prepared microscale bistable mechanism can be driven between two stable positions. The two-photon 3D printing method is used to print polymer structures with submicron resolution, and the HOT method is used to apply optical trapping forces to the structure to introduce stored strain energy into bending. A custom photopolymerized resin is specially designed for the hybrid 2PS/HOT manufacturing process, as the low viscosity and refractive index differences between cured and uncured polymers make HOT-based operations possible. The overall size of the final bistable structure is 38 μm × 38 μm × 3 μm, and the bending thickness is 800 nm. Zhang et al [105] designed a bioinspired snap-through metastructure for manipulating micro-objects (figure 7(b-iii)). The metastructure uses a TPP system GT+ printing and consists of two materials with different stiffness. The rigid frame is printed using IP-S resin (Young's modulus ≈ 1.3 GPa). In the second printing step, the bending beam element and the laminated spring are printed using a custom-made urethane(meth)acrylate resin (Young's modulus ≈ 30 MPa). In order to reduce the friction between the deformable curved beam element and the rigid frame, a 14 μm gap is introduced in the design. The larger gap can suppress the snap-through instability when it meets the design needs. Frenzel et al [39] proposed multistable microlattices (figure 7(b-iv)) using a bistable curved beam to achieve multistable mechanical metamaterials for energy absorption at the microscale. The samples were fabricated by the Photonic Professional GT laser lithography system. The system uses a frequency-doubled erbium fiber laser with a central wavelength of 780 nm and a pulse length of 90 fs to polymerize IP-S resin through multi-photon absorption. The small volume solidified in the galvo-scanning mode is spliced by the mechanical stage. The microlattices are divided into 162 segments with a volume of 400 nm × 350 nm × 50 nm.
3.2.4. 4D printing.
Tibbits first proposed the concept of 4D printing in 2013 and demonstrated the research results of 4D printing [107]. 4D printing technology is 3D printing on the basis of 3D coordinate axis increased 'space-time axis'. 4D printing is a kind of intelligent manufacturing technology. The shape, performance or function of the components prepared by 4D printing can change at any time or in space under the stimulation of the external environment (thermal, light, pH, moisture, electricity and magnetic field, etc), which has the intelligent characteristics of self-perception and self-execution [108–112]. The basic principle of 4D printing is the same as that of 3D printing. The difference is that the materials used in 4D printing are intelligent materials with stimulus responses. Figure 8(a) shows the principle and application of 4D printing based on extrusion 3D printing (a 4D printing gripper that grabs an object under external stimuli and drops it when the stimulus is removed).
Figure 8. 4D printing. (a) 4D printing concept demonstration, and the principle and application of 4D printing based on extrusion 3D printing. (b) Shape memory materials (SMPs) are introduced into the rotating multistable structure by 4D printing technology. [113] John Wiley & Sons. © 2018 WILEY‐VCH Verlag GmbH & Co. KGaA, Weinheim. (c) A temperature-controlled recoverable multi-material bistable structure was fabricated by a 3D printer based on FDM technology. Reprinted from [114], © 2020 Elsevier Ltd. All rights reserved.
Download figure:
Standard image High-resolution imageBecause the multistable mechanical metamaterials cannot recover after deformation, their reusable properties are limited. However, combined with 4D printing technology, the deformed multistable mechanical metamaterials can be restored to their initial shape. Jeong et al [113] introduced shape memory polymers (SMPs) into rotational multistable structures, as shown in figure 8(b). Based on the multi-material 4D printing technology, two different digital SMPs were utilized to achieve controllable large-angle and thermally-driven actuation. They used a multi-material 3D printer based on PolyJet technology to fabricate active multistable structures. The PolyJet technology is an ideal multi-material 4D printing method because it can print multiple materials simultaneously. The inner cross of the multistable structure is connected to the outer ring through two pairs of SMPs beams. The inner cross can be alternately rotated to two stable states while the outer ring remains unchanged. In the design of a multi-material multi-stable structure, a pair of SMPs beams are made of rigid digital material (GD8530-DM, beam thickness: 0.6 mm), which satisfies the condition of rotational bistable reverse lateral deformation. The other pair of SMPs beams are made of rubbery digital materials (FLEX9895-DM) with varying in thicknesses (0.6–1.2 mm) that do not meet the bistable condition. The rigid SMPs beams with fixed boundaries define the overall bistability, and the SMPs beams with fixed boundaries act as control knobs. They make the potential drop at the second steady state shallower, making the heat-activated rotation easier. This multi-material 4D printing adjusts the balance between the energy barrier force and the shape memory recovery force, so that a multistable structure enables controllable thermal actuation. Niknam et al [114] proposed a tunable thermal bistable multi-material structure, as shown in figure 8(c). The thermal softening behavior of two different polymers was utilized to design a bistable bi-material structure that reverts to its original shape when the environment reaches the trigger temperature. The hard and soft parts of the bistable bi-material structure are made by a 3D printer based on FDM technology. The soft parts are printed using commercial TPU filaments and the rigid parts are printed using commercial carbon fiber-reinforced nylon. The printed parts are assembled and bonded using a commercial cyanoacrylate adhesive to form a multi-material bistable structural element.
Although the aforementioned 3D printing technologies have satisfied most of the current manufacturing of multistable mechanical metamaterials, many new 3D printing technologies have emerged in recent years to provide a better platform for the manufacturing these metamaterials. The volumetric AM techniques via tomographic reconstruction allow direct one-off printing of 3D objects without layer-by-layer printing [115]. The SLA 3D printing approach for polymeric components with mobile liquid interfaces to reduce the adhesion between the interface and the printed object allowing for a continuous and fast printing process [116]. This technology can be used to rapidly manufacture large-size multistable mechanical metamaterials, and the materials can maintain excellent mechanical properties, which is very beneficial to mechanical metamaterials. The combination of artificial intelligence (AI) and AM can be used to solve the problems faced in the process of AM [117], such as design optimization, defect detection, parameter control and so on. At present, some commercial AM simulation software provides an intelligent design scheme for AM. With the continuous development of multi-material 3D printing and 4D printing technology [118, 119], the properties of 3D printing materials (especially mechanical properties, such as strength, toughness, etc) have been significantly improved, and the application fields (e.g. aerospace, biomedical, electronic equipment, driver/robot technology, etc) of traditional 3D printing have also been broadened. It is worth mentioning that the holistic concept of 'material-structure-performance integrated additive manufacturing' [120] has promoted the development of high-performance and multi-functional metamaterials (especially multistable mechanical metamaterials). These 3D printing technologies break through the existing 3D printing technology and provide opportunities for the manufacture of novel and complex multistable mechanical metamaterials.
