Abstract
The popularity of coated aluminum is gaining significant attention in numerous sectors in the industry due to its specific strength, corrosion resistance, and recyclability. However, because of friction, its lifetime reduces which causes a billion-dollar loss every year to our property. Many types of research are going around the world on how friction and wear loss can be reduced. This research focuses on the tribological study of coated aluminum in different conditions in the experiments, lubricant is used to find its efficiency, and coating materials have also its self-lubricating properties. Both reciprocating motion of pin and simultaneous motion of pin and disc applied. The combined effects of lubrication and motions are correlated with the reduction of tribological properties to a certain extent. The velocity of both pin and disc is also varied. Applied loads are changed in different experiments as well. Roughness analysis has also been done to observe the effect of lubricant, motion, and applied load on the surface of the specimens. SEM, EDX, XRD, and FTIR tests are also performed to check the morphology of the specimens. The experiments show that comparatively less friction and wear are in at lubricated, reciprocating, and less velocity of pin and disc conditions. Less coefficient of friction is observed at higher applied load but less wear is produced at lower applied load. The Machine Learning (ML) approach is used to detect patterns automatically in datasets and create models to predict future data or other outcomes.
Export citation and abstract BibTeX RIS

Original content from this work may be used under the terms of the Creative Commons Attribution 4.0 licence. Any further distribution of this work must maintain attribution to the author(s) and the title of the work, journal citation and DOI.
1. Introduction
Aluminum has excellent properties for being utilized in different industries such as automotive, marine, and aerospace for high strength to weight ratio, light density, cracking toughness good ductility, low cycle fatigue resistance, and low cost [1–4]. Unfortunately, low hardness and poor lubricating property under dry sliding conditions limit their applications in the industry [5, 6]. Besides, poor wear resistance is seen when they are applied to tribological machine parts. As a result, the service life of different components decreases [7]. That is why it has become an important duty for the researchers to invent ways of increasing of wear resistivity of this material to increase their service life.
Aluminum is coated with different materials to improve the tribological properties. From the literature, it is known that Cr-based coatings show a promising advantage [8–11]. It shows excellent results in dry machining conditions and in reciprocating motion conditions [12]. Ni is another material that is frequently used to coat aluminum and applied for various applications. It is used in aviation, aerospace, automotive, and machinery due to its excellent tribological properties, hardness, wear resistance, corrosion-resistant properties, and lubricity [13, 14]. Besides, Cr and Ni, Cu is also used as a coating material so that it can be applied in industry in the tribological environment [15].
In some mechanisms, both reciprocating and rotating motion is required simultaneously. From literature [16, 17], the friction and wear in reciprocating motion are lower than that of rotating motion and in some cases, the different trends are also observed. But, the trends of friction and wear under simultaneous motion are not clearly understood. In this work, both motions are considered to find out the exact nature of friction and wear. The practical examples of applications of simultaneous motion are slider-crank mechanism, linear-rotary motor or actuator (linear-rotary motors can be used to perform complex tasks, such as threading in, closure, transferring, stacking, aligning, adhesive dispensing, electronic packaging, and optoelectronic applications and many others with just a single component), a rotary-linear switched reluctance motor for automotive applications, linear-rotary joint for robotics applications [18–23].
By applying the knowledge of machine learning (ML), the tribological characteristics of the materials can be improved. The ML methods can detect patterns automatically in datasets and create models to predict future data or other outcomes [24–26]. On the basis of literature, future opportunities and challenges, and concerning the practical applications in industry, the parameters are chosen for the ML model and experimental data. In the case of experimentations, there are several parameters such as, surface roughness, relative motion, type of material, type of lubrication, type of coating, temperature, normal load, sliding velocity, hardness, relative humidity, vibration, area of contact, rubbing duration, etc are attributed with friction and wear.
In this study, lightweight aluminum is coated by three layers for producing self-lubricating properties of coated surfaces. Moreover, multidirectional motions are created artificially. Both of these conditions are used for reducing friction and wear so that these coated materials are suggested to the improvement of different concerning mechanical and tribological systems in the industry. The reduction of friction and wear results in lowering the energy consumption, increase the life period of the tribo-components, and ensuring the productivity that reflects the economic growth under sustainable conditions.
The lubricants are introduced in the mating surfaces to reduce the tribological properties more and keep them at a minimal level. SAE 60 lubricant is used due to its excellent characteristics, such as high wear protection, excellent viscosity-temperature behavior, minimal frictional loss, high cleaning capability, high oxidation, and temperature stability, prevents black sludge formation [27].
Frictional behaviors are dependent on the motion [28–30]. The effects of motion in relation to sliding velocity, load, lubrication, the direction of motion, self-lubricating coating, surface roughness have some role on friction coefficient and that has been investigated in this study. That is, by better understanding the relationships of motion in conjunction with the related parameters, the mechanisms and systems can be designed and developed for the reduction of friction coefficient.
2. Methodology
2.1. Material preparation
Aluminum is used as disc material which is coated by chromium (Cr), copper (Cu), and nickel (Ni) using electrodeposition process. The different parameters such as current densities, the temperature of the bath, electrolyte composition, pH of the electrolyte, etc effects coating properties [31, 32]. The thickness of the coating was estimated from the cross-section of the test specimens and the thickness for Cr–Cu–Ni was about 22.60 μm.
The aluminum sheets are collected from the local market and these sheets are then cut by circular shape and size from the local workshop using a CNC lathe machine. The radius of the disc material is 50 mm and the thickness is 3 mm. The coating on aluminum (figure 1) is done by Jatrabari metal company, Dhaka.
Figure 1. Disc before the experiment.
