Abstract
A traceable humidity generator for temperatures up to 180 °C and pressures up to 600 kPa was realized using simple techniques and with a chamber of a considerable volume (approximately 40 l). A relative humidity setup, used for calibrating sensors at temperatures up to 180 °C and dew-point temperatures up to 95 °C, was modified to allow for the generation of dew-point temperatures up to 150 °C, thus extending the maximum relative humidity at 180 °C from 8%rh to 45%rh. The uncertainty in the generated relative humidity remained 0.2%rh at 5%rh and increases to 0.4%rh at 95%rh.
Seven industrial sensors of two different types and manufacturer (one capacitive sensor and one acoustic sensor) were tested in the setup. For both types the tests were used to obtain information about the behaviour of the sensors at high air and dew-point temperatures and high pressures. The capacitive sensors were tested up to 180 °C for determining their temperature and relative humidity correction function and the acoustic sensors were tested up to 120 °C for investigating the speed of sound.
Export citation and abstract BibTeX RIS

Original content from this work may be used under the terms of the Creative Commons Attribution 3.0 licence. Any further distribution of this work must maintain attribution to the author(s) and the title of the work, journal citation and DOI.
Introduction
Temperature- and humidity-controlled commercial climatic test chambers (CTC) are available on the market from many manufacturers. The ranges of environmental parameters (temperature, pressure and relative humidity) made available by such commercial chambers are those required by the tests for which the chambers are meant to be used: tests on the effects of specified environmental conditions on biological items, industrial products, materials and electronic devices and components. As a consequence, commercial climatic chambers typically offer a wide range of controlled temperatures (−70 °C to 200 °C) and relative humidity (10%rh to 98%rh), but simultaneous control of temperature and relative humidity is usually confined to a limited temperature range (10 °C to 95 °C). Moreover, their use is limited to atmospheric pressure, though some models for high-altitude temperature testing allows one to control pressure down to 30 kPa.
In many industrial processes (drying/baking in food processing [1], drug manufacturing in the pharmaceutical industry [2], paper drying [3] and wood drying [4]) humidity measurement and control are required at temperatures significantly above 100 °C. In such industrial processes, humidity is measured with humidity sensors available on the market. These humidity sensors are typically calibrated up to 100 °C, because traceable standards for relative humidity above 100 °C are not widely developed (to our knowledge, only one standard humidity generator for temperatures above 100 °C exists [5]). Consequently, the humidity measurements performed in industrial processes at temperatures above 100 °C are mostly not SI-traceable.
At the turn of the century the temperature department of the Van Swinden Laboratory (VSL) began increasing calibration capabilities in the field of humidity. Initially a home-built dew-point temperature generator in the range from −60 °C up to 70 °C [6, 7] was realized, followed by the purchase of a commercial climatic chamber, a Thunder Scientific 2500, for relative humidity calibrations in the range from −10 °C up to 70 °C and 10%rh up to 95%rh [8]. The traceability for the climatic chamber was obtained via chilled mirror hygrometers (CMH) calibrated in-house against the developed dew-point generator [9] and a set of calibrated glass-encapsulated thermistors.
In 2010 the temperature range of the relative humidity calibrations was extended down to −40 °C and up to 180 °C using a Hereaus HC4033 climatic chamber, but only in the range from 10 °C up to 90 °C the chamber was able to generate relative humidity. In 2011, based on customer demand, an internal project started to further extend the relative humidity range and the pressure range. A pressure sub-chamber, enclosed in the Hereaus HC4033, was designed for temperatures up to 180 °C and pressures up to 600 kPa. The facility was validated in 2012 and an EA-accreditation was obtained in 2013 for relative humidity at atmospheric pressure over the whole temperature range −40 °C to 180 °C and dew-point temperatures up to 95 °C [10].
In 2015 an EMPIR (European Metrology Programme for Innovation in Research) project was started (HIT: Metrology for Humidity at High Temperatures and Transient Conditions [11]) with the goal of providing traceability to relative humidity measurements at temperatures (and dew-points) above 100 °C. This paper reports on the VSL contribution to this project. The VSL relative humidity calibration facility was extended to allow calibrations of relative humidity sensors for temperatures up to 180 °C, dew-points up to 150 °C and pressures up to 600 kPa. In this paper we also report on the tests on a total of seven instruments of different types from two manufacturers; one type was a capacitive sensor and the second type was an acoustic sensor.