3.3. Other manufacturing methods
Many of the methods described above (especially AM technology) have become the most popular choices for manufacturing multistable mechanical metamaterials, but there are also other manufacturing methods used, although they may be limited. Holmes and Crosby [121] prepared micron-scale surface structures with snap-through properties by mimicking the opening and closing of Venus flytrap leaves (figure 9(a)). In order to fabricate this surface structure, they use the Euler buckling of the plate to generate a controllable microlens shell array under equal biaxial compressive stress. First, a cylindrical photoresist is attached to the silicon wafer, and a micro-mode PDMS elastomer is attached to the silicon wafer to form a series of holes. Then this elastic PDMS hole array is placed in an equal biaxial strain through a simple inflation process. A thin layer (∼1 μm) of cross-linked PDMS coated with uncured PDMS (15–60 μm thick) is placed on the surface of the strain hole. The assemblies were heated to crosslink the uncured PDMS and bind the film to the hole array under equal biaxial stretching. The release of tension leads to the development of equiaxial compressive strain in thin PDMS coatings. The associated compressive stress causes the PDMS circular plates on each hole surface to buckle, resulting in a convex array. Pan et al [24] proposed a novel design strategy for mechanical pixel arrays inspired by the spines of hedgehogs. The mechanical pixel array is composed of multiple multistable mechanical pixel elements and a frame (figure 9(b)). The multistable mechanical pixel element consists of a commercial flexible pipette (PP) and a carbon fiber tube. One end of each pipe is connected to the carbon fiber tube with glue, and the other end is connected to the frame. The frame consists of two panels with patterned holes and pillars. The panel is made of polymethyl methacrylate sheet with a size of 200 mm × 200 mm × 9 mm and is formed by laser cutting. The double-sided panel adopts a combination of standard bolts, gaskets and double screw studs. The other end of the pipe structure of the module is connected to the hole of the panel with glue. Fu et al [48] developed programmed granular metamaterials. Three multistable granular metamaterials elements are designed by connecting a rough rigid cylinder or sphere with a stretchable component (figure 9(c)). These three forms are: (1) cylinders bound by elastic bands, (2) spheres threaded by elastic strings, and (3) spheres wrapped by elastic membranes. The first design is to twine the ends of three identical polycarbonate tubes with two identical rubber bands (linear elastic materials). They used three different diameters of rubber bands to wind the tube to achieve different preload and stiffness. A plurality of cylindrical-elastic band elements is periodically arranged to construct cylindrical-elastic band metamaterials with an orthogonal laminated structure, each layer comprising two parallel elements. A rubber band is added between the adjacent two layers to construct a complete structure. In the second design, multiple spheres are connected together by elastic strings as basic units to construct two structures. The first structure is an 'interstitial orthogonal tetrahedra' structure, which contains orthogonal layers of parallel units with predetermined spacing, and adjacent parallel layers are staggered. The second structure has no gap spacing between units in the same layer and is called a 'dense orthogonal cubic' structure. The third design is to use an elastic membrane to wrap spheres of different diameters. The ball-membrane metamaterials were prepared by molding method, and the mold was manufactured by 3D printing. A silicone elastomer (Ecoflex 00-30) is cast into the cavity formed by the mold. After curing, the Ecoflex membrane is demolded. Then the membrane is filled with small spheres. The arrangement of the spheres in the membrane is ordered when the diameter of the sphere is large (e.g. ϕ = 18 mm), and the arrangement of the spheres is disordered when the diameter of the sphere is much smaller than the diameter of the membrane (e.g. ϕ = 2 mm). Fu et al [122] developed a new mechanically guided assembly method using compressive buckling for constructing complex 3D micro/nanostructures from 2D micro/nano films. This method is suitable not only for a wide range of materials (e.g. semiconductors, polymers and metals), but also for a wide range of lengths (e.g. from 100 nm to 30 mm). This method transforms the 2D film pattern into the target 3D structure through the action of compression force, and realizes the reversible switching of the 3D structure between different configurations by changing the path of compression deformation. As shown in figure 9(d), a 2D precursor is mounted on a fully stretched substrate and its end is connected to the elastic substrate using an oxide adhesive. Two different 3D conformations can be obtained by different unloading methods. The shape I conformation is obtained by unloading the substrate material along both x and y directions simultaneously, while shape Ⅱ conformation is obtained by unloading the substrate material first along the x direction and then along the y direction. Figure 9(d) shows a membrane-like 2D precursor that can be reconfigured into different stable states. This design mainly depends on the deformation of the elastomer platform in different time series, and changes the 3D configuration of the mesoscopic structure supported by the platform through the nonlinear buckling of the material. This method provides a new design strategy for multistable mechanical metamaterials and has important applications in reconfigurable and tunable devices.
Figure 9. Other manufacturing methods for multistable mechanical metamaterials. (a) A controllable microlens shell array is generated under equal biaxial compressive stress for the preparation of micron-scale surface structures with snap-through characteristics. [121] John Wiley & Sons. Copyright © 2007 WILEY‐VCH Verlag GmbH & Co. KGaA, Weinheim. (b) Multistable mechanical pixel array composed of flexible straws and carbon fiber tubes. [24] John Wiley & Sons. © 2019 WILEY‐VCH Verlag GmbH & Co. KGaA, Weinheim. (c) Three kinds of multistable granular metamaterials unit cells are designed by connecting rough rigid cylinders or spheres with stretchable components. [48] John Wiley & Sons. © 2019 WILEY‐VCH Verlag GmbH & Co. KGaA, Weinheim. The unit cell is assembled into a programmed granular metamaterial. (d) A mechanically guided assembly method using compressive buckling is used to construct complex 3D micro/nanostructures from 2D micro/nanofilms. Reproduced from [122], with permission from Springer Nature.
Download figure:
Standard image High-resolution image3.4. Multi-physical field control
Soft-driven materials can change their shape, structure and properties under external fluid (e.g. gas, liquid) driving or external stimuli (e.g. electricity, light, thermal, pH, solvent, moisture and magnetic field) [123, 124]. The former is mechanical drive, and the latter is non-mechanical drive. Common soft drive materials include ecoflex [44], PDMS [33], electroactive polymers [63], SMPs [125], hydrogels [126], liquid crystal polymers [127], etc. The multistable mechanical metamaterials under the control of multiple physical fields can be obtained by introducing these soft-driven materials into the design of metamaterials. Soft-driven materials can be deformed in response to mechanical forces or stimuli such as electricity, light, temperature, pH, solvents, moisture, and magnetic fields to achieve active or passive driving of multistable mechanical metamaterials. We discuss representative examples of different driving strategies, as well as their characteristics and applications, as shown in table 1.
Table 1. Representative examples based on actuation methods and their characteristics and applications.
Actuation methods | Actuating materials | Structural forms | Snap-through timescale and size | Applications | References |
---|---|---|---|---|---|
Mechanical force | 3D printed ABS and TPU | Miura-ori | 80 ms (100 mm × 100 mm × 2.2 mm) | Grasping robot | [133] |
Pneumatic actuation | Ecoflex and 3D printed Vero White | Curved beam | ≈37 ms (22.8 mm × 10 mm × 6.55 mm) | High-speed swimming robot | [44] |
Dielectric actuation | Dielectric elastomer: polyacrylate film (VHB) and polyimide or polyester films | Single curved surface and double curved surface | 200 ms (≈60 mm × 15 mm × 1.025 mm) | Grasping robot | [63] |
Light-driven actuation | Azo-liquid crystal networks (LCNs) | Curved beam | ≈200 ms (≈23 mm × 4 mm × 20 μm) | Self-cleaning and Light-driven crawler | [127] |
Thermal actuation | Liquid crystal elastomers (LCEs), PDMS and neodymium magnets | Kirigami (based on rotating squares) | — (≈20 mm × 20 mm × 1.5 mm) | Wave control, reconfigurable structure and thermally driven crawler | [131] |
Magnetic actuation | Paper and magnetized plate (mix Ecoflex and NdFeB) | Kresling origami | — (folded unit: ≈4.5 mm height × 20 mm diameter) | Mechanical storage | [134] |
Solvent evaporation induced deswelling | PDMS | Dome shell | ≈1.8 ms (10 mm diameter × 0.6 mm) | Soft jumper | [33] |
Moisture with different relative humidity | PEDOT: PSS | Waterbomb origami | ≈60 ms (4 cm × 4 cm × 40 μm) | Soft crawler and mechanical logic operation | [135] |
As shown in figure 10(a-i), a bistable structure can be generated by magnetic force. The bistable element consists of two magnets, and a repulsive magnetic force exists between the two magnets properly arranged. Generally, the direction of the magnetic force is always consistent with the connection between the two magnets. The repulsive force pushes the magnet further until it reaches another steady state when one magnet is fixed and the other moves. Based on the design of this magnetic structure mechanism, various multistable mechanical metamaterials with rich controllable steady states can be realized. Seyedkanani and Akbarzadeh [128] utilized the above magnetic structure mechanism to design a rotating multi-stable metamaterial (figure 10(a-ii)). Specifically, a rotating multistable unit cell is developed by circularly arranging permanent magnets and creating magnet pairs with magnetically induced negative incremental torsional stiffness. The rotating unit cell is formed by the magnet pair in series with the inclined elastic arm. 1D rotationally multistable metamaterials are formed by stacking these unit cells upon each other. The SLA-based 3D printer uses commercial resin (Grey Pro V1) to make parts (hubs, rings and molds). Silicone rubbers (Elite Double 8 and 32) are used for mold casting of elastic arms. Cylindrical Nd N52 permanent magnets (magnetic flux density 1.48 T, maximum tension ≈ 2.5 pounds) are embedded as magnetic inclusions in 3D printed wheels and rings to form rotating magnet pairs. Tan et al [129] proposed novel multistable mechanical metamaterials composed of multiple magnet systems (figure 10(a-iii)). Six different modes of multistable mechanical metamaterials design forms are proposed by changing the arrangement of magnets (relative angles). These metamaterials can be manufactured by FDM and interlocking methods and consist of bistable units and frames arranged in a regular manner. The magnets are interlocked in the frame, and every three magnets form a bistable element. The support frame of the 3D metamaterials is printed by FDM (the material is PLA). The magnet is locked on the support frame and then the support frames are assembled together.