Download figure:
Standard image High-resolution imageThe pin material is stainless steel of grade 304. The height of the pin is 48 mm with a 7 mm head. The diameter of the head is 6 mm which constitutes 41 mm and the diameter of the thinner part is 3 mm which constitutes 7 mm. A schematic diagram can be seen in figure 2 with proper dimensions. Chemical composition of pin can be seen in table 1.
Figure 2. Dimension of pin material drawn in CAD.
Download figure:
Standard image High-resolution imageTable 1. Chemical composition (%) of pin SS-304.
Si | Cr | Mn | Fe |
---|---|---|---|
0.47 ± 0.14 | 13.15 ± 0.49 | 8.82 ± 0.49 | 77.57 ± 0.66 |
2.2. Experimental procedure
The tribological experiments are done in a pin on the disc tribometer shown in figure 3. Three-layered galvanized based on aluminum is used as a disc material. The disc had 3 holes at the corners so that it can be screwed with the help of a screw. Only1 one type of stainless steel is used in the experiments as pin material. Both the linear motion of the pin and the simultaneous motion of the pin and disc are considered for the experiments. All the experiments are done at ambient temperature and air pressure.
Figure 3. Part of the experimental setup.
Download figure:
Standard image High-resolution imageExperiments are done both in dry and lubricated conditions. SAE 60 engine oil has been used as a lubricant. Total 48 numbers experiments are performed among which half are performed in linear motion of pin and the rest half are performed at the simultaneous motion of pin and disc. Total 12 numbers of experiments are performed in a lubricated environment. Each experiment is performed for 15 min and at every minute data is collected by a digital indicator. The linear motion of the pin ranged from 0.15 m s−1 to 0.25 m s−1. The circular motion ranged from 0.35 m s−1 to 0.45 m s−1. The applied loads are 1.5 N, 2.5N, 3.5N, and 4.5N. At the same condition, 4 experiments were performed to ensure accuracy. For example- at 0.15 m/s linear motion of pin, 0.45 m s−1 circular motion of disc and 3.5N applied load total of 4 experiments are performed. The reason behind using two types of conditions with lubricated and without lubricated conditions is to find the effectiveness of the lubricant. Wear rate was measured by calculating the mass loss of the pin and disc after rubbing for a specified duration. Initial and final mass loss of the pin and disc before and after rubbing was calculated on a high-resolution weighing scale. The formula used for calculating wear rate is as follows:

During experimentation, each test was repeated five times with a new sample of pin and disc under identical conditions and the average value was taken [33, 34]. The load cells (TML, Tokyo Sokki Kenkyujo Co. Ltd, CLS-100NA, Serial no. MR2947) were incorporated to determine the forces creating on the pin. A data acquisition system was facilitated to determine the forces continually when the process is on and the data are sent immediately to the computer. The load cell and the digital indicator (TML, Tokyo Sokki Kenkyujo Co. Ltd, Model no. TD-93A), calibrated against a standard proving ring was used for measuring loads [33, 34]. The coefficient of friction was obtained by dividing the frictional force by the applied normal force (load).
The worn surface of the disc after experimentation is depicted in figure 4.
Figure 4. Disc after the experiment.
Download figure:
Standard image High-resolution image2.3. Characterization approaches
The differences of the coefficients of friction under different conditions have been analyzed by ML methods to predict the future data and regression models have been established. To best fit our model, we used quadratic polynomial. A quadratic equation is a 2nd-degree polynomial equation.

Moreover, for our given dataset degree is increasing with the nth value. So, Equations for Our polynomial degree 2 regression

The flow chart for data analysis with regression using the ML approach is shown in figure 5. The Codes used to generate ML graphs have been added in the appendix.
Figure 5. Flow chart for data analysis with regression.
Download figure:
Standard image High-resolution imageIn order to observe the surface morphology of the disc before and after the experiment, a scanning electron microscopy test is performed. Energy Disperse x-ray analysis is performed to find the presence of different elements in the disc material. X-ray diffraction analysis is performed to obtain the crystallographic structure. Fourier-transform infrared spectroscopy test is done to show the presence of bands in the disc material.
3. Results and discussion
3.1. Surface coating analysis
3.1.1. Analysis of the impacts of coating on tribology
One strategy to lowering the values of friction and wear of a surface incorporates self-lubricating coatings (figure 6). Self-lubricating coating is deposited on the substrate in such a way so that the interfacial surfaces exhibit low shear strength causing interlayer sliding. Low shear strength results in a low adhesion between the coated substrate and the pin material which reduce the friction and wear. The coating thickness, coating surface roughness, relative hardness coating and substrate and lubricity effects of coated materials are also some considerable factors for the variation of friction and wear [35–37].
Figure 6. Effect of coating as self-lubricant.