Design of the setup
The climatic chamber used in the high temperature relative humidity facility has only a standard relative humidity range up to 90 °C (see figure 1). For extension of the relative humidity range the choice was made to construct a special chamber inside the cabinet of the CTC and to pre-condition the gas outside the CTC.
Figure 1. The standard temperature and relative humidity range of the climatic chamber (thick line), the relative humidity extension realized in 2013 at atmospheric pressure (black dash line) and the range extension up to td = 150 °C and p = 600 kPa (dotted line).
Download figure:
Standard image High-resolution imageAt a dew-point temperature of 150 °C the saturation vapour pressure is nearly 500 kPa and for the realization of such a high humidity a special pressure chamber was designed, capable to withstand pressures up to 600 kPa. The pressure chamber was constructed in aluminium to limit the weight and coated with nickel to avoid corrosion [10].
To condition the gas, an external saturator was constructed, consisting of two containers, each with a water column of approximately 50 cm and a total volume of 5 litres. The saturator was immersed in a calibration bath (see figure 2). With the bath filled with water, the achievable temperature range was between 10 °C and 95 °C. A flow mixing principle was adopted to generate fast changing relative humidities. A stream of dry gas, generated using a mass flow controller (MFC) and a heat-exchanger in the bath, is mixed with wet gas from its corresponding MFC and the saturator. After mixing, the gas is fed through a heated tube to an additional heat-exchanger in the cabinet of the CTC and then in the pressure chamber, were sensors can be tested. The gas exits the cabinet via an exhaust tube and is let to a valve used to control the pressure in the test chamber. The tubes between the cabinet and the valve and part of the tubes after the valve are heated to prevent condensation. For operations below atmospheric pressure, a pump can be connected downstream of the control valve. The pump limits the dew-point temperature to approximately 30 °C.
Figure 2. A sketch of the high temperature relative humidity setup.
Download figure:
Standard image High-resolution imageThe flow mixing also made it possible to generate dew-point temperatures well below 10 °C, with as only restriction the dew-point temperature of the supply gas. The use of dry nitrogen from a liquid nitrogen storage tank sets the lowest achievable dew-point temperature well below −64 °C.
With the liquid bath filled with water, the maximum dew-point temperature was 95 °C. For generating higher dew-point temperatures an attempt was made to inject water in a dry gas stream as used in another setup [5]. Tests were performed to investigate whether it was possible to integrate water injection within the limited space of the CTC cabinet. The tests showed that such a simple solution was not possible without mayor rebuild of the setup or loss of performance (such as increased non-uniformity). A simple alternative was found in changing the water in the saturator bath with a mineral oil, thus extending the upper dew-point temperature limit from 95 °C to 150 °C.
The temperature and the temperature uniformity in the pressure chamber are measured using a glass-encapsulated thermistor, Yellow Spings Inc. (YSI), type 55016 [10, 12]. To minimize the self-heating effect the resistance is calibrated and measured using the low power option of the Agilent 34420A. The dew-point temperature is measured after the pressure control valve using a MBW 373 HX in the dew-point temperature range −35 °C up to 95 °C and a MBW 973 or MBW 373 LX below −35 °C. The dew-point temperature can also be measured up to 120 °C in the pressure chamber (and at pressure) with a Michell Instruments Optidew HT. Dew-point temperatures above 95 °C are normally only generated at an elevated pressure and the dew-points of the expanded gas after the control valve are then in the operation range of the MBW 373 HX (see table 1).
Table 1. The dew-point temperature, td, and saturation vapour pressure, es, indicating the minimum pressure of operation. The third column shows the chamber pressure, p95, at which the dew-point temperature of the expanded gas is still in the operating range of the MBW 373 HX and column four and five show practical pressures, p, and the dew-point temperature of the expanded gas, td @ 101.3 kPa.
td/°C | es/kPa | p95/kPa | p/kPa | td @ 101.3 kPa/kPa |
---|---|---|---|---|
100 | 101.4 | 121 | 150 | 89.4 |
110 | 143.4 | 171 | 200 | 90.7 |
120 | 198.7 | 238 | 250 | 93.7 |
130 | 270.3 | 325 | 350 | 93.0 |
140 | 361.5 | 435 | 450 | 94.1 |
150 | 476.2 | 575 | 600 | 93.8 |
Figure 3 shows an overview of the actual setup with the pressure chamber in the CTC cabinet and the saturator containers in the oil bath. The pictures show the MFC's for the dry and wet gas control and for the automatic refill of the saturator and the valve for the pressure control in the exit of the pressure chamber. The three water storage tanks contain approximately 11 liters of water which allow for the operation of the setup at 150 °C and 95%rh for 24 h.