Figure 10. Bistable/multistable structure controlled by multiple physical fields. (a) Multistable mechanical metamaterials under magnetic field control. (i) Bistable structure is generated by controlling the magnetic field. (ii) Magnetically controlled rotating multistable metamaterials are composed of magnet pairs with magnetic induction negative incremental torsional stiffness. [128] John Wiley & Sons. © 2022 Wiley‐VCH GmbH. (iii) Novel multistable mechanical metamaterials composed of multiple magnet systems. Reprinted from [129], © 2019 Elsevier Ltd. All rights reserved. (b) Gas-driven meter-scale multistable rigid deployable structure. Reproduced from [130], with permission from Springer Nature. (c) Temperature-responsive multistable mechanical metamaterials combine liquid crystal elastomer (LCE) and multistable kirigami structure (based on a rotating square mechanism). Reprinted with permission from [131]. Copyright (2021) American Chemical Society. (d) Solvent-driven jumping polymer gels based on 3D dome structure. Reproduced from [33], with permission from Springer Nature. (e) Multistable mechanical metamaterials under electric field control. (i) Dielectric elastomer actuators (DEAs) based on bistable curved beams were fabricated for grippers and binary devices. Reproduced from [132]. © IOP Publishing Ltd. All rights reserved. (ii) Dielectric elastomer (DEs) bionic three-layer bistable all-polymer laminates for soft and tunable bistable actuators. [63] John Wiley & Sons. © 2018 WILEY‐VCH Verlag GmbH & Co. KGaA, Weinheim.
Download figure:
Standard image High-resolution imageMelancon et al [130] designed the meter-scale multistable, inflatable rigid deployable structure inspired by origami (figure 10(b)). It solves the disadvantages of cumbersome assembly or poor air tightness of traditional deployable structures. To demonstrate this deployable structure, they constructed an inflatable archway with 60 cm high and 150 cm wide (initially 20 cm high and 30 cm wide) and a shelter 2.5 m × 2.6 m × 2.6 m (initially 2 m long, 1 m wide and 0.25 m high). In order to provide a robust and protective environment, adapt to geometric frustration during deployment, and minimize the bending energy in the hinge, stiff faces and compliant hinges are selected to construct an origami structure. To realize the centimeter-level arch structure, two different methods based on cardboard and 3D printing faces are used, respectively. In the first method, the cardboard is cut by laser, and then the hinge connection is formed by a double-sided adhesive sheet. This cardboard structure can be manufactured quickly and at a low cost, but it cannot provide a closed cavity. Therefore, the second method is used to realize the inflatable prototype, and the 3D printing faces of the rigid material (PLA) are connected with the flexible polyester laser cutting sheet to form a hinge. The meter-scale shelter with large size (8 ft × 4 ft, 4 mm thick), corrugated face, high bending stiffness and weight ratio is manufactured with corrugated plastic sheets. In order to form a compliant hinge, the thickness of the material is reduced locally by cutting the plastic sheet. In addition, plates were carved to further increase the flexibility of the hinges to allow for geometric frustration during deployment.
Korpas et al [131] combined a liquid crystal elastomer (LCE) with a multistable kirigami structure (based on a rotating square mechanism) to prepare temperature-responsive multistable mechanical metamaterials (figure 10(c)). The structure will be automatically reconfigured when the local temperature changes. The metamaterials consist of a square block embedded in a cylindrical magnet and a PDMS-LCE bilayer hinge connecting adjacent vertices. As the temperature increases, the shrinkage and softening of LCE cause the block to rotate. The hinge consists of two layers: a temperature-responsive LCE layer and a PDMS layer. The two parts were respectively prepared by a 3D printer based on DIW and bonded by silicone glue. The square block was prepared by molding silicone (DragonSkin 10-SLOW) in a custom 3D printing mold, and cured to leave space for the insertion of the magnet and hinge. The hinge is then placed in and glued to the square with silicone. To provide axial restraint and reduce friction, the customized inserts are 3D-printed and can be moved around the center of each square, together with the cylindrical neodymium magnets.
Kim et al [33] used a 3D dome structure to create autonomous snapping and jumping polymer gels (PDMS) (figure 10(d)). The crosslinked PDMS was swollen in n-hexane solution and then placed on a black PTFE sheet to swell. As the solvent evaporates, the material deforms into a curved geometry. During this process, some complex buckling transitions (e.g. smooth, simple bending deformation and abrupt, snap-through buckling) will occur. Based on this concept, they fabricated an axisymmetric shell structure that allows for predetermined buckling modes and maximum displacement locations. The dome shell structure is made from uniform PDMS sheets from which a circular sheet is laser-cut and a circular groove pattern is laser-carved on the central area. The circular sheet is swollen with n-hexane to a fully balanced state (i.e. a flat geometry). Then, the swollen circular sheet is dried for a certain time, and the groove is oriented to the substrate. The circular sheet deforms into a spherical shell due to the evolution of the transient deswelling strain in the thickness and radial directions during the drying process. A sequential release of stored energy is used to complete the snap-through.
Follador et al [132] designed an active, elastic, electrodynamic bistable gripper and binary device based on dielectric elastomer actuators (DEAs) (figure 10(e-i)). The pre-buckled bistable elastic thin beam is a passive element driven by two DEAs sheets. The DEAs acted as antagonists to provide actuation for switching between two equilibrium positions. The DEAs expand and drive the bistable unit to generate a snap after applying a high voltage on the DEAs. The bistable unit can be maintained at any steady state after removing the voltage. Therefore, this structure can be designed as a gripper and binary device. Shao et al [63] reported a bioinspired three-layer bistable all-polymer laminate (figure 10(e-ii)) containing dielectric elastomers (DEs) for soft and tunable bistable actuators. It comprises a stiff yet flexible elastic support layer, a pre-deformed elastomer layer and an electroactive layer. The pre-stress and lamination strategies induce tunable bistability, while the electromechanical response of the DE film enables reversible shape transition and deformation. They used disc actuators and reed unit actuators similar to Venus's flytrap leaf to demonstrate this concept. A laminated bistable actuator was fabricated by attaching two orthogonally pre-strained acrylate adhesive elastomer films (VHB-4905) as DE layers to a support layer (25 μm) of a polyimide (PI) or polyethylene terephthalate (PET) film of the same thickness and to different elastic moduli. The DE films as the top and bottom layers are pre-stretched in both directions using a stretching device. The film is kept in a stretched state until combined with the support layer. The electrodes are applied to the appropriate positions of the actuator before bonding the film. Two electrode materials were used to make the actuators, carbon grease and poly(3,4-ethylenedioxythiophene)/poly(p-styrene sulfonic acid) for the inner and outer electrodes, respectively. A carbon grease electrode is used outside the DEs layer, using a brush and a polyethylene film mask. In order to connect the electrode to the power supply, a carbon nanotube wire is used, and one end is connected to the electrode using Ag epoxy to establish a flexible lead. The pre-stretched DEs film is then uniformly pressurized together with the support layer. Finally, external constraints are removed by cutting the laminates into discs or reed units of the required size and shape.
3.5. Characteristic size
Advanced manufacturing technology has enabled the fabrication of multistable mechanical metamaterials with complex structures that span multiple length scales. Figure 11 shows various examples of multistable mechanical metamaterials that have been previously reported across multiple length scales, featuring a wide range of unit cell sizes (∼μm to ∼m). Moreover, these multistable mechanical metamaterials demonstrate varying mechanical responses, known as the 'size effect'.