Download figure:
Standard image High-resolution image3.1.2. Roughness analysis of the samples
Figure 7 shows the roughness analysis of the samples before and after tribological tests. The length in the x-axis ranged 7.5 mm for all the samples and the roughness tests range based on the surface profile of the sample. Figure 7(a) shows the less surface roughness with the Ra value 0.2 μm because the surface is coated and no tribological test has been done. Figures 7(b) and (c) show the higher surface roughness having Ra value 1.90 μm and 1.70 μm respectively. These two figures show higher surface roughness because the tribological tests have been performed in a dry conditions where for figure 7(b), the simultaneous motion of pin, and disc and for figure 7(c) reciprocating motion of pin have been applied. During rubbing action, the friction and wear under the motions and lubrications are seemed to be higher, produce more roughing of the surfaces. Under the simultaneous motion, more friction and wear are evident in comparison to reciprocating motion. When rubbing occurs, the simultaneous motion generates high rougher surfaces than that reciprocating motion. Higher friction and wear, higher roughing surfaces imitated. When the surfaces are contaminated with lubricants, reciprocating motion causes a small amount of surface roughness which results in small friction and wear. In contrast, the reciprocating motion with lubricants in relation to lubricated surfaces under reciprocating motion creates more roughening which gives rise to more friction. But it can be assured that the friction, wear, and roughness is apparent to lower in lubricating conditions whenever these parameters are compared under dry conditions. The quantitative trends of roughening surfaces are also confirmed by the SEM image spectra. Surface roughness plays a key role that influences the tribological property of surfaces, when the surface roughness is produced due to rubbing action in a combination of different motions, asperities of the surfaces are interlocking or deformation are occurred causes more friction and wear. As the roughness is created in the surfaces in different patterns due to distinct nature motions, surface irregularities are observed. Friction increases are generally attributed to close contact between surface irregularities [38, 39]. Surface irregularities can happen in three different forms [40, 41]: (i) roughness produces due to material removal mechanisms (ii) waviness, created due to the impact of the motions which are created artificially or induced vibration, and (iii) errors of form, when the abnormality can be occurred due to non-controllable parameters. Besides, the maximum measured contact area correlates with higher COF [27]. On the contrary, figures 7(d) and (e) show the lowest surface roughness with Ra value 1.0 μm and 0.50 μm respectively. This is because for both figures, the tribological tests have been performed in a lubricated condition where for figure 7(d), the tribological test has been performed in simultaneous motion of pin, and disc and for figure 7(e), the tribological test has been performed in reciprocating motion of pin. The reason for less surface roughness in the lubricated conditions is the formation of tribo-layer on the surface of the disc which minimizes the surface area.
Figure 7. Roughness analysis of sample (a) before the tribological test, (b) at the simultaneous motion of pin and disc at dry condition, (c) at the reciprocating motion of pin at dry condition, (d) at the simultaneous motion of pin and disc at lubricated condition, (e) at the reciprocating motion of pin at lubricated condition.
Download figure:
Standard image High-resolution image3.1.3. SEM analysis of the coated samples
From the scanning electron microscopy test of coated samples at different magnifications, it is clearly observed that the samples are clean (figure 8). No micro crack, micropore, or other effects are observable.
Figure 8. SEM analysis of the coated sample before the tribological test, (a) at 500 μm magnification, (b) at 300 μm magnification, (c) at 200 μm magnification, (d) at 100 μm magnification.
Download figure:
Standard image High-resolution image3.1.4. EDS analysis of the coated samples
The EDX micrographs of full area Aluminum coated with 20% Cr, 40% Cu, and 60% Ni are represented in figure 9. The maximum percentage of the composition contained Cr. The EDX spectra show the presence of other elements such as Ni and Cu. A strong peak of Cr is can be observed in the spectra. The comparatively less strong peaks of Ni and Cu are also seen.
Figure 9. Energy dispersive x-ray analysis of aluminum disc sample.
Download figure:
Standard image High-resolution image3.1.5. XRD analysis of the coated samples
Figure 10 represents the x-ray diffraction patterns of the sample. The phases present in the structure are consistent with the SEM and EDX findings. The peaks present in the figure confirm the crystal structure of the sample.
Figure 10. X-ray diffraction analysis of aluminum disc sample.
Download figure:
Standard image High-resolution imageNo peak is observable in the FTIR analysis of the sample in figure 11. A homogeneous line is seen having different bands including C–O, C=C, C–H, N–H. The presence of these bands does not make any special effect on the material property.
Figure 11. FTIR analysis of aluminum disc sample.
Download figure:
Standard image High-resolution image3.1.6. Thin film adhesion testing
The thin film adhesion performance of the multilayers and deposits of Cr, Cu, and Ni on Al was investigated by using cross-hatch adhesion testing method according to the ASTM D3359 for comparisons. The test was conducted by scratching on the plated surface followed by a peeling operation using adhesive tape as shown in figure 12. The adhesion scale ranging from 5B (100% adhesion) to 1B (poor adhesion, more than 60% of the deposited substrate [42]. The results indicate that a higher adhesion class 5B attributed 100% and 4B (90%) adhesion were exhibited by the electrodeposition method. And moderately higher. These particular properties are possibly related to the cross-sectional investigations of SEM images that exhibited the presence of cracks which could be more significant at intermediate thickness.
Figure 12. Photographs of cross-hatch observation (a) Crosshatch for 5B and (b) Crosshatch for 4B.
Download figure:
Standard image High-resolution image3.1.7. Modulus of elasticity and hardness testing
Tensile test was performed on pure Al and deposited Al/Cr, Cu, Ni. The in-plane tensile results show that modulus of elasticity was found 68.5 GPa for pure Al and 76.6 GPa for coated Al. The tensile result confirmed that there is less influence of the coating stiffness on the film stiffness and very few tangible variations were observed which were effectively subjected by the substrates [43, 44].
The hardness measure of the specimen using Rockwell B scale and the results were observed are 54 for pure Al and 75 for coated Al using substrate Cr, Cu, Ni. These results also signify that coated materials increased the hardness of the Al that was effectively subjected by the substrates Cr, Cu, and Ni.