Figure 3. Overview of the high temperature relative humidity facility. Clockwise the pressure chamber with industrial sensor mounted in the door, the saturator in the calibration bath, the pressure control valve, storage tanks for automatic refill of the saturator and the mass flow controllers for the dry and wet gas flow (right three in picture) and the refill of the saturator (left in picture).
Download figure:
Standard image High-resolution imageValidation of the setup
The validation of the generated temperature and the calibration and drift of the thermistors were already reported [10, 12] but, after extending the setup to over atmospheric pressures and higher dew-point temperatures, additional validation measurements were performed. Figure 4 shows the six thermistors in the test chamber and the results of the additional uniformity measurements that were used for the 2017 EA-accreditation. The uniformity is improved, compared to 2013, mainly due to the use of a new saturator.
Figure 4. The six thermistors used to measure the temperature and temperature uniformity in the chamber (left). The graph on the right shows the uncertainty contribution to the uniformity obtained during the validation in 2017 and used for the CMC calculations.
Download figure:
Standard image High-resolution imageAs the bare thermistors are now used also at elevated pressures, an investigation was performed to find their pressure sensitivity. Two thermistors were enclosed in a ¼ inch brass end cap, connected to a 50 cm stainless steel tube and submerged in a water bath (see figure 5). At the top end a pressure tight connector enabled the measurements of the sensor resistance at different temperatures and pressures up to 1 MPa using compressed air. Figure 6 shows the results of the investigation in a water bath with millikelvin stability [13] in the temperature range from 25 °C up to 75 °C and pressures between atmospheric and 1 MPa. Although there is some scatter on the results, the overall pressure effect is less than 1 µK · kPa−1 and therefore an uncertainty contribution of only 1 mK is assumed in the uncertainty budget.
Figure 5. The test tubes for the pressure test on the YSI, 55016, glass-encapsulated thermistors. The tubes were pressurized with compressed air up to 1 MPa. The inset shows the bare sensor. The leak-tight tubes were submerged in a water bath.
Download figure:
Standard image High-resolution imageFigure 6. The results of the pressure sensitivity test of two YSI, 55016, glass-encapsulated sensor over the pressure range 100 kPa to 1 MPa and the temperature range from 25 °C to 75 °C.
Download figure:
Standard image High-resolution imageThe estimation of the dew-point temperature gradients in the test chamber up to 95 °C has been reported in a previous paper [10]. As for the temperature uniformity, additional validation measurements were performed. The dew-point temperature gradient measurements were performed using two MBW 373 HX chilled mirror hygrometers (CMH) measuring the expanded gas sampled from two different positions: the chamber centre and the gas outlet of the chamber. Both instruments had been previously calibrated using the high temperature dew-point temperature generator [9]. The measured gradients, shown in figure 7, were within ±0.05 °C up to 120 °C, but appear to increase above 120 °C. The gradients are over the whole range within the combined calibration uncertainty of both CMH's.
Figure 7. The results of the gradient measurements at three chamber pressures. The dashed line is the combined expanded calibration uncertainty of the two CMH's at 100 kPa and the dotted line is the uncertainty transformed to 550 kPa.
Download figure:
Standard image High-resolution imageAs the reference dew-point temperature is measured after the expansion of the gas and needs to be converted back using the test chamber pressure and the CMH head pressure, the pressure stability is influencing the dew-point temperature. The pressure control and pressure measurement are performed with two independent instruments, which are connected to the pressure chamber using a ⅛ inch sample line. Figure 8 shows the measurements at 250 kPa and 550 kPa with details at the 80 °C and 95%rh setpoint. Table 2 shows the effect of the pressure (in)stability on the dew-point temperature and the relative humidity.
Figure 8. The pressure stability at 250 kPa (top) and 550 kPa (bottom) and the effect on the stability of the calculated reference dew-point temperature at nominal 80 °C and 95%rh (left).
Download figure:
Standard image High-resolution imageTable 2. The stability in temperature, dew-point temperature, pressure and relative humidity at nominal 80 °C and 95%rh at 250 kPa and 550 kPa. The table shows the average and standard deviation.