Figure 11. The characteristic size of the unit cell of multistable mechanical metamaterials manufactured by different manufacturing methods. (a) Multistable microlattices based on bistable curved beams were prepared by TPP. [39] John Wiley & Sons. © 2016 WILEY‐VCH Verlag GmbH & Co. KGaA, Weinheim. (b) Micro-/nano-multistable mechanical metamaterials prepared by mechanically guided assembly of compressive buckling. (i) The micron-sized dome shell structure was prepared by equal biaxial compressive stress. Reproduced from [122], with permission from Springer Nature. (ii) Mechanically guided assembly method using compressive buckling was used to construct complex 3D micro/nanostructures from 2D micro/nanofilms. [121] John Wiley & Sons. Copyright © 2007 WILEY‐VCH Verlag GmbH & Co. KGaA, Weinheim. (c) PμSL was used to fabricate meso-scale signal elements based on curved beams. Reproduced from [35]. CC BY 4.0. (d) Multistable mechanical metamaterials prepared by macro 3D printing technology (e.g. FDM, PolyJet, SLS, DIW). (i) Double-U type multistable mechanical metamaterials were constructed by FDM. Reprinted from [92], © 2018 Elsevier Ltd. All rights reserved. (ii) Scalable tristable hierarchical mechanical metamaterials were prepared by multi-material PolyJet 3D printing. From [20]. Reprinted with permission from AAAS. (iii) Multistable Schwarz's Primitive shell structure is fabricated by SLS. [21] John Wiley & Sons. © 2021 Wiley‐VCH GmbH. (iv) Multistable mechanical metamaterials based on inclined beam were constructed by DIW. [18] John Wiley & Sons. © 2015 WILEY‐VCH Verlag GmbH & Co. KGaA, Weinheim. (e) Multistable mechanical metamaterials fabricated by mold casting and cutting. (i) A digital synthetic multi-material structure with monostable or bistable properties was prepared by mold casting. Reproduced with permission from [88]. (ii) Multistable, reprogrammable origami metamaterials are fabricated by engraving machine. [83] John Wiley & Sons. © 2022 Wiley‐VCH GmbH. (f) Gas-driven meter-scale multi-stable rigid deployable structure. Reproduced from [130], with permission from Springer Nature.
Download figure:
Standard image High-resolution imageShan et al [18] prepared 1D multistable mechanical metamaterials with volume filling fractions around 50% and with centimeter-scale lattice constants. In contrast, Frenzel et al [39] achieved lattice constants that are about two orders of magnitude smaller (micron scale) through experiments, resulting in higher characteristic vibration frequencies and faster energy absorption. Vangelatos et al [136] clarified the buckling mechanism that controls the response of 3D structures at the microscopic scale. It is found that the scale effect affects the buckling deformation of the characteristics. For low h/d (the ratio of element height to beam diameter), the instability mechanism of buckling is reduced and the internal stiffness of the structure is increased.
It can be seen that the effective strength of micro-scale materials is significantly improved compared with macro-scale materials [137]. The reason is that there are many defects in the manufacture of macroscopic materials (such as dislocations, voids, grain boundaries, cracks, etc), resulting in the actual strength of the material is far less than the theoretical strength [138]. As a result, the strength depends largely on the intrinsic size of the material [139]. The main strategy to reduce the intrinsic characteristics of the material is to reduce its overall external size [140]. As the size of the material decreases and approaches the nanoscale, the size of its inherent defects will eventually become closer to the length scale of its external characteristics [141].
These multistable mechanical metamaterials with different feature sizes require different manufacturing methods. Notably, two methods, TPP and mechanically guided assembly of compressive buckling, have the ability to fabricate structures with micron-scale feature sizes (figures 11(a), (b-i) and (b-ii)). PμSL has inferior spatial resolution compared to TPP, but can fabricate larger structures (millimeter scale), as shown in figure 11(c). Conventional 3D printing technologies, such as FDM, PolyJet, SLS, and DIW, have moderate spatial resolution, but can be used to manufacture practical large-scale structures (figures 11(d-i)–(d-iv)). Mold casting and cutting methods are suitable for manufacturing even larger structures, up to centimeters or meters in size (figures 11(e-i), (e-ii) and (f)). Although these methods are applicable for preparing multistable mechanical metamaterials, their effectiveness is restricted when compared to integrated molding techniques, like 3D printing. This is due to the complicated processing steps and low precision associated with them. As a result, these methods can only be employed in specific materials or structures or under particular circumstances.
In summary, there are lots of methods for manufacturing multistable mechanical metamaterials. At present, common methods include different AM technologies, mold casting, and cutting. Moreover, alternative techniques such as mechanically guided assembly of compressive buckling are also available. In many cases, a combination of these methods, such as 3D printing combined with mold casting, is utilized. Due to the diverse nature of multistable mechanical metamaterials, the preparation method should be evaluated based on material, structure, scale, and properties.
4. Application of multistable mechanical metamaterials
It can be seen from the above analysis that the bistable/multistable structure has excellent mechanical properties, which leads to the wide application of multistable mechanical metamaterials in many fields. Reusability, energy storage and absorption characteristics provide a new design method for realizing reusable devices and mechanical energy absorption. These structures can achieve rapid deformation and amplification of the output force, which provides an effective way for high-performance actuators and is expected to solve the problem of slow response during actuation. In addition, they can maintain the steady state after deformation without consuming additional energy, which is very beneficial for low-power grippers. The rich deformability of multistable structure provides a feasible solution for reconfigurable manipulator, multi-stage energy absorption and wave control. Therefore, in this section, we will review the research progress of multistable mechanical metamaterials from the perspective of application, such as energy absorption, soft actuator/soft robot, mechanical storage/logical operation, wave control, etc.
4.1. Actuators for soft robots
Robots with perception, decision-making and execution capabilities can assist or even replace humans to complete dangerous, heavy and complex work, and improve work efficiency and quality [142, 143], and are widely used in various fields [144–146]. However, most robots are currently made of rigid materials (e.g. metals), which cannot exhibit the inherent adaptive properties of flexible materials for more complex external obstacles due to their weak ability to deform elastically [32, 147]. In addition, rigid robots have a poor affinity for the human body and are easy to cause harm to the human body. In contrast, soft robots can safely interact and cooperate with human beings, with continuity, flexibility and adaptability, showing certain safety and elastic deformation ability, can adapt to the harsh closed environment, resist pressure and alleviate stress concentration phenomenon [142, 144]. Recently, the design of various high-performance soft actuators and robots using bistability and multistability has aroused interest in soft robots [23, 25]. Compared with the stable actuation structure, soft robots with bistable and multistable structures can make use of the snap-through of multistable structures to achieve fast response [59, 63, 148]. In addition, the conventional stable actuator needs an external continuous energy supply to keep its deformation shape, while the multistable structure can keep its deformation shape without continuous energy input to achieve the environmental protection effect.
In addition, soft robots with complex deformation modes usually require multiple hardware systems [142, 149], such as storage, valves, motors, and microcontrollers. These hardware systems reduce the degree of freedom of soft robots and limit their mobility, flexibility and adaptability [32, 146, 150]. Bistable structures have two distinct stable configurations that can be utilized to represent binary information (0 or 1) and implement logical operations (e.g. AND, OR, NOT and NAND, NOR, etc) [35, 151]. Although the hardware system based on electronic transistors and magnetic memory has advantages in computing speed and storage density, the mechanical storage and logic system based on bistability has strong robustness and are conducive to application under extreme conditions (such as high temperature and strong radiation) [151, 152]. This bistable system can be easily integrated into soft robots to improve the flexibility of soft robots, and significantly reduce the complexity of their control systems without limiting their mobility [153, 154]. The assembly of bistable units into multistable mechanical metamaterials can provide rich controllable stable states and has important applications in information processing and logical operations [34, 36, 155].
Bistable beam and truss structures are often used to make soft actuators and mechanical storage/logic because of their simple structure and fast deformation speed. Chi et al [44] proposed the design of a bistable and multistable soft flapping actuator composed of soft bending actuators and pre-bending flexible wings (figure 12(a)). The design of the actuator is inspired by the design of the hair clipper, which is formed by combining two parallel wing frame bands at the end to form a pair of bistable pre-bending flexible wings. The slightly buckled actuator can drive the wings to achieve large-scale flapping and rotational motion. On this basis, a high-speed, efficient and operable soft swimmer using bistability and multistability was developed. The lightweight, butterfly stroke–like soft swimmer (2.8 g) exhibited a record speed of 3.74 body length·s−1 (4.8 times faster than previously reported), high power efficiency, low energy consumption cost and high maneuverability.