3.2. Effect of lubrication
3.2.1. Coefficient of friction
In all the experiments it is seen that less coefficient of friction and less wear is observed when lubricant is used which is because of the properties of the lubricant. From figure 13 which has been drawn comparing the effect of lubrication in both simultaneous motion and reciprocating motion at 3.5 N applied force, 0.45 m s−1 disc velocity, and 0.15 m s−1 pin velocity, it is seen that the minimum coefficient of friction is found at lubricated condition both in a simultaneous and reciprocating motion and literature shows the similar results [40]. At the simultaneous motion of pin and disc but without lubricant, the initial coefficient of friction is found 0.176 which increases with time and reaches the maximum value of 0.184 after 9 min of friction. After 13 min of friction test, it decreases again and reached 0.18 after 15 min. The reciprocating motion of pin but without lubricant as well the initial coefficient of friction is found 0.169 which increases with time. It reaches the maximum value of 0.177 after 9 min of friction. The value then decreases after 12 min of friction and reached 0.172 after 15 min. At the simultaneous motion of pin, and disc and at the lubricated condition, the coefficient of friction is seen much lower compared to without lubricated condition. In the beginning, the coefficient of friction is seen as 0.142 which increases with time and reaches a maximum value of 0.151 after 10 min of friction. After 11 min of friction, it starts to decline again and finally reaches 0.148 after 15 min of friction. Similarly, at the reciprocating motion of pin and at without lubricated condition the coefficient of friction is seen 0.135 which rises up with time and reaches the maximum value after 0.142 after 12 min of friction. Finally, it reaches 0.139 after 15 min of friction. Less coefficient of friction is observed at lubricated conditions compared to dry conditions because of the formation of trilayer on the surface of the coated samples [39]. When the lubricant is applied between the contacting surfaces, thin films of lubrication separate the pin and disc (figure 14). This separation causes the reduction of area of contact between the mating surfaces which in turn reduces the friction and wear. Moreover, due to the lubrication effects, the roughing surfaces change into wet and smoother surfaces which are also responsible for lower frictional parameters [45, 46]. Comparison of friction at different conditions can be seen at table 2.
Figure 13. Coefficient of friction at 3.5 N applied force, 0.45 m s−1 disc velocity and 0.15 m s−1 pin velocity.
Download figure:
Standard image High-resolution imageFigure 14. Analysis the effect of lubricant on friction and wear mechanism.
Download figure:
Standard image High-resolution imageTable 2. Comparison of friction at different conditions.
SL. | Friction at 3.5N applied force, 0.45 m s−1 disc velocity, 0.15 m s−1 pin velocity, and without lubricant | Comparison of friction at 3.5N applied force, 0.15 m s−1 pin motion and without lubricant with the first one (%) | Comparison of friction at 3.5N applied force, 0.45 m s−1 disc motion 0.15 m s−1 pin motion and with lubricant with the first one (%) | Comparison of friction at 3.5N applied force, 0.15 m s−1 pin motion and with lubricant with the first one (%) |
---|---|---|---|---|
1 | 0.17634 | −3.969604 | −19.22423 | −23.17682 |
2 | 0.17798 | −3.933026 | −19.13136 | −23.11496 |
3 | 0.17998 | −4.094899 | −20.03 | −23.96933 |
4 | 0.17961 | −3.897333 | −19.03569 | −23.04994 |
5 | 0.18125 | −3.862069 | −18.94621 | −22.99034 |
6 | 0.18125 | −3.862069 | −18.94621 | −22.99034 |
7 | 0.18125 | −3.862069 | −18.12414 | −22.24 |
8 | 0.18289 | −3.827437 | −18.03817 | −22.93728 |
9 | 0.18452 | −3.793627 | −18.76219 | −22.87557 |
10 | 0.18452 | −3.793627 | −17.95469 | −23.61804 |
11 | 0.18452 | −3.793627 | −17.94927 | −23.61804 |
12 | 0.18489 | −4.132187 | −18.91936 | −23.02991 |
13 | 0.18452 | −4.677 | −18.75677 | −23.61804 |
14 | 0.18216 | −3.442029 | −18.53316 | −23.37505 |
15 | 0.18016 | −4.190719 | −17.62322 | −22.52442 |
When we do regression analysis of table 3, we get 3 separate regression models for each case (figure 15). These are blue, red, and green regression models. The blue regression line shows the comparison of values when we change from friction at 3.5N applied force, 0.45 m s−1 disc velocity, 0.15 m s−1 pin velocity, and without lubricant to friction at 3.5N applied force, 0.15 m s−1 pin motion, and without lubricant. The values start from 0.17 and gradually increase from 0.17 to 0.18. We can see the change from −4% to −3%. The red regression line shows the comparison of values when we change from friction at 3.5N applied force, 0.45 m s−1 disc velocity, 0.15 m s−1 pin velocity, and without lubricant to friction at 3.5N applied force, 0.45 m s−1 disc motion 0.15 m s−1 pin motion, and with lubricant. The values start from 0.17 and gradually increase from 0.17 to 0.18. We can see the change from −19% to −17%. The green regression line shows the comparison of values when we change from friction at 3.5N applied force, 0.45 m s−1 disc velocity, 0.15 m s−1 pin velocity, and without lubricant to friction at 3.5N applied force, 0.15 m s−1 pin motion, and with lubricant. The values start from 0.17 and gradually increase from 0.17 to 0.18. we can see the change from −23% to −22%.
Table 3. Comparison of wear rate at different conditions.
SL. | Wear rate at 3.5N applied force, 0.45 m s−1 disc velocity, 0.15 m s−1 pin velocity, and without lubricant | Comparison of wear rate at 3.5N applied force, 0.15 m s−1 pin motion and without lubricant with the first one (%) | Comparison of wear rate at 3.5N applied force, 0.45 m s−1 disc motion 0.15 m s−1 pin motion and with lubricant with the first one (%) | Comparison of wear rate at 3.5N applied force, 0.15 m s−1 pin motion and with lubricant with the first one (%) |
---|---|---|---|---|
1 | 0.403 | −65.26055 | −86.6005 | −94.78908 |
Figure 15. Regression model for the coefficient of friction at 3.5 N applied force, 0.45 m s−1 disc velocity, and 0.15 m s−1 pin velocity.