Time period | p/kPa | tair/°C | td/°C | h/%rh |
---|---|---|---|---|
06:30–07:20 | 249.3 ± 0.3 | 79.980 ± 0.008 | 78.28 ± 003 | 93.3 ± 0.1 |
04:45–05:40 | 548.7 ± 0.5 | 80.081 ± 0.003 | 78.10 ± 0.02 | 92.2 ± 0.1 |
Based on the validation tests described above, a complete uncertainty budget for the setup at elevated pressure is performed (see table 3 for the air temperature and table 4 for the relative humidity at elevated pressure of 600 kPa). The uncertainty contributions for the air temperature uncertainty budget remained the same as that reported in 2013 [10], with exception of the reduced uniformity contribution and the contribution for the pressure effect of the thermistors.
Table 3. Uncertainty budget for air temperature calibration in the setup in the range from 40 °C to 180 °C.
Temperature/°C | 40 | 70 | 100 | 125 | 180 |
---|---|---|---|---|---|
Uncertainty source | ui/°C | ||||
tair—Repeatability | 0.0100 | 0.0100 | 0.0100 | 0.0100 | 0.0100 |
tair—Calibration | 0.0100 | 0.0100 | 0.0100 | 0.0100 | 0.0100 |
tair—Digital multimeter | −0.0001 | −0.0004 | −0.0001 | −0.0003 | −0.0006 |
tair—Homogeneity | 0.0080 | 0.0213 | 0.0346 | 0.0456 | 0.0567 |
System | |||||
Radiation effect | 0.0173 | 0.0173 | 0.0173 | 0.0173 | 0.0173 |
Heat conduction thermistor cable | 0.0023 | 0.0023 | 0.0023 | 0.0023 | 0.0023 |
Pressure effect on thermistor | 0.0010 | 0.0010 | 0.0010 | 0.0100 | 0.0010 |
Self-heat thermistor | 0.0100 | 0.0100 | 0.0100 | 0.0100 | 0.0100 |
UUT—Resolution | 0.0029 | 0.0029 | 0.0029 | 0.0029 | 0.0029 |
UUT—Repeatability | 0.01 | 0.01 | 0.01 | 0.01 | 0.01 |
UUT—Fit | 0.03 | 0.03 | 0.03 | 0.03 | 0.03 |
UUT—Flow dependence | 0.01 | 0.01 | 0.01 | 0.01 | 0.01 |
UUT—Hysteresis | 0.01 | 0.01 | 0.01 | 0.01 | 0.01 |
Combined uncertainty (k = 1) | 0.04 | 0.05 | 0.06 | 0.06 | 0.07 |
Expanded uncertainty (k = 2) | 0.09 | 0.10 | 0.11 | 0.13 | 0.14 |
tair = air temperature, UUT = unit under test.
Table 4. Uncertainty budget for relative humidity calibration in the new setup in the range from 100 °C to 180 °C at 600 kPa.
Temperature/°C | 100 | 100 | 125 | 150 | 180 |
Relative humidity/%rh | 5 | 97 | 97 | 90 | 45 |
Chamber pressure/kPa | 600 | 600 | 600 | 600 | 600 |
Dew-point temperature at p/°C | 7.2 | 99.2 | 124.0 | 146.0 | 147.6 |
Dew-point temperature at p0/°C | −14.4 | 56.4 | 75.0 | 91.0 | 92.1 |
Uncertainty source | ui/%rh | ||||
Chamber pressure | 0.0000 | 0.0000 | 0.0000 | −0.0004 | 0.0015 |
CMH head pressure | 0.0007 | 0.0733 | 0.0688 | 0.0624 | 0.0309 |
td—Repeatability | 0.0005 | 0.0265 | 0.0221 | 0.0170 | 0.0084 |
td—Calibration | 0.0013 | 0.0663 | 0.1106 | 0.0852 | 0.0422 |
td—DMM | 0.0003 | 0.0345 | 0.0289 | 0.0224 | 0.0111 |
tair—Repeatability | −0.0018 | −0.1735 | −0.1485 | −0.1165 | −0.0515 |
tair—Calibration | −0.0004 | −0.0347 | −0.0297 | −0.0233 | −0.0103 |
tair—Digital multimeter | 0.0000 | 0.0004 | 0.0008 | 0.0014 | 0.0005 |
tair—Homogeneity | −0.0012 | −0.1200 | −0.1356 | −0.1321 | −0.0721 |
System | |||||
Radiation effect | −0.0006 | −0.0601 | −0.0514 | −0.0404 | −0.0178 |
Heat conduction thermistor cable | −0.0001 | −0.0080 | −0.0069 | −0.0054 | −0.0024 |
Self-heat thermistor | −0.0004 | −0.0347 | −0.0297 | −0.0233 | −0.0103 |
Pressure effect on thermistor | −0.0001 | −0.0050 | −0.0043 | −0.0034 | −0.0015 |
Water vapour homogeneity | 0.0034 | 0.2094 | 0.1794 | 0.1440 | 0.0714 |
Formula | 0.0007 | 0.0380 | 0.0310 | 0.0150 | 0.0073 |
UUT—Resolution | 0.0029 | 0.0029 | 0.0029 | 0.0029 | 0.0029 |
UUT—Repeatability | 0.10 | 0.10 | 0.10 | 0.10 | 0.10 |
UUT—Fit | 0.10 | 0.10 | 0.10 | 0.10 | 0.10 |
UUT—Flow dependence | 0.03 | 0.03 | 0.03 | 0.03 | 0.03 |
UUT—Hysteresis | 0.14 | 0.14 | 0.14 | 0.14 | 0.14 |
Combined uncertainty (k = 1) | 0.20 | 0.39 | 0.37 | 0.33 | 0.24 |
Expanded uncertainty (k = 2) | 0.41 | 0.77 | 0.74 | 0.66 | 0.48 |
p = chamber pressure, p0 = atmospheric pressure, td = dew-point temperature, tair = air temperature, UUT = unit under test.