Figure 12. Applications of multistable mechanical metamaterials to soft actuators/robots and mechanical storage/logic. (a) The design of bistable and multistable soft beat actuators composed of soft bending actuators and pre-bending flexible wings. Reproduced with permission from [44]. A high-speed, efficient and operable soft swimmer using bistable and multistable states was developed. (b) Reprogrammable mechanical metamaterials realize periodic arrays of basic logic and fully functional mechanical logic gates. Reproduced from [35]. CC BY 4.0. The application of reprogrammable mechanical metamaterials in general combinatorial logic and temporal logic (information storage) is demonstrated experimentally. (c) The tri-stable hierarchical mechanical metamaterial based on the X-shaped curved beam structure can perform ternary logic operations and amplitude modulation. From [20]. Reprinted with permission from AAAS. Basic logic operations (e.g. 'OR', 'AND', 'NOT' gate, etc) are experimentally demonstrated. (d) Flexible multistable mechanical metamaterials based on 3D dome shells, which can be used to prepare robot grippers. Reproduced from [26]. CC BY 4.0. The gripper has the functions of storing skin, storing information and calculating mechanical signals distributed in space. The dome is sunken and the grab arm remains open during deflating; the gripper can grasp during inflating. (e) The multistable Kresling origami unit is connected in series into a multi-cell structure and made into a robotic arm. Reproduced from [25]. CC BY 4.0. The robotic arm achieves universal bending, stretching and twisting movements, and can grasp and manipulate objects through magnetization design and precise magnetic field control. (f) Mechanical metamaterials based on bistable 3D dome shells with stable memory properties. Reproduced from [34], with permission from Springer Nature.
Download figure:
Standard image High-resolution imageThe logical function of mechanical metamaterials is usually determined by their layout, which is difficult to change once the design is completed. The existing mechanical metamaterials logic systems are not fully functional or cannot implement temporal logic. Therefore, they do not have strong mechanical computing ability. As a result, Mei et al [35] proposed reprogrammable mechanically mechanical metamaterials consisting of a periodic array of basic logic and a fully functional mechanical logic gate (figure 12(b)). The metamaterials can be reprogrammed under a series of continuous electromagnetic excitations. The loading position is determined by the switch state distribution of the bistable curved beam array to perform different logic functions (e.g. 'AND', 'OR', 'NOT' logic gates). The experiments demonstrate the application of reprogrammable mechanical metamaterials in general-purpose combinatorial logic and temporal logic (information storage). In addition, the information storage capacity of the system is proved to be beneficial to the compact design of mechanical logic circuits. Zhang et al [20] proposed scalable tri-stable hierarchical mechanical metamaterials for ternary logic operations and amplitude modulation, as shown in figure 12(c). The basic element is the X-shaped curved beam structure, which provides two additional steady states under the left/right movement of the connecting rod, that is, it has three steady states. The hierarchical mechanical metamaterials constructed by extending the element according to the bottom-up scheme can achieve an exponential increase in the number of steady states. They used this unique tri-stable structure to design the basic mechanical ternary logic gate, with mechanical force as input and displacement as output. Experiments demonstrate the basic logic operations (such as 'OR', 'AND', 'NOT', etc). Due to this unique tri-stable structure design, it also shows complex logic operators that could not be realized before. Compared with binary logic gates, ternary/multi-valued logic gates can process more information, effectively reduce design complexity and speed up serial arithmetic operations. The ternary logic gate also has unique applications in a fuzzy logic circuit, asynchronous circuit and so on. These mechanical logic systems can be embedded in any type of architectural material to interact mechanically with the surrounding environment. Because the system does not need electricity when processing and storing digital data internally, it is very suitable for high radiation, high temperature, high voltage and other electronic equipment is difficult to play the role of the occasion.
The bistable thin shell structure has a larger contact area, and it is advantageous to prepare it as a soft gripper for 'grasping' action. Faber et al [26] reported a series of mechanical metamaterials composed of flexible plates made up of reconfigurable bistable 3D dome arrays, as shown in figure 12(d). The robot gripper prepared by 3D printing has the functions of storing skin, storing information and calculating mechanical signals distributed in space. A simple robotic gripper was constructed for demonstration experiments. The gripper arm was kept open when the dome was depressed. The grasping arm will close tightly enough to grasp a small-weight object when a small amount of air pressure is applied to make the dome convex. The bistable structure can store energy when flipping the dome to close the gripper, so that the grip can be maintained without external energy input. In addition, flexible mechanical metamaterials also show certain potential in mechanical storage. The 3D dome bistable structure can store local elastic energy and generate multistable reconfigurable geometries. The 3D dome structure is similar to the '1' and '0' of computer data. Data is mechanically 'Read' from the shape of the flexible sheet by pressing the dome in certain positions in a certain order. The flexible sheets can be 'programmed' to perform mechanical computing without power or a central processor. Kresling origami structures are also commonly used to make soft robots due to their bistability [32, 156], torsional buckling deformation and axial contraction motion (i.e. tension–compression–torsion coupling). Wu et al [25] connected Kresling origami elements in series into a multi-cell structure, which was then made into a robotic arm, as shown in figure 12(e). This robotic arm is inspired by the flexible deformation of the octopus tentacles to achieve walking, swimming, hunting and other movements. The Kresling element can achieve stretching and universal bending deformation under the control of the external magnetic field, that is, the stretching deformation is realized when the in-plane torque is applied, and the bending deformation is realized when the out-of-plane torque is applied. Multiple Kresling elements are assembled into a multi-element bionic robot arm. The robot arm realizes universal bending, stretching and twisting movements, and can grasp and operate objects through magnetizing design and precise magnetic field control. This magnetically driven bionic robot arm has the advantages of wireless remote control, fast response and easy miniaturization. Their team also used Kresling origami to realize a millimeter robot that can simultaneously realize amphibious multimodal motion, controlled liquid drug release, and solid drug delivery [146].
The bistable thin shell structure also shows rich research results in mechanical storage and logical operation. Novelino et al [134] combined magnetic response materials with bistable Kresling origami structure to form a new type of multifunctional actuator. It can realize the independent control of multiple driving elements under the control of a single external magnetic field, and can be applied to information storage. In the demonstration experiment, the analog-to-digital conversion and information storage functions are realized. They designed a three-bit memory, which realized the change of stored information under distributed control and displayed the stored information in real time with LED. This multi-functional actuator can passively sense the size of the external load, and actively respond through magnetic drive. It integrates the functions of driving, sensing and computing, and conforms to the induction–decision–response of the robot. Although mechanical metamaterials exhibit novel mechanical properties, they cannot be changed once programmed, so they do not exhibit reprogrammability similar to digital devices (such as hard drives). Chen et al [34] overcame this challenge by using tiled mechanical metamaterials design framework. The material has stable memory properties at the element level, as shown in figure 12(f). This design includes a set of physical binary elements (m bits), similar to digital bits, and clearly describes the write and read phases. Each m-bit can be moved between the equilibrium of the bistable 3D dome shell using a magnetic drive, switching independently and reversibly between two stable states (acting as memory). Each state has a significantly different elastic mechanical response after deformation of the structure and is able to cycle reversibly until the system is reprogrammed. Encoding a set of binary instructions onto a tiled array produces significantly different mechanical properties, allowing stiffness and strength to change by order of magnitude. Flexible devices based on soft materials are being widely used, but their control systems are still rigid hard valves and electronic controls.
The continuity, flexibility and adaptability of soft robots provide new functions that traditional rigid robots cannot achieve. The advantages of introducing bistable structure into soft actuators and robots are as follows: (1) fast response. The bistable structure can perform snap-through under low driving energy and small input force to achieve fast movement and amplify the output force. In addition, rapid deformation at the millisecond level can be achieved to overcome the disadvantages of low force and slow response of soft materials. (2) Energy saving. The bistable structure does not need to provide additional energy and can maintain the deformation configuration, that is, to maintain the capture steady state. However, the traditional soft actuator needs continuous driving input to maintain deformation. (3) Rich deformation configurations. Multiple bistable units can be connected in series, parallel or mixed to form multistable structure with different configuration, so as to adapt to the reconfigurable robot and multi-modal robot in narrow space, and a reconfigurable manipulator that can bend and twist. The mechanical storage and logical operations currently implemented in bistable structures are slow and poorly miniaturized and integrated compared to electronic forms of computing and information processing. However, the bistable structure interacts with the surrounding environment, stores bit information through binary states (0, 1), does not require additional power supply, and has high energy efficiency. Therefore, mechanical storage and logical operation are very suitable for high radiation, high temperature, high pressure and other occasions where electronic equipment is difficult to play a role. In addition, the development of micro-nano manufacturing technologies (e.g. micro-nano 3D printing, lithography, etc) has promoted the development of micro-nano devices, which is conducive to the miniaturization of mechanical logic gates. With the development of soft actuators and robots, the reversible binary of bistable structure is used as soft mechanical logic gates (AND, OR, NOT). The designed mechanical logic computation and mechanical memory have potential applications in the autonomous control of soft actuators and robots. The integration of information processing, material science and robotics enhances the ability to interact with and adapt to the environment [35, 155, 157].