Download figure:
Standard image High-resolution image3.2.2. Wear rate
From figure 16 which has been drawn comparing the effect of lubrication in both simultaneous motion and reciprocating motion at 3.5 N applied force 0.45 m s−1 disc velocity and 0.15 m s−1 pin velocity, it is seen that the minimum wear rate is found at lubricated condition both in a simultaneous and reciprocating motion and literature shows the similar results [27]. Maximum 0.403g of wear is produced after 15 min of friction test when the simultaneous motion of pin and disc is applied without lubricated condition. A reciprocating motion of pin and at without lubricated condition, 0.14g wear is produced after 15 min of friction test which is 65.26% less compared to the first one. At the simultaneous motion of pin and disc and with the lubricated condition, 0.054g wear is produced which is 86.6% less compared to the first one. A reciprocating motion of pin and at without lubricated condition, 0.021g wear is produced which is 94.78% less compared to the first one.
Figure 16. Wear rate at 3.5 N applied force, 0.45 m s−1 disc velocity, and 0.15 m s−1 pin velocity.
Download figure:
Standard image High-resolution image3.2.3. SEM analysis
Comparatively less rubbing effect and less wear are seen in the SEM analysis when the tribological analysis was performed at lubricated conditions. From the SEM analysis of the sample where tribological analysis was performed 3.5 N applied force, 0.15 m s−1 pin velocity, 0.45 m s−1 disc velocity, and at lubricated condition, rubbing effect and abrasive wear are visible (figure 17). The rubbing effect can be seen at 500 μm image (figure 17(a)). both wear and rubbing effects are easily observable at 300 μm, 200 μm, and 100 μm images (figures 17(b)–(d)).
Figure 17. SEM analysis of the sample after tribological test at 3.5 N applied force, 0.45 m s−1 disc velocity, 0.15 m s−1 pin velocity and at lubricated condition, (a) at 500 μm magnification, (b) at 300 μm magnification, (c) at 200 μm magnification, (d) at 100 μm magnification.
Download figure:
Standard image High-resolution image3.3. Effect of motion
3.3.1. Coefficient of friction
Both pin and disc motion plays an important role in determining the coefficient of friction (figure 18). All the lines drawn here are without lubricated condition and at 2.5 N applied force. Here, the maximum coefficient of friction is observed at 0.25 m s−1 pin velocity and 0.45 m s−1 disc velocity. At the beginning of the experiment, the coefficient of friction is observed as 0.239 which increases with the passage of time and fluctuated. The maximum coefficient of friction is found after 7, 8, 11, and 14 min of friction which is 0.248. The second maximum coefficient of friction is observed at 0.15 m s−1 pin velocity and 0.35 m s−1 disc velocity. In the beginning, the coefficient of friction is found 0.217 which reaches over the period and reaches the maximum value of 0.239 after 15 min of friction. The lowest coefficient of friction is seen at 0.15 m s−1 pin velocity where the disc was fixed. At the beginning of the friction test, the coefficient of friction is seen as 0.16 which fluctuated over the period and reached a maximum value at 6, 13, and 14 min. The second-lowest coefficient of friction is seen at 0.25 m s−1 pin velocity when the disc is kept fixed. Here, the initial coefficient of friction is seen as 0.177 which increases over the period and reached maximum value after 9 min of friction test. After 15 min of friction test, the coefficient of friction is seen as 0.183. Such behavior of decreasing coefficient of friction after a certain period of time can be related to the formation of tribo-layers during rubbing [47, 48]. Simultaneous motion of pin and disc makes more friction compared to reciprocating motion of pin. This is because, the simultaneous motion of the pin makes two types of motion, and as a result, it gets in touch with more surface area which makes more friction. Comparison of friction at different conditions can be seen at table 4.
Figure 18. Coefficient of friction at 2.5 N applied force and without lubricant.
Download figure:
Standard image High-resolution imageTable 4. Comparison of friction at different conditions.
SL. | Friction at 2.5N applied force, 0.45 m s−1 disc velocity, 0.25 m s−1 pin velocity, and without lubricant | Comparison of friction at 2.5N applied force, 0.25 m s−1 pin velocity and without lubricant with the first one (%) | Comparison of friction at 2.5N applied force, 0.35 m s−1 disc velocity, 0.15 m s−1 pin velocity and without lubricant with the first one (%) | Comparison of friction at 2.5N applied force, 0.15 m s−1 pin velocity and without lubricant with the first one (%) |
---|---|---|---|---|
1 | 0.23963 | −26.0944 | −9.431206 | −33.18867 |
2 | 0.24183 | −26.12993 | −8.435678 | −33.79647 |
3 | 0.24403 | −26.16482 | −8.359628 | −33.76224 |
4 | 0.24623 | −26.82451 | −7.878812 | −34.35406 |
5 | 0.24403 | −25.53784 | −5.655042 | −33.57374 |
6 | 0.24623 | −25.57771 | −6.49799 | −33.54181 |
7 | 0.24843 | −25.61687 | −6.440446 | −35.37012 |
8 | 0.24843 | −25.61687 | −6.440446 | −35.58346 |
9 | 0.24623 | −24.33091 | −4.711043 | −34.79267 |
10 | 0.24623 | −24.95228 | −4.711043 | −34.8211 |
11 | 0.24843 | −25.61687 | −4.669323 | −35.37012 |
12 | 0.25063 | −26.88425 | −6.383913 | −35.32299 |
13 | 0.25063 | −27.4987 | −5.506125 | −34.70853 |
14 | 0.24843 | −26.85666 | −4.669323 | −34.13034 |
15 | 0.25063 | −26.88425 | −4.628337 | −35.32299 |
When we do regression analysis of table 5, we get 3 separate regression models for each case (figure 19). These are blue, red, and green regression models. The blue regression line shows the comparison of values when we change from friction at 2.5N applied force, 0.45 m s−1 disc velocity, 0.25 m s−1 pin velocity, and without lubricant to friction at 2.5N applied force, 0.25 m s−1 pin velocity, and without lubricant. The values start from 0.23 and gradually increase from 0.23 to 0.25. We can see that these values are changing increasingly and decreasingly. The red regression line shows the comparison of values when we change from friction at 2.5N applied force, 0.45 m s−1 disc velocity, 0.25 m s−1 pin velocity, and without lubricant to friction at 2.5N applied force, 0.35 m s−1 disc velocity, 0.15 m s−1 pin velocity, and without lubricant. The values start from .23 and as gradually increase from .23 to .25. We can see the change from −9% to −4%. The green regression line shows the comparison of values when we change from friction at 2.5N applied force, 0.45 m s−1 disc velocity, 0.25 m s−1 pin velocity, and without lubricant to friction at 2.5N applied force, 0.15 m s−1 pin velocity, and without lubricant. The values start from 0.23 and gradually increase from 0.23 to 0.25. We can see the change from −33% to −35%.
