Abstract
In the recent technology over the Unmanned Aerial Vehicle (UAV), the implication of propeller contributes a principal part in the production of thrust by pushing the air with the rotating blades. Especially, propeller's incomparably works perfect in the advanced UAVs, because of its huge contribution to UAV's construction. Analyzing the structural behavior of propeller and its rotodynamic effects with the help of advanced engineering approaches can provide better performance and lifetime in advanced operating conditions. The composites of CFRP (Carbon Fiber Reinforced Polymer) and GFRP (Glass Fiber Reinforced Polymer) are widely used for the propellers, due to the advantage of load resisting capacity, lightweight, higher production. This work deals with the comparative studies of the propeller with the different composites such as CFRP and GFRP to inculcate the structural characteristics of deformation with respect to the applied load, maximum stress, and normal stress by coupled cum advanced simulations for different rotational velocities. The primary outcome of these comparative studies is providing the optimized performance as well as its ultimate lifetime of the rotor component for an advanced UAV. Finally, material optimizations are executed for UAV's propeller by using two advanced numerical methodologies that are FSI (Fluid-Structure Interaction) for the evaluation of structural parameters and coupling of CFD (Computational Fluid Dynamics) - MRF (Moving Reference Frame) for the representation of rotating nature of propeller. Through these approaches and grid convergence test, the best composite material is finalized, which is GFRP. Especially, Epoxy-E-Glass UD and Epoxy-S-Glass-UD are performed better than other composite materials, wherein the Epoxy-E-Glass-UD is reacted low deformed value of 3.7829μm and Epoxy-S-Glass-UD is induced low stress value f 55556Pa than other composites at average loading conditions.
Export citation and abstract BibTeX RIS
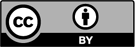
Content from this work may be used under the terms of the Creative Commons Attribution 3.0 licence. Any further distribution of this work must maintain attribution to the author(s) and the title of the work, journal citation and DOI.