4.2. Energy absorption
Energy absorption plays an important role in daily life and industrial production. The absorption and dissipation of impact energy by traditional energy-absorbing structures/materials are often achieved through destructive plastic deformation or fracture [158, 159]. One of the major drawbacks of this approach is that because the process of absorbing energy is destructive, the structure/material is destroyed after a single use and cannot be reused, that is, the structure/material is not repeatable, which will lead to waste of resources and environmental pollution [160]. In addition, such structures/materials often have poor adaptability to complex environments and lack flexible deployment capabilities [161–163]. In the face of these shortcomings, researchers have adopted multistable mechanical metamaterials to address the above challenges [38, 58, 164].
The bistable structure absorbs energy from the external system when switching from a low-energy state to a high-energy state, and this process is repeatable. The bistable structure is assembled into multistable mechanical metamaterials. The bistable units of multistable mechanical metamaterials are switched to a high-energy state when they are subjected to an impact load, and the impact energy is stored in the structure in the form of elastic energy. Therefore, multistable mechanical metamaterials are often used to collect or dissipate mechanical energy [18, 21, 24, 51] (figure 13).
Figure 13. Application of multistable mechanical metamaterials in energy absorption. (a) Multistable mechanical metamaterials based on 1D inclined beam structure can be used for repeated energy absorption. [18] John Wiley & Sons. © 2015 WILEY‐VCH Verlag GmbH & Co. KGaA, Weinheim. The structure can be extended to 2D and 3D structures. The experiment demonstrates the impact protection effect of metamaterials on high-altitude objects falling. (b) Multistable micro-lattice based on bistable curved beams have been implemented for the absorption of mechanical energy at the micron scale. [39] John Wiley & Sons. © 2016 WILEY‐VCH Verlag GmbH & Co. KGaA, Weinheim. (c) Programmable multistable perforated shell for energy absorption. [21] John Wiley & Sons. © 2021 Wiley‐VCH GmbH. Low-speed impact test of toy cars to demonstrate the energy absorption of metamaterials. (d) Hedgehog-inspired mechanical pixel array (multistable mechanical metamaterials made of a 3D thin shell straw structure that can absorb energy efficiently and repeatedly). [24] John Wiley & Sons. © 2019 WILEY‐VCH Verlag GmbH & Co. KGaA, Weinheim. The demonstration experiment shows the energy absorption capacity of the metamaterial and can protect fragile objects. (e) Multistable mechanical metamaterials combined with inclined beam and snap-fit structure. [17] John Wiley & Sons. © 2017 WILEY-VCH Verlag GmbH & Co. KGaA, Weinheim. (f) Programmed granular metamaterials for repeatable energy absorption [48]. The energy absorption capacity of the metamaterial was verified by experiments. [48] John Wiley & Sons. © 2019 WILEY‐VCH Verlag GmbH & Co. KGaA, Weinheim.
Download figure:
Standard image High-resolution imageShan et al [18] earlier proposed to use multistable mechanical metamaterials to absorb impact energy, as shown in figure 13(a). The team designed multistable mechanical metamaterials that can repeatedly absorb energy using a 1D inclined beam structure. Moreover, this structure can be extended to 2D or even 3D structures. The impact protection effect of the metamaterials against falling high-altitude objects is demonstrated by experiments. This structure is simple and low-cost. However, its mechanical properties are no longer adjustable and lack of programmability once this structure is completed. In addition, this structure has low strength and limited energy absorption. In the same year, Restrepo et al [54] adopted a similar structure and proposed phase transforming cellular materials. This phase-transforming cellular materials are actually multistable mechanical metamaterials that exhibit properties similar to those of phase change materials. On the micro-nano scale, multistable mechanical metamaterials can also exhibit excellent mechanical energy absorption capacity. Frenzel et al [39] proposed multistable micro-lattices (figure 13(b)), which use bistable bending beams to achieve micrometer-scale metamaterials for absorbing mechanical energy. However, these multistable mechanical metamaterials based on bistable beam structures have low strength and lack stability in engineering applications.
The bistable thin shell structure with 3D characteristics is also commonly used for energy absorption. Shi et al [21] designed a programmable multistable perforated shellular using two perforation strategies on Schwarz's Primitive shellular (figure 13(c)). The low-speed impact test of the toy car demonstrates the energy absorption of the material, measuring the rebound distance after impact, and the perforated shell with self-contact design has the minimum rebound distance and absorbs most of the impact energy. However, the thin-shell structure lacks stability in engineering applications due to the difficulty in preparation and low strength susceptibility to damage. Inspired by hedgehogs, Pan et al [24] proposed a new mechanical pixel array design strategy. They used straws (3D thin-shell structure) to fabricate multistable mechanical metamaterials with super mechanical property programmability, complex shape reconfigurability, and efficient and repeatable energy absorption, as shown in figure 13(d). The demonstration experiment shows that these multistable mechanical metamaterials can absorb impact energy to protect fragile objects. However, due to the non-boundary constraints of these metamaterials, they are easy to splash when subjected to impact. In addition, straws are thin-walled shell structures, which are difficult to be processed and extended to micro-nano scales.
Based on the research of Bertoldi et al, Wu et al [17] designed multistable mechanical metamaterials that combine inclined beams and snap-fit structures for energy absorption (figure 13(e)). These artificial structures allow the snap-fit sequence to be inserted into the mating grooves. However, because there is no opening in the middle of the snap-fit, the snap-fit is forced to deform when subjected to an external load, increasing wear and being easily damaged. In addition, Fu et al [48] collaborated to develop programmable granular metamaterials for repeatable energy absorption (figure 13(f)). The element undergoes a steady state transition under external load, the stretchable component undergoes elastic deformation, and the rigid granular slide relative to each other. The external energy is partly stored as elastic strain energy and partly dissipated as frictional heat energy, thus achieving the purpose of energy absorption. The energy absorption capacity of the metamaterials was verified by experiments.
There is also a great demand for high-velocity impact protection in engineering field. Compared with low-velocity impact, the mechanical behaviors of structures under high-velocity impact, explosion and other strong dynamic loads are more complex. When the multistable mechanical metamaterials with macroscopical element size are subjected to these dynamic loads, their steady-state transition time is significantly longer than the response time of base materials due to the combination of the ultra-high strain rate effect of the material and the inertia effect of the structure [165–167]. In other words, the base material has undergone plastic deformation or failure before the occurrence of multistability [23]. To solve this problem, a microcosmic size of multistable element is necessary to reduce the influence of inertia effect on steady state. However, the current manufacturing technology is not sufficient enough to achieve the preparation of multi-stable metamaterials across scales, as discussed in section 3. Therefore, there are very few studies on multistable mechanical metamaterials applied to high-speed impact protection. For example, Cherkaev and Leelavanichkul [168] proposed a protective bistable structure with advanced impact resistance. The structure is composed of two parts: a 'sacrificial element' and a 'waiting element'. When the strains reach a threshold, the sacrificial elements yield and subsequently fail, while the waiting elements become active and take the load to maintain the structural integrity. However, this is only a numerical study without verification of experiment. Therefore, the study of multistable mechanical metamaterials under high-speed impact needs further exploration.