Table 5. Comparison of wear rate at different conditions.
SL. | Wear rate at 2.5N applied force, 0.45 m s−1 disc velocity, 0.25 m s−1 pin velocity, and without lubricant | Comparison of wear rate at 2.5N applied force, 0.25 m s−1 pin velocity and without lubricant with the first one (%) | Comparison of wear rate at 2.5N applied force, 0.35 m s−1 disc velocity, 0.15 m s−1 pin velocity and without lubricant with the first one (%) | Comparison of wear rate at 2.5N applied force, 0.15 m s−1 pin velocity and without lubricant with the first one (%) |
---|---|---|---|---|
1 | 0.384 | −63.02083 | −15.625 | −67.44792 |
Figure 19. Regression model for coefficient of friction at 2.5 N applied force and without lubricant.
Download figure:
Standard image High-resolution image3.3.2. Wear rate
From figure 20 which has been drawn comparing the effect of pin velocity in both simultaneous motion and reciprocating motion at 2.5 N applied force and without lubrication, it is seen that minimum wear rate is found at reciprocating motion and with lower pin velocity. Maximum 0.384g wear is produced at 0.25 m s−1 pin velocity and 0.45 m s−1 disc velocity after 15 min of friction test. At 0.15 m s−1 pin velocity and 0.35 m s−1 disc velocity, 0.324g wear is produced which is 15.62% less compared to the first one. When pin velocity is maintained at 0.25 m s−1 and disc are kept fixed, 0.142g wear is produced which is 63.02g less compared to the first one. At 0.15 m s−1 pin velocity and keeping the disc fixed, 0.125g wear is produced which is 67.44g less compared to the first one [49, 50]. Simultaneous motion of pin and disc makes more wear compared to reciprocating motion of pin. This is because, the simultaneous motion of the pin makes two types of motion, and as a result, it gets in touch with more surface area which makes more wear.
Figure 20. Wear rate at 2.5 N applied force and without lubricant.
Download figure:
Standard image High-resolution image3.3.3. SEM analysis
SEM analysis of the sample at 1.5 N applied force, 0.2 m s−1 pin velocity and without lubricating condition where the disc was fixed and samples are after the friction test, it is seen that it shows different morphology compared the images of before tribological test and rubbing effects, and micro-cracks [51] are observable (figure 21). Rubbing effects and micro-cracks are observable at 500 μm image (figure 20(a)). Rubbing effects are clearly observable in other images of 300 μm, 200 μm, and 100 μm as well (figures 20(b)–(d)).
Figure 21. SEM analysis of the sample after tribological test at 1.5 N applied force, 0.2 m s−1 pin velocity and at without lubricating condition, (a) at 500 μm magnification, (b) at 300 μm magnification, (c) at 200 μm magnification, (d) at 100 μm magnification.
Download figure:
Standard image High-resolution image3.4. Effect of applied load
3.4.1. Coefficient of friction
From figure 22 which has been drawn comparing the effect of applied force in both simultaneous motion and reciprocating motion at 0.45 m s−1 disc velocity and 0.2 m s−1 pin velocity and without lubrication, it is seen that the minimum coefficient of friction is found at higher applied force and a reciprocating motion. From the figure, it is clearly observable that the maximum coefficient of friction is obtained at 1.5 N applied force when both pin and disc were moveable. At the beginning of the friction test, the coefficient of friction is seen as 0.497. The coefficient of friction fluctuates over the period and reached the maximum value of 0.525 after 8 min of friction. After 15 min of friction, the coefficient of friction reaches 0.514. When a disc is kept fixed at 1.5 N applied force, the initial coefficient of friction is seen as 0.435. The value of the coefficient of friction fluctuates over the period and reaches a maximum value of 0.444 after 4, 5, 10, and 12 min of friction test. After 15 min of the friction test, the coefficient of friction reaches 0.435 again. At 4.5 N applied force and when both pin and disc are kept moveable the coefficient of friction is found 0.224 at the beginning of the friction test. Though the value of the coefficient of friction fluctuated over the period a bit the value remains almost the same over the period. When a disc is kept fixed at 4.5 N applied force, the initial coefficient of friction is found 0.173 which reaches the maximum value of 0.179 after 7 min of friction test. After 15 min of the friction test, the final value of the coefficient of friction reaches 0.171. Wear of the coating first occurs on top of the asperities of the sliding surface resulting in increased surface area and a positive trend of the COF [52]. Comparison of friction at different conditions can be seen at table 6.
Figure 22. Coefficient of friction at 0.45 m s−1 disc velocity, 0.2 m s−1 pin velocity, and without lubricant.
Download figure:
Standard image High-resolution imageTable 6. Comparison of friction at different conditions.