Sensor testing
As part of the project EMPIR HIT industrial sensors of two different types and manufacturer were tested in the newly built setup. The first sensor type was an impedance sensor from Michell Benelux and in total five instruments were tested up to 180 °C and 550 kPa. The data were used to determine the correction coefficients at high temperatures. Figure 9 shows three of the sensors mounted in the door of the pressure chamber and figure 10 shows the performance of one of the sensors at the temperature and pressure extremes: 180 °C and 550 kPa. The deviation and hysteresis for three sensors is given in figure 11; for all three sensors the deviation is less than 5%rh (using a correction function only valid up to 80 °C) and the hysteresis is less than 0.5%rh.
Figure 9. Three Michell Benelux impedance sensors mounted in the door of the pressure chamber.
Download figure:
Standard image High-resolution imageFigure 10. The test of Michell Benelux sensor no.1 at 180 °C and 550 kPa.
Download figure:
Standard image High-resolution imageFigure 11. The relative humidity deviation of the three Michell Benelux sensor at 180 °C and 550 kPa.
Download figure:
Standard image High-resolution imageFigure 12 shows an example of a data set obtained for determining the correction function. The data were collected during measurements of three sensors at 400 kPa with temperatures between 20 °C and 180 °C; the maximum dew-point temperature during the test was 132 °C. The data of all the sensors were combined to create a correction function with the relative humidity, h, and temperature, t, as input parameters:
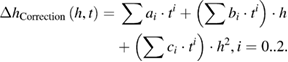
Figure 12. The deviation of the uncorrected relative humidity indication from the reference relative humidity for three sensors at 400 kPa and in the temperature range from 20 °C up to 180 °C.
Download figure:
Standard image High-resolution imageThe coefficients of the function are shown in table 5 and figure 13 shows the deviation of the corrected relative humidity indication for three sensors. While the uncorrected relative humidity indication has a scatter of up to 23%rh, the scatter for the corrected indication is reduced to less than 5%rh with a standard deviation of 1.2%rh.
Table 5. The coefficients for the ΔhCorrection—function.
i | ai/%rh · °C−i | bi/°C−i | ci/%rh−1 · °C−i |
---|---|---|---|
0 | 4.253 968 × 100 | 3.547 534 × 10−2 | 1.172 996 × 10−3 |
1 | −8.563 315 × 10−2 | −3.425 967 × 10−3 | −6.169 198 × 10−6 |
2 | 2.826 277 × 10−4 | −1.586 467 × 10−6 | 2.248 801 × 10−7 |
Figure 13. The deviation of the corrected relative humidity indication, using the new correction function, from the reference relative humidity for three sensors at 400 kPa and in the temperature range from 20 °C up to 180 °C.
Download figure:
Standard image High-resolution imageThe second type of sensor was an acoustic sensor from Innovation Handling [14] (see figure 14), which uses resistance thermometers to measure the temperature and the speed of sound, together with the temperature, to calculate the relative humidity. Two instruments were tested at atmospheric pressure up to 100 °C and one of the two instruments was tested up to 120 °C and 550 kPa. The measurements with both instruments were used to verify the implemented relationship between the air speed and the relative humidity at atmospheric pressure and to determine the relationship at elevated pressure.