The bistable structural element will be converted from one steady state to another when subjected to an external impact load. During the conversion process, the conversion is reversible. The energy input from the outside is stored in the structure in the form of strain energy. Therefore, multistable mechanical metamaterials exhibit excellent energy absorption properties (such as reversibility and repeatability). The deformation of multistable mechanical metamaterials is dominated by elastic deformation, which solves the shortcomings of non-reusable traditional energy absorbing structures. In addition, multistable mechanical metamaterials are programmable, which can be deployed quickly and flexibly, improving their ability to use in complex environments. However, there are some disadvantages in multistable mechanical metamaterials, such as low strength, weak energy absorption and failure to recover automatically in conventional multistable structures. Therefore, the energy absorption capacity can be improved by optimizing structure design, using high energy density materials, combining with traditional energy absorption structure, and introducing a multi-stage energy absorption structure. By adding a recoverable mechanism to the multistable structure and adding a response external stimulus material, multistable mechanical metamaterials can be designed to provide more different types of unusual physical properties. For example, a bistable structure with shape memory material is designed, and the trigger temperature is adjusted by changing the design parameters. The thermal bistable structure will recover its shape when heated to the trigger temperature [114].
4.3. Wave control
Multistable systems usually respond to external stimuli by releasing energy in a sequential manner through a continuous internal transition process from one steady state to another [169, 170] (figure 14). In other words, in the initial high-energy state of the bistable structure, the input signal pushes the first steady state back to the low-energy state, the released energy pushes the next steady-state element to the low-energy state. Finally, the stable nonlinear transmission wave propagates in the multistable system with high fidelity and controllability. This system is internally interrelated, similar to the 'domino effect', a small initial energy can produce a series of chain reactions.
Figure 14. Application of multistable mechanical metamaterials in wave control. (a) A multistable system with a magnet can propagate unidirectional transition waves. Reprinted figure with permission from [171], Copyright (2016) by the American Physical Society. (b) A flexible medium based on a bistable Von Mises truss structure can steadily propagate mechanical signals. Reproduced with permission from [37]. (c) Transient wave propagation of bistable 3D dome shell array in a sealed fluid cavity. Reproduced from [40]. CC BY 4.0. (d) Transition waves in mechanical metamaterials composed of tri-stable element chains. Reprinted figure with permission from [170], Copyright (2020) by the American Physical Society. (e) 2D multistable mechanical metamaterials can achieve predictable and programmable motion by adjusting the propagation of transition waves in their architectures. Reproduced with permission from [41].
Download figure:
Standard image High-resolution imageThe bistable curved beam and truss structures are the earliest examples used to study wave control. Nadkarni et al [171] designed a set of multistable systems composed of bistable units with a pair of magnets at the center that can propagate unidirectional transition waves (figure 14(a)). The bistable units in the array suffer repulsive forces from magnets in their adjacent elements. Therefore, it triggers the sequential switching of the remaining bistable units in the array when one of the bistable units switches states, generating 1D transition waves. Raney et al [37] used a flexible medium prepared by a bistable Von Mises truss structure to stably propagate mechanical signals (figure 14(b)). The bistable buckling beam which can produce large deformation is prepared by using flexible material, and the energy is released under the stimulation of traveling wave front, so that the large amplitude signal can achieve the effect of lossless propagation without external excitation. The energy absorption and release of the balance of the structure leads to stable wave propagation, which is characterized by the high fidelity, predictability and controllability due to the inherent dissipation of the material. They also studied the transition wave propagation of a bistable 3D dome-shell array in a sealed fluid cavity [40], as shown in figure 14(c). Because the fluid cavity between two bistable dome shells will maintain a constant volume, the snap-through process of the bistable dome shell will propagate to its adjacent shell. The energy dissipation during propagation affects the propagation distance. In order to extend the propagation distance, the team adjusts the energy barrier by changing the thickness of the shell to allow the transition wave to propagate in both directions at a limited distance.
In addition, some kirigami structures (e.g. rotary hinge deployable kirigami structure) are also commonly used to control the propagation of waves. Yasuda et al [170] studied the transition waves in mechanical metamaterials composed of tri-stable element chains by experimental, numerical and analytical methods (figure 14(d)). The transition wave can be initiated from different stable phases in a highly adjustable tri-stable energy range. These waves propagate through coupled translational and rotational motions. Jin et al [41] have proposed 2D multistable mechanical metamaterials that can achieve predictable and programmable motion by adjusting the propagation of transition waves in their architectures (figure 14(e)). Initially, in a stretched (ON) state, the element of the long array is disturbed at one end to induce a local transition of the metamaterials into a compressed (OFF) state, thereby triggering a transition wave to propagate through the material in a constant manner. The transition wave propagation can be programmed to produce serpentine motion and functional shape deformation by introducing defects into the structure of these mechanical metamaterials.
Since multistable systems can generate interrelated state transitions, energy is released in sequence under external excitation. The bistable structure switching between two states can be used for transition wave propagation in the system. The velocity and direction of this transition wave can be programmed by using mechanical instability in multistable systems, thereby increasing the design range of mechanical metamaterials [172–174]. The design of programmable soft robot motion, adjustable energy absorption, and mechanical logic devices such as switches or filters can also be achieved using transition wave control across multistable systems.
4.4. Other application
Multistable structures exhibit rich mechanical properties. In addition to the above fields, they have applications in many fields, such as reconfigurable structures/devices, shock absorbers, deployable structures/devices, and material constitutive simulators.
The structure is fixed and cannot be reconstructed once the traditional metamaterials are prepared. Due to the shape deformation ability of the multistable structure and the complex spatial configuration, it can be applied to reconfigurable devices (such as reconfigurable antennas, reconfigurable resonators, etc) [70, 180]. The elements of reconfigurable antenna array are flexible and variable according to the actual situation, and the performance of antenna can be reconfigurable by adjusting the variable devices. Zhang et al [175] designed a new set of elastic joints with a specific range of motion, and designed a new triple-stable element and a series of programmable multistable metastructures based on kirigami structure (figure 15(a)). The tristable element is applied to the design of frequency reconfigurable antenna to realize 5G three-band communication.
Figure 15. Application of multistable mechanical metamaterials in other aspects. (a) A novel elastic joint with a specific range of motion is used in a kirigami structure to design a novel tristable unit and a series of programmable multistable metastructures, which can be used in the design of frequency reconfigurable antennas to realize 5G three-band communication. Reproduced from [175]. CC BY 4.0. (b) Tunable aerodynamic negative stiffness (monostable and multi-stable) mechanical metamaterials based on 3D domed shell structure with vibration isolation properties. Reprinted from [176], © 2020 Elsevier Ltd. All rights reserved. (c) Multistable mechanical metamaterials for nanoscale damping. Reprinted from [177], © 2020 Elsevier Ltd. All rights reserved. (d) A checkerboard structure (programmable phononic crystals) consisting of multistable units, each of which has different modes and acoustic characteristics and can be individually encoded. Reproduced from [178]. CC BY 4.0. (e) The combination of gas, liquid and multistable elastic capsules is used to create an artificial fluid with multiple stable states. Reproduced from [179]. CC BY 4.0. (f) Mechanically guided assembly of 3D structures for biointegrated electronic and optoelectronic devices. Reproduced from [122], with permission from Springer Nature. The 2D film pattern is transformed into the target 3D structure by the action of compression force, and the reversible switching of 3D structure between different configurations is achieved by changing the path of compression deformation (multistability). (g) A 'stair-building' strategy based on bistable structures is proposed to customize and re-customize the target mechanical behavior of mechanical metamaterials. [29] John Wiley & Sons. © 2021 Wiley‐VCH GmbH. (h) A deployable, multistable rigid wall structure. Reproduced from [130], with permission from Springer Nature. The origami units are combined to achieve a macro-scale (meter level) functional structure (e.g. arches and emergency shelters, etc).
Download figure:
Standard image High-resolution imageThe local instability in the multistable structure occurs under the predetermined force. The lower energy is used to enter the new steady-state configuration when the multistable structure is converted, which can prevent the transmission of the critical force and consume energy. Based on this principle, the bistable structure can be applied to vibration isolation. Tan et al [176] proposed mechanical metamaterials with real-time adjustable aerodynamic negative stiffness (both monostable and multistable), as shown in figure 15(b). The basic element of the metamaterials is 3D dome shell structure, which can achieve multi-level mode conversion through pneumatic drive and has vibration isolation performance. Inspired by the protein structure, Benichou and Givli [177] used carefully designed multistable mechanical metamaterials as nano-scale shock absorbers, as shown in figure 15(c). The 'target' is mechanically protected by using structural instability to repeatedly filter out forces that exceed the allowable level (e.g. forces from a vibration environment).
Inspired by the pixel encoding of the display, Yang et al [178] designed a chessboard structure composed of many units (figure 15(d)). Each unit has multistable characteristics and can change its state independently. The chessboard structure unit has different modes and acoustic characteristics, and selects some interesting characteristics and corresponding coding methods, such as filtering, waveguide, lens and invisibility characteristics.