SL. | Friction at 1.5N applied force, 0.45 m s−1 disc velocity, 0.2 m s−1 pin velocity, and without lubricant | Comparison of friction at 1.5N applied force, 0.2 m s−1 pin velocity and without lubricant with the first one (%) | Comparison of friction at 4.5N applied force, 0.45 m s−1 disc velocity 0.2 m s−1 pin velocity and without lubricant with the first one (%) | Comparison of friction at 4.5N applied force, 0.2 m s−1 pin velocity and without lubricant with the first one (%) |
---|---|---|---|---|
1 | 0.49792 | −12.65464 | −54.94457 | −65.27755 |
2 | 0.51641 | −15.78203 | −55.50628 | −66.20515 |
3 | 0.50716 | −13.33504 | −55.12067 | −65.2654 |
4 | 0.50716 | −12.42212 | −55.12067 | −65.2654 |
5 | 0.51179 | −13.2144 | −55.25899 | −65.26114 |
6 | 0.51641 | −14.8874 | −55.58955 | −65.57193 |
7 | 0.52104 | −15.64371 | −57.65968 | −65.5631 |
8 | 0.52491 | −17.1458 | −56.25726 | −66.12943 |
9 | 0.51953 | −17.17899 | −55.87358 | −66.09243 |
10 | 0.51416 | −13.61444 | −55.41271 | −66.37428 |
11 | 0.51416 | −14.51494 | −55.28824 | −66.69325 |
12 | 0.50491 | −12.03185 | −54.66717 | −65.75825 |
13 | 0.50953 | −14.64487 | −55.07821 | −65.74883 |
14 | 0.51416 | −16.31399 | −55.8017 | −66.37428 |
15 | 0.51416 | −15.41349 | −55.73168 | −66.69325 |
When we do regression analysis of table 7, we get 3 separate regression models for each case (figure 23). These are blue, red, and green regression models. The blue regression line shows the comparison of values when we change from friction at 1.5N applied force, 0.45 m s−1 disc velocity, 0.2 m s−1 pin velocity, and without lubricant to friction at 1.5N applied force, 0.2 m s−1 pin velocity, and without lubricant. The values start from 0.49 and gradually increase from 0.49 to 0.52. We can see that the values are continuously increasing and decreasing. The red regression line shows the comparison of values when we change from friction at 1.5N applied force, 0.45 m s−1 disc velocity, 0.2 m s−1 pin velocity, and without lubricant to friction at 4.5N applied force, 0.45 m s−1 disc velocity 0.2 m s−1 pin velocity, and without lubricant. The values start from 0.49 and gradually increase from 0.49 to 0.52. We can notice that these values are also volatile. That means its value is upward and downward. The green regression line shows the comparison of values when we change from friction at 1.5N applied force, 0.45 m s−1 disc velocity, 0.2 m s−1 pin velocity, and without lubricant to friction at 4.5N applied force, 0.2 m s−1 pin velocity, and without lubricant. The values start from 0.49 and gradually increase from 0.49 to 0.52. We can see the change from −65% to −66%.
Table 7. Comparison of wear rate at different conditions.
SL. | Wear rate at 1.5N applied force, 0.45 m s−1 disc velocity, 0.2 m s−1 pin velocity, and without lubricant | Comparison of wear rate at 1.5N applied force, 0.2 m s−1 pin velocity and without lubricant with the first one (%) | Comparison of wear rate at 4.5N applied force, 0.45 m s−1 disc velocity 0.2 m s−1 pin velocity and without lubricant with the first one (%) | Comparison of wear rate at 4.5N applied force, 0.2 m s−1 pin velocity and without lubricant with the first one (%) |
---|---|---|---|---|
1 | 0.336 | −59.82143 | +79.7619 | −34.52381 |
Comparison between surface roughness, COF and wear rate.
Figure 23. Regression model for the coefficient of friction at 0.45 m s−1 disc velocity, 0.2 m s−1 pin velocity, and without lubricant.
Download figure:
Standard image High-resolution image3.4.2. Wear rate
From figure 24 which has been drawn comparing the effect of applied force in both simultaneous motion and reciprocating motion at 0.45 m s−1 disc velocity and 0.2 m s−1 pin velocity and without lubrication it is seen that minimum wear rate is found at less applied force and a reciprocating motion. After 15 min of friction test at 1.5 N applied force and simultaneous motion of pin and disc 0.336 g wear is produced. At 1.5 N applied force and at the reciprocating motion of pin 0.135 g wear is produced which is the minimum and 59.82% less compared to the first one. At 4.5 N applied force and simultaneous motion of pin and disc, 0.604 g wear is produced which is the maximum and 79.76% more compared to the first one. At 4.5 N applied force and at the reciprocating motion of pin, 0.22 g wear is produced which is 34.53% less compared to the first one. Formation of wear increases with the increase of applied load [53, 54] as the contact area increases in relation to the nominal contact area and thus increases the frictional force between two contact sliding surfaces. The increased frictional force actual contact surface area caused severe wear. Therefore, the frictional thrust and shear force increases with the increase in applied load and thus accelerates the wear rate.
Figure 24. Wear rate at 0.45 m s−1 disc velocity, 0.2 m s−1 pin velocity, and without lubricant.
Download figure:
Standard image High-resolution imageFigure 25 shows the comparison between surface roughness, COF and wear rate at different conditions. From the figure, it can be clearly observed that lubricating conditions make less COF and wear because at these conditions the contact areas reduce for the mating surfaces. Besides, the reciprocating motion of pin makes less COF and wear compared to the simultaneous motion of the pin and disc as in reciprocating motion the pin gets in touch with less surface.
Figure 25. Comparison of surface roughness, COF, and wear rate.
Download figure:
Standard image High-resolution image3.4.3. SEM analysis
Rubbing effect and abrasive wear are clearly visible in figure 26 at different magnifications of the figures where tribological analysis has been performed at 4.5 N applied force, 0.2 m s−1 pin velocity, 0.45 m s−1 disc velocity, and without lubricated condition. Rubbing effects are visible at 500 μm (figure 26(a)). Both rubbing effect and abrasive wear [55] produced because of increased speed of pin and disc are easily seen 300 μm, 200 μm, and 100 μm images (figures 26(b)–(d)). Sliding tracks form abrasive wear on the surface of the samples [38].
Figure 26. SEM analysis of the sample after tribological test at 4.5 N applied force, 0.2 m s−1 pin velocity, 0.45 m s−1 disc velocity and at without lubricating condition, (a) at 500 μm magnification, (b) at 300 μm magnification, (c) at 200 μm magnification, (d) at 100 μm magnification.
Download figure:
Standard image High-resolution image4. Conclusion
From this research, the significant results are the minimization of coefficient of friction and wear rate at a lubricated condition where maximum 20% coefficient of friction and 86.6% wear rate in simultaneous motion of pin, and disc have been minimized and 24% coefficient of friction and 94.7% wear rate at reciprocating the motion of pin compared simultaneous motion of pin and disc at the lubricated condition to have been minimized. At less pin and disc velocity around 9.4% coefficient of friction and 15.6% wear rate at the simultaneous motion of pin and disc has been reduced and 35.4% coefficient of friction and 67.4% wear rate at the reciprocating motion of pin compared to the simultaneous motion of pin and disc are higher motion have been reduced. The minimum coefficient of friction is observed at a higher applied load where 57.6% coefficient of at simultaneous motion of pin and disc and 66.7% coefficient of friction have been minimized at the reciprocating motion of pin compared to the simultaneous motion of pin and disc at higher applied loads. Minimum wear rate is found at lower applied load. The regression model constructed from the variation of coefficient of friction shows a very small number of outliers. Further research can be carried out by changing the coating material on aluminum. In the case of simultaneous motion loads applied during experiments are in the range 1.5N to 4.5N. In this study, the critical values of forces applied for experimental setup in simultaneous motion are not analyzed. In future studies, the critical value of forces applied for experimental setup in simultaneous motion can be analyzed. The natural frequency of the experimental setup also is evaluated using dead weight and adding weights by the variation of amplitude and frequency.
Data availability statement
All data that support the findings of this study are included within the article (and any supplementary files).
Appendix
Codes used to generate ML graphs have been added here:
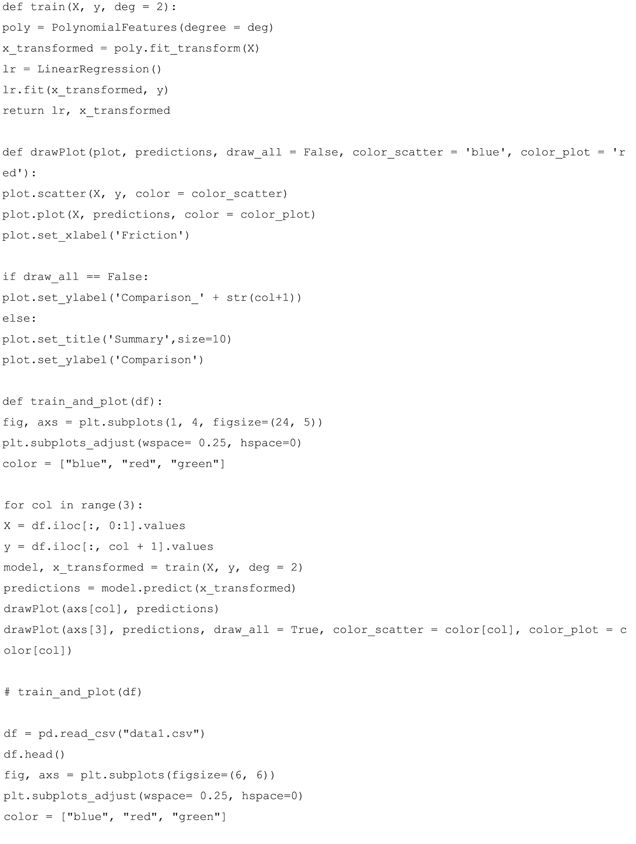
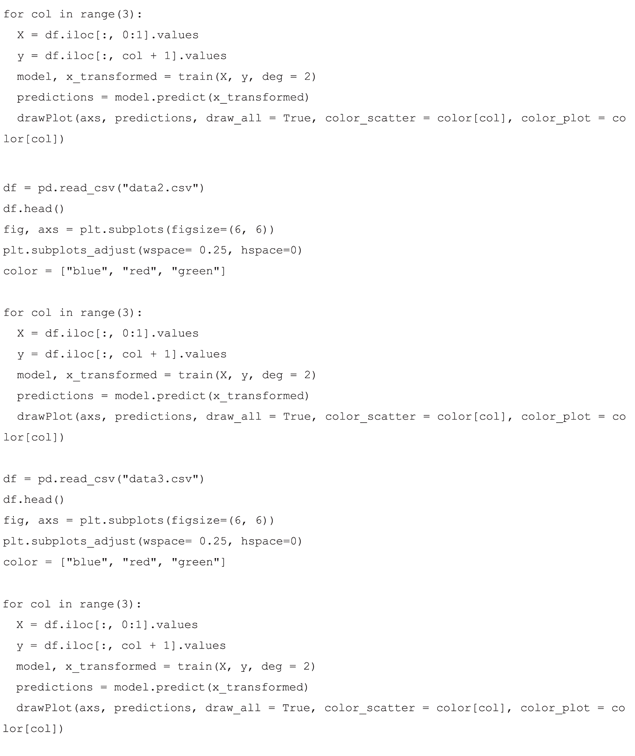