Figure 14. The Innovation Handling acoustic sensor mounted in the pressure chamber with pressure feedthrough mounted on the door.
Download figure:
Standard image High-resolution imageFigure 15 shows the relative humidity indication of the acoustic sensor at 80 °C and atmospheric pressure. With the implemented speed of sound relationship for atmospheric pressure the relative humidity deviation from the reference was less than 0.5%rh.
Figure 15. The test of Innovation Handling sensor no.2 at 80 °C and 100 kPa.
Download figure:
Standard image High-resolution imageFigure 16 shows the measurement of the speed of sound at 80 °C and three pressures: 100 kPa, 250 kPa and 500 kPa. At high pressure the sensitivity of the speed of sound to humidity is compressed.
Figure 16. The indicated speed of sound of the Innovation Handling acoustic humidity meter at 80 °C and 100 kPa (left), 250 kPa (middle) and 500 kPa (right).
Download figure:
Standard image High-resolution imageIn figure 17 the measured speed of sound is shown as function of the water mole fraction, temperature and pressure in the range from 80 °C to 120 °C and from 100 kPa to 500 kPa.
Figure 17. The indicated speed of sound of the Innovation Handling acoustic humidity meter as function of the amount fraction, temperatures and pressures.
Download figure:
Standard image High-resolution imageBased on the data obtained between 20 °C and 120 °C and 100 kPa and 500 kPa, an equation for the speed of sound, vUUT, was fitted with the temperature, t, and water mole fraction, X, as parameters:

Table 6 shows the coefficients of the fitted equation and the standard deviation of the fit is 0.4 m·s−1. The new equation was compared with literature data [15] in the range from 40 °C to 100 °C and up to 500 kPa. At low temperature the agreement was within 0.5 m·s−1 (see figure 18), but at high temperature the difference increases to more than 3 m·s−1. There are several effects which can contributed to the observed differences. The main effects are the CO2 content of the gas mixture and the geometry design of the speed of sound meter. During the experiments compressed air was used, whose CO2 content was not measured. It is therefore not known whether the gas was depleted or enriched in comparison to standard air (≈370 µmol · mol−1) used in the literature data. Also, the literature data is for free space, while the instruments used in the experiments used a channel of approximately 78 cm length, which reduces the speed of sound in comparison to the free space conditions [15]. This corresponds to the deviation seen in figure 18.
Table 6. The coefficients for the vUUT—function.
i | ai/m · s−1 · °C−i | bi/m·s−1·(µmol · mol−1)−i |
---|---|---|
0 | 3.336 340 × 102 | −2.085 331 × 100 |
1 | 6.087 494 × 10−1 | 4.884 975 × 10−5 |
2 | −4.705 447 × 10−4 | 3.112 114 × 10−11 |
Figure 18. The deviation of the measured speed of sound from the literature value as function from amount fraction, temperature and pressure.
Download figure:
Standard image High-resolution imageConclusion
The dew-point temperature range of the high temperature relative humidity setup was extended from 95 °C up to 150 °C. To our knowledge, no other traceable humidity generators based on such simple technique (combined flow mixing and bubbling) has been realized so far in a considerable volume (300 mm × 300 mm × 300 mm), the standard reported in [5] being based on a completely different approach (steam injection) and on a smaller test volume (<1 l).
The uncertainty estimated for the generated relative humidity is 0.2%rh at 5%rh and increases to 0.4%rh at 95%rh. The increased dew-point temperature allowed to extend the maximum relative humidity at 180 °C from 8%rh to 45%rh. Due to the use of an improved humidity generator, the temperature uniformity of the test chamber was also improved, thus reducing the air temperature uncertainty to a maximum of 0.2 °C.
The setup was used to test seven industrial sensors of two different types and manufacturer. A capacitive sensor was tested to determine the correction, needed for the transformation of the raw sensor indication to an actual relative humidity indication. A correction function was applied, which was able to produce an indication within 2%rh of the reference value over the temperature range from 20 °C up to 180 °C.
An acoustic sensor was tested in the range from 20 °C to 120 °C with pressures up to 550 kPa. The results were used to investigate the performance of the sensor at high temperatures and to determine the speed of sound, applicable to the sensor readings, for high pressures. Using the data, a simple equation was found, resulting in a standard deviation of 0.4 m · s−1 for the speed of sound.
Acknowledgments
This work was jointly funded by the Ministry of Economic Affairs, The Netherlands and by the European Commission through the EMPIR Program, Project 14IND11, 'Metrology for Humidity at High Temperatures and Transient Conditions'.