Peretz et al [179] combine gas, liquid and multi-stable elastic capsules to create an artificial fluid with multiple stable states, as shown in figure 15(e). Bistability is achieved by switching between the unfolding and folding states through the inversion of a truncated body, which produces significant volume changes. The elastic multiple stability of the capsule gives the fluid multiple stable thermodynamic properties, including the ability to capture and store energy under standard atmospheric conditions.
The mechanical guided assembly method of 3D structure proposed by Fu et al [122] has attracted more and more attention due to its wide application in bio-integrated electronic and optoelectronic devices. In this method, the 2D film pattern is transformed into a target 3D structure by the action of a compressive force, and the reversible switching of the 3D structure between different configurations (i.e. multistability) is achieved by changing the path of compressive deformation, as shown in figure 15(f).
The mechanical properties of traditional materials cannot be customized because of the structural topology and complex coupling. Based on the bistable structure, Lin et al [29] proposed a novel 'Stair-Building' strategy for customizing and re-customizing the target mechanical behavior of mechanical metamaterials (figure 15(g)). Similar to building a staircase with bricks, the target stress–strain (force–displacement) curves of the materials are customized or re-customized by visually stacking bistable units to achieve a brick-like loading curve.
Deployable systems can compress large structures into small volumes. Common methods include mechanisms consisting of interconnected rod units that can expand and contract simultaneously, and sometimes the structure is locked by bistable units. Melancon et al [130] designed a deployable, multistable deployable rigid wall structure. A deployable bistable origami library with a single fluid pressure input was constructed by geometric analysis and experiments. These units are then combined to further implement functional structures at the macro scale (meter level), such as arches and emergency shelters, as shown in figure 15(h). These systems are locked in place after deployment and provide a robust shell through their hard surfaces.
Multistable structures significantly broaden the application area of mechanical metamaterials due to their rich mechanical properties. The rich and repeatable deformability of multistable structures is utilized to demonstrate advantages in the preparation of reconfigurable devices (e.g. reconfigurable antennas and resonators). The multi-stable structure can prevent the transmission of critical force and consume energy during state switching, so it also plays a role in vibration isolation. Rich acoustic performance can be demonstrated by encoding different acoustic characteristics onto bistable structures. The multistable structure is designed as a deployable system, which plays a locking role in folding and deployable, and is used to design functional buildings at macro-scale. In addition, the bistable structure can be used to construct the target stress–strain curve.
5. Conclusion and prospect
This paper reviewed the research progress of multistable mechanical metamaterials in the past decade. We analyzed the stable and unstable points of the bistable structure in the state transition process from the perspective of energy, as well as the storage and release of energy. The categories of bistable structures based on basic element types are summarized, including (1) beam, truss and compliant mechanisms; (2) curved surface and thin shell structure; (3) other structures, such as kirigami, snap-fit structure, etc. Meanwhile, we summarized the bistability criteria of these structures. With the development of advanced manufacture technologies (e.g. 3D/4D printing), the complex multistable mechanical metamaterials can be prepared. Multistable mechanical metamaterials have been widely used in many fields (e.g. energy absorption, soft actuator/robot, mechanical storage/logic operation, wave control) due to their reusable, energy absorption, fast deformation and amplification of output force, energy saving and rich deformation ability. Although significant progress has been made in the research of multistable mechanical metamaterials, there are still many challenges in the design, manufacture and application process.
From the manufacturing perspective, the rapid development of advanced manufacturing technologies, particularly 3D printing technology, has made it possible to manufacture multistable mechanical metamaterials with various scales and complex features that cannot be produced using traditional casting or molding methods [74, 105]. However, at present, 3D printing still has the problem of high manufacturing costs and low efficiency, which may be solved by combining it with conventional techniques as certain conventional techniques like mold casting and laser cutting have inherent merits over AM in the fabrication of multistable mechanical metamaterials with particular structures or materials [175].
In addition, some new manufacturing technologies will also bring new opportunities for the preparation and application of multistable mechanical metamaterials. For example, micro-nano scale 3D printing technologies such as PμSL and TPP have been instrumental in the production of multistable mechanical metamaterials with microscopic units [27, 105]. The use of materials with excellent mechanical properties, advanced AM and post-processing technologies not only improves the performance of printed structures (especially mechanical properties, such as strength, toughness, etc), but also broadens the application fields of multistable mechanical metamaterials (such as aerospace, biomedical, electronic devices, actuator/robotic technology, etc). Multistable mechanical metamaterials can also be produced using soft-driven materials or 4D printing technology [111, 181], where they can be controlled under different physical fields like electricity, light, temperature, pH, solvent, moisture, and magnetic fields. These deformed multistable mechanical metamaterials can regain their original form when subjected to outside stimulus after undergoing deformation. Some feasible schemes (e.g. commercial AM simulation software, combination of AI and 3D printing, material–structure–performance integrated AM, etc) also provide excellent platforms for intelligent design, defect detection and parameter control of multistable mechanical metamaterials [117, 120]. Furthermore, traditional metamaterials design is generally a time-consuming process and the conventional design method is plagued by strong randomness, leading to dubious efficiency and unreliable outcomes. Recently, there has been great interest in the utilization of AI-assisted generative design, modeling, and topology optimization [182, 183]. Therefore, the combination of traditional design/simulation method and AI can realize the automatic design of multistable mechanical metamaterials [184] through simplifying the designing of optimized components with basic parameters. Consequently, the design efficiency can be substantially enhanced.
From the application perspective, multistable mechanical metamaterials typically possess low overall strength and lack self-recovery ability, which restricts their reusable range. At the same time, their energy absorption capacity is weaker compared to traditional energy absorbing materials, thereby limiting their application in high-energy scenarios. To overcome these drawbacks, one could optimize structural design, use materials with high energy density, combine with traditional energy absorption structures, or introduce multi-stage energy absorption structures. Meanwhile, due to the combination of the strain rate effect of the material and the inertial effect of the structure, multistable mechanical metamaterials with a macroscopic unit size are prone to fail before the state transition under high-speed impact. It is necessary to use micro-sized multistable elements to reduce the influence of inertial effects on the stable state.
Another application challenge is to achieve precise and quick control of the deformation of multistable mechanical metamaterials [114]. For instance, the active deformation provides a fast-driving method for soft actuator/robot, but the snap-through instability during steady-state conversion poses a challenge to precise control of the soft actuator/robot. The deformation of multistable structures is often carried out under single drive, which makes the structural control complicated. One solution is to adjust the energy barrier of the bistable unit or apply external constraints to control the deformation of the interconnection element under single drive [28]. In addition, multistable mechanical metamaterials based mechanical storage and logic operations are suitable in extreme environments, such as high radiation, high temperature, and high pressure. Meanwhile, combining mechanical computing with soft actuators/robots allows for autonomous control, enhancing their ability to interact with and adapt to the environment [37, 185, 186].
The special properties of multistable mechanical metamaterials also make them of great significance in interdisciplinary applications. Due to the interrelation among multistable systems, a relatively small amount of energy input can trigger a series of sequential energy releases in response to external stimuli [185]. Therefore, the bistable structures can control the propagation of transition waves in the system by exploiting the snap through instability of the multistable structure, thus regulating their velocity and direction [37]. By applying this feature, the multistable structure enables the development of programmable soft robot motion, tunable energy absorption, and mechanical logic device designs, such as switches or filters. Moreover, with the advantages such as steady-state conversion, repeatable deformability and self-locking, multistable metamaterials also find applications in the field of reconfigurable devices [175], vibration isolation [187], acoustic modulation [178] and even deployable functional buildings [130].
In the past decade, scientists have shown great enthusiasm for the research of multistable mechanical metamaterials, and have achieved remarkable results. We believe that the continuous improvement of multistable mechanical metamaterials theory and manufacturing technology will greatly promote their application in more engineering fields.
Acknowledgments
This work was supported by the National Natural Science Foundation of China (Grant Nos. 12172164, 52250363), the National Key R&D Program of China (Grant Nos. 2021YFB3801800, 2018YFA0306200).
Conflict of interests
The authors declare that they have no known competing financial interests or personal relationships that could have appeared to influence the work reported in this